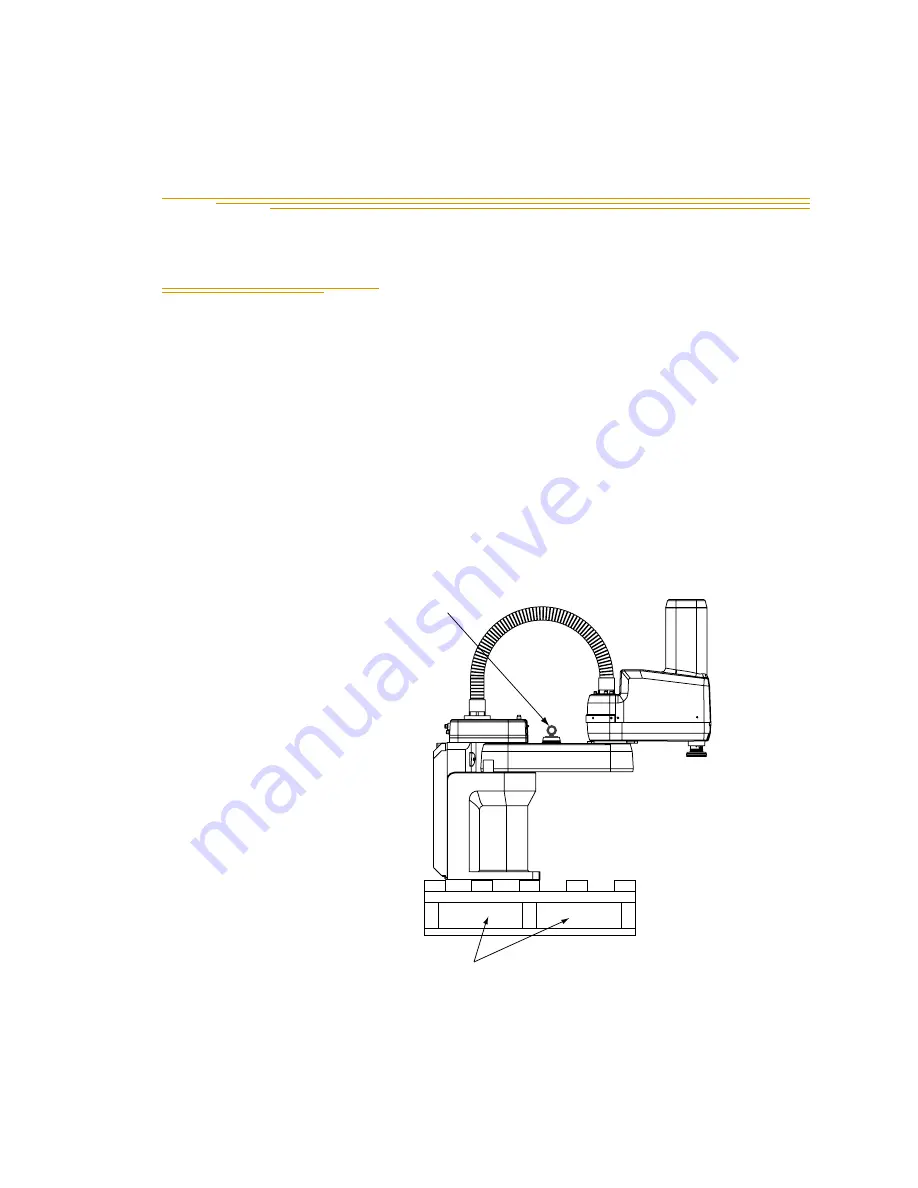
Adept Cobra i600/i800 Robot User’s Guide, Rev E
35
Robot Installation
3
3.1
Transport and Storage
This equipment must be shipped and stored in a temperature-controlled environment,
within the range –25° to +55° C (-13° to +131° F). The recommended humidity range is 5 to
90 percent, non-condensing. It should be shipped and stored in the Adept-supplied
packaging, which is designed to prevent damage from normal shock and vibration. You
should protect the package from excessive shock and vibration.
Use a forklift, pallet jack, or similar device to transport and store the packaged equipment
(see
).
The robots must always be stored and shipped in an upright position in a clean, dry area
that is free from condensation. Do not lay the crate on its side or any other non-upright
position: this could damage the robot.
The i600 robot weighs 41 kg (90 lb) and the i800 weighs 43 kg (95 lb) with no options
installed.
Figure 3-1. Cobra Robot on a Transportation Pallet
Eyebolt for lifting robot
after robot has been
unbolted from the
transportation pallet.
Place forklift or pallet-jack here.
Summary of Contents for Adept Cobra i600
Page 1: ...Adept Cobra i600 i800 Robot User s Guide ...
Page 2: ......
Page 10: ......
Page 14: ......
Page 34: ......
Page 56: ...Chapter 4 System Installation 56 Adept Cobra i600 i800 Robot User s Guide Rev E ...
Page 76: ...Chapter 5 Optional Equipment Installation 76 Adept Cobra i600 i800 Robot User s Guide Rev E ...
Page 104: ...Chapter 6 System Operation 104 Adept Cobra i600 i800 Robot User s Guide Rev E ...
Page 116: ...Chapter 7 Maintenance 116 Adept Cobra i600 i800 Robot User s Guide Rev E ...
Page 147: ...Index Adept Cobra i600 i800 Robot User s Guide Rev E 147 ...
Page 148: ......
Page 149: ......
Page 150: ...5960 Inglewood Drive Pleasanton CA 94588 925 245 3400 P N 03589 000 Rev E ...