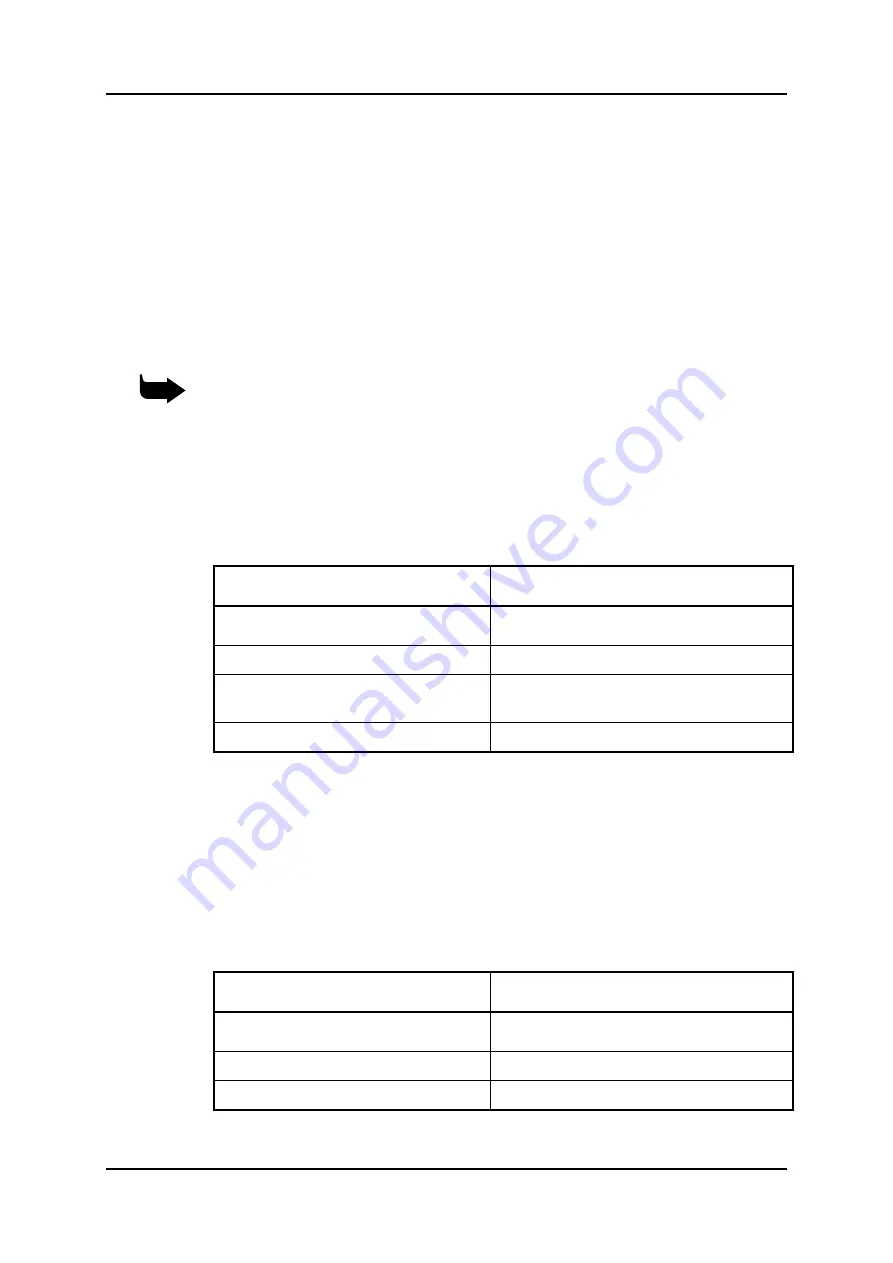
ADT Model 7900 Uno Dicing Series Installation Supplement
Preparing the Site
P/N 97910-9000-001-01 Ver. 04/2014
5
3.
PREPARING THE SITE
Before installing the system, verify that all of the following elements are
present at the site and their specifications have been met:
"Environmental Requirements" on page 5.
"Electricity Supply" on page 5.
"Drain and Exhaust" on page 7.
"Pneumatics" on page 8.
"Site Dimensions" on page 8.
Note:
If you require fastening the system to the floor, contact ADT for the
securing kit.
3.1
Environmental Requirements
To ensure proper system performance, verify that the following room
specifications are met.
Table 8. Environmental Requirements
Element
Specifications
Temperature
20 °C - 25 °C (68 °F ± 77 °F)
Temperature variation
±1 °C (±1.8 °F)
Humidity
Less than 70% relative humidity (non-
condensing)
Lighting
Minimum 1000 lux.
3.2
Electricity Supply
The system’s internal main power connection has been preset by ADT to
comply with the voltage requirements at your site, according to
information that you provided at the time of ordering.
3.2.1
Electric Supply Specification
Table 9. Electric Supply Specifications
Element
Specifications
Voltage Options (RMS)
200 to 240 ±10% VAC, 1 phase
Frequency
50/60 Hz ±2%
Power Consumption
2.5 KVA (2" Spindle)