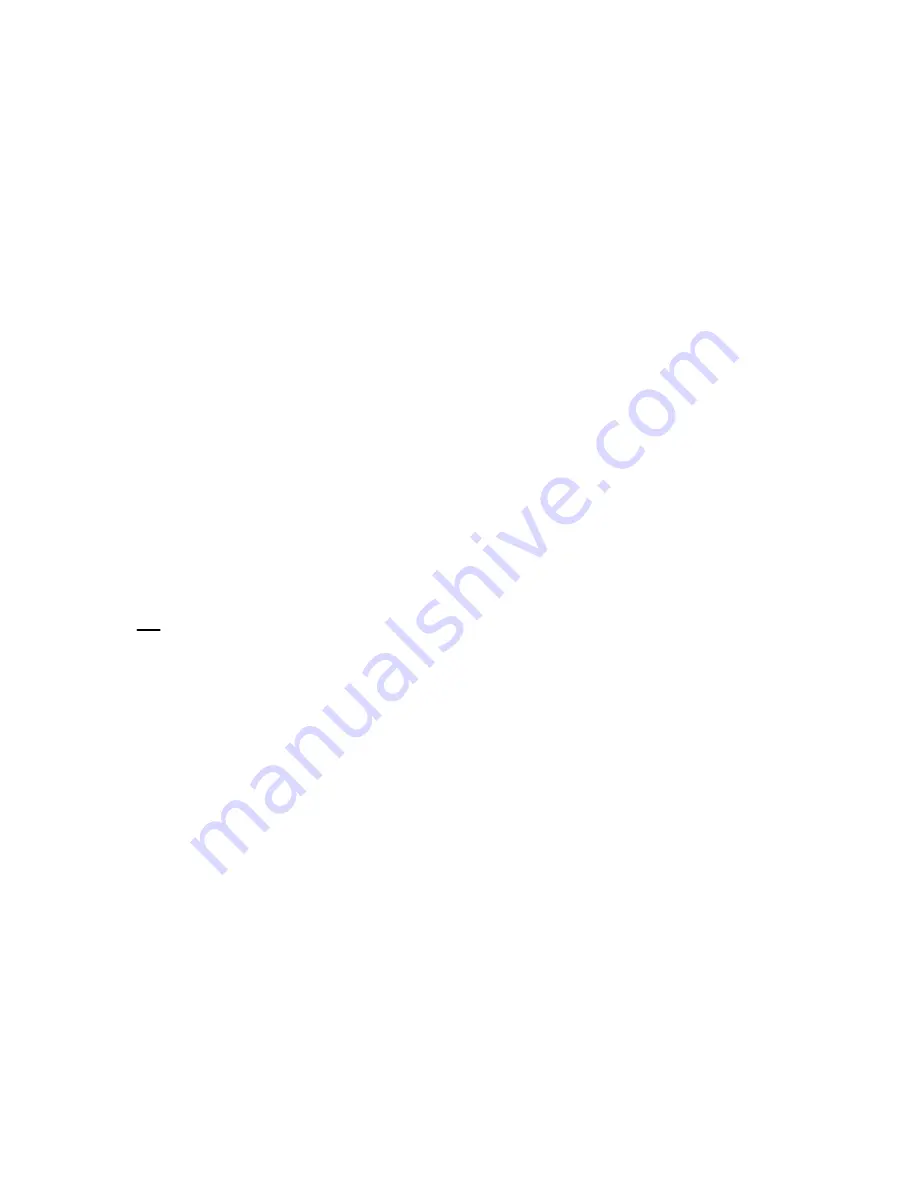
③
.Selection of welding parameters
Except for pulse current and the width time (Pulse time On) as well as pulse frequency ,welding
parameters of pulse argon gas tungsten arc welding are as same as general tungsten DC argon are
welding. Pulse current increasing means electric arc can obtain greater penetration ability.But too
much current can cause local melting of tungsten electrode.Generally,welding current required
for DC tungsten argon are welding or greater current is used. Arc holding current and base current
influences cooling and crystallizing of the metal in the bath. The range is determined by
performance of the welding materials. When sheet is welding,smaller arc holding current (base
current) is usually used in order to reduce welding through and deformation.When pulse width ratio
(holding time of pulse current and base current) is selected, both the heat input and features of pulse
%
%
welding should be considered. Usually, it can be selected between 10
- 90
. Selection of pulse
frequency (periodical change time of pulse current) mainly depends on thickness of sheet and
welding speed and operation custom of the operator should be also considered.
If you use longer cable tig torch,please set the "Pre Flow" time between 0-10s.
1.5 AC ARGON ARC WELDING
1. put switch "19" (AC/DC) onto the position "AC".
2. The method of the connection same as 1.1
3. Reguting "13" to select right "sp(AC balance)"
SP= *100%
tp:the time of I
2
at positive tn: the time of In at Negative
4. Regulating "15" to select right AC square wave frequency.
5. The Method of the welding same
as 1.1
2.Hand welding with electrode
①
.Put switch"12" (STICK/TIG switch) onto the position "STICK".
②
.Regulating Current Knob"4" to select right welding current
select empiric formula:I=40d, d is dia. of the electrode.
③
.Notice positive and negative connection during welding.
tp
tn