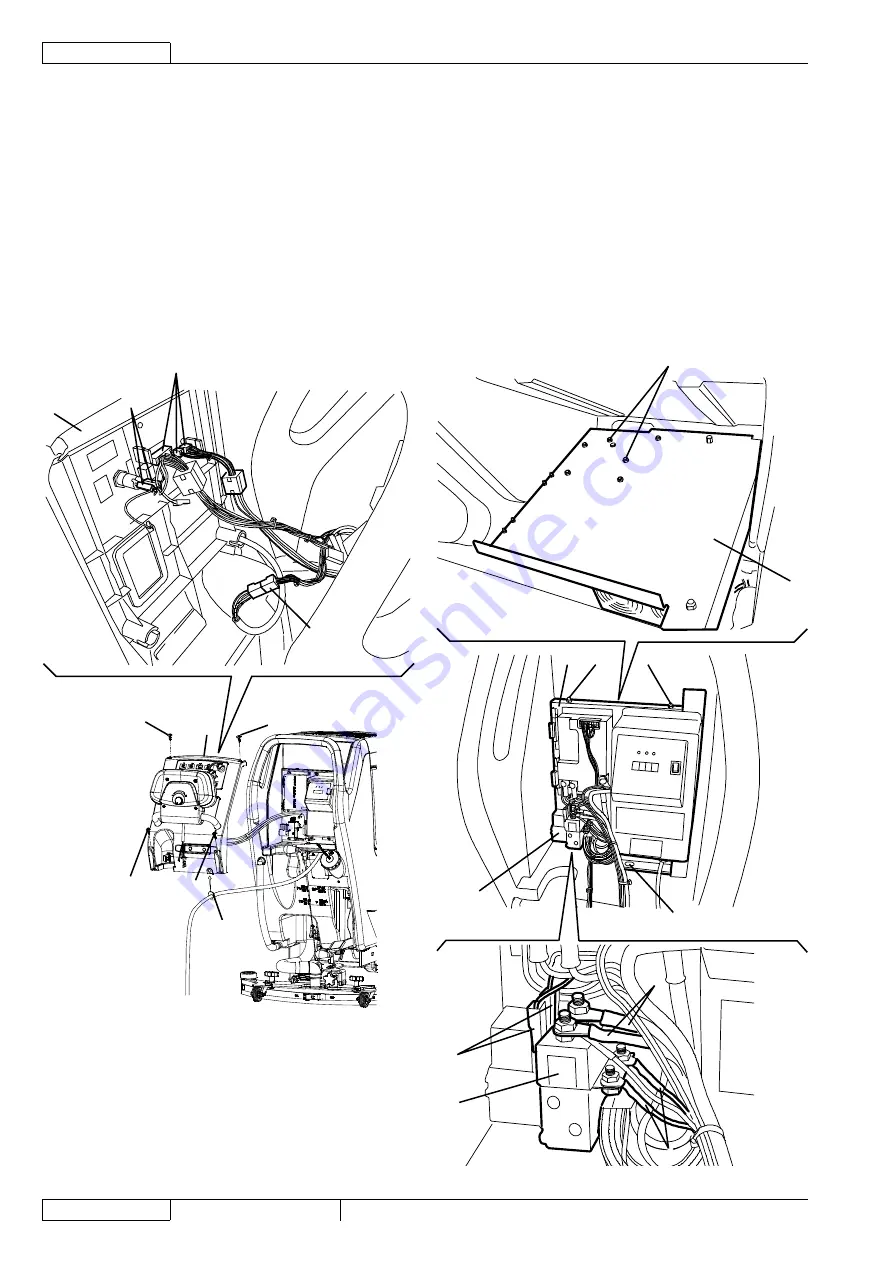
ENGLISH
SERVICE MANUAL
58
9096982000(1)2007-02
Adfinity
TM
17 ST, 20 ST, 20 D, X 20 D, X 20 C, X 24 D
ELECTRICAL SYSTEM
BRUSH MOTOR ELECTROMAGNETIC SWITCH DISASSEMBLY/ASSEMBLY
Disassembly
Disconnect the battery connector (12).
Move aside the recovery water drain hose (16).
Remove the battery charger cable (6) from the cable holder (7).
Remove the screws (A) and carefully move aside the panel (B) by disengaging the cable grommet (C) from its housing on
the panel (B).
Disconnect the connectors (D), (E), (F), and remove the panel (B).
Disconnect the terminals (G) and (H) from the electromagnetic switch (J). Disconnect also the terminals (I), which are
present only on the models with drive system.
Remove the screws (K) and move the electrical panel (L) by disengaging it from the lower fastener (M).
Remove the screws (N) on the rear side of the electrical panel (L), then remove the electromagnetic switch (J).
Assembly
Assemble the components in the reverse order of disassembly.
1.
2.
3.
4.
5.
6.
7.
8.
9.
A
A
B
A
A
C
B
D
E
F
L
N
J
L K
K
M
H
G
J
I
S301571A
S301572A