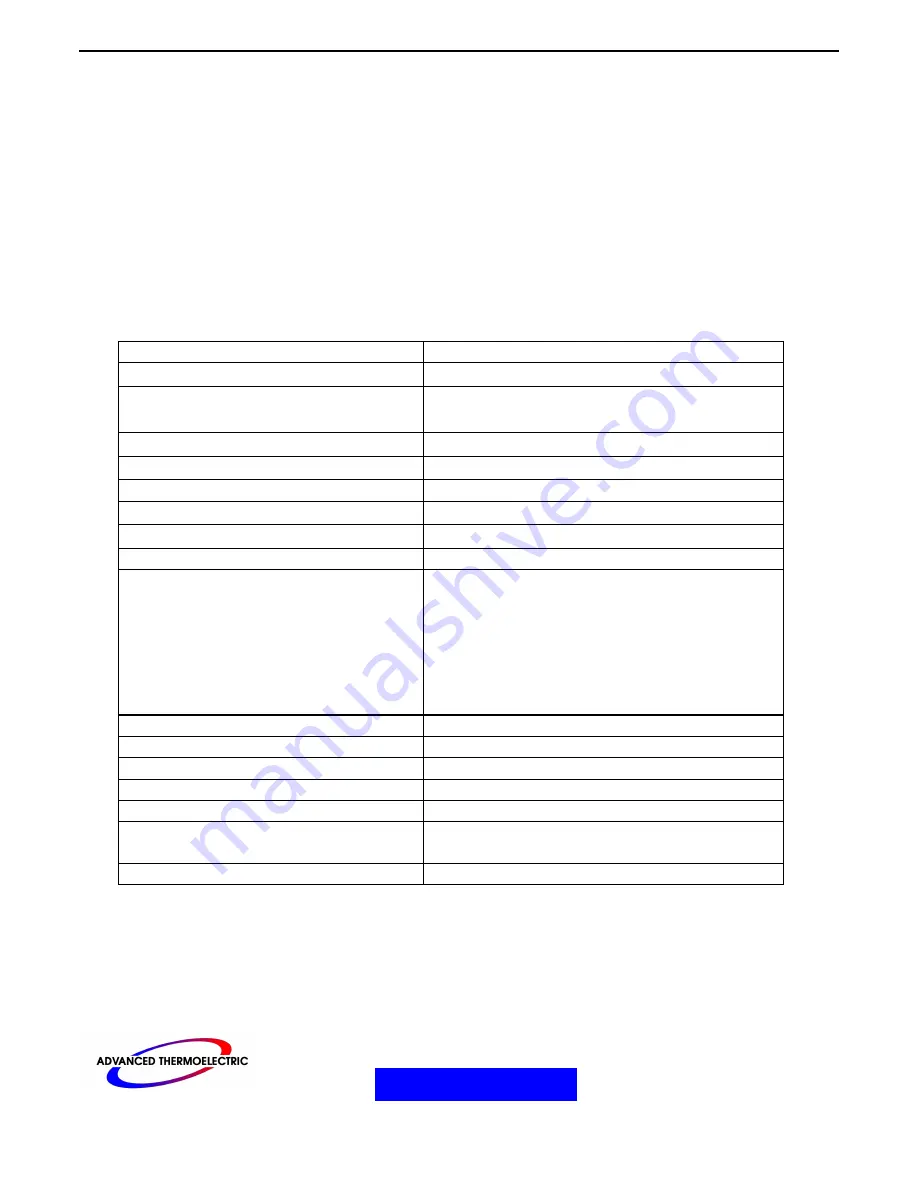
ElectraCOOL
LA550 Chiller
For Information Call
1 800-250-2920
electracool.com
One Tara Boulevard
Nashua, NH 03062 USA
international Inquiries (603) 888-2467
rev 7/03
1
1.0 Introduction
The
ElectraCOOL
LA550 Chiller is a thermoelectric temperature control system
designed to meet RTCA DO-160D requirements for use in aircraft. The chiller
circulates 1.2 gpm of constant temperature coolant for controlling laser package
temperatures and other temperature sensitive systems. It does not use Freon
or any other replacement gas. From conception, this chiller has been designed
for long life and ease of use. The internal thermoelectric modules have lifetimes
greater than 200,000 hours.
2.0 Specifications
Process Fluid Type:
Water, Ethylene Glycol 50/50
Ambient Air Operating Range:
5
°
C to 40
°
C
Cooling Capacity @25
°
C with
25
°
C Ambient Air :
600W
Control Accuracy:
±
0.5
°
C
Storage Temperature Range
-20
°
C to 60
°
C
Humidity
95% minimum non condensing
Set-point Range:
-10
°
C to +50
°
C
Temperature probe:
100
Ω
Platinum RTD, 3 Wire
Process Pump Capacity :
1.2 gpm @ 35 psi
Process Fluid Connections:
3/8” DESO Quick Disconnect,
Minimal Spillage on 90
°
elbow for
space constraint
Parker FS-371-6FP inlet (Female)
Parker FS-372-6FP outlet (Male)
Include mating connectors (3/8”NPT
Female ends)
Input Power :
27.5 VDC Nominal @ 1000W
Input Voltage Range:
22 to 30.3VDC
Abnormal Input Voltage
20.5 to 32.5 VDC for 5 min
System Proof Pressure :
100 psi
Process Fluid Reservoir:
1 Liters
Dimensions:
19” rack mount , 14” high, 16.5”
deep
Weight :
65 lbs