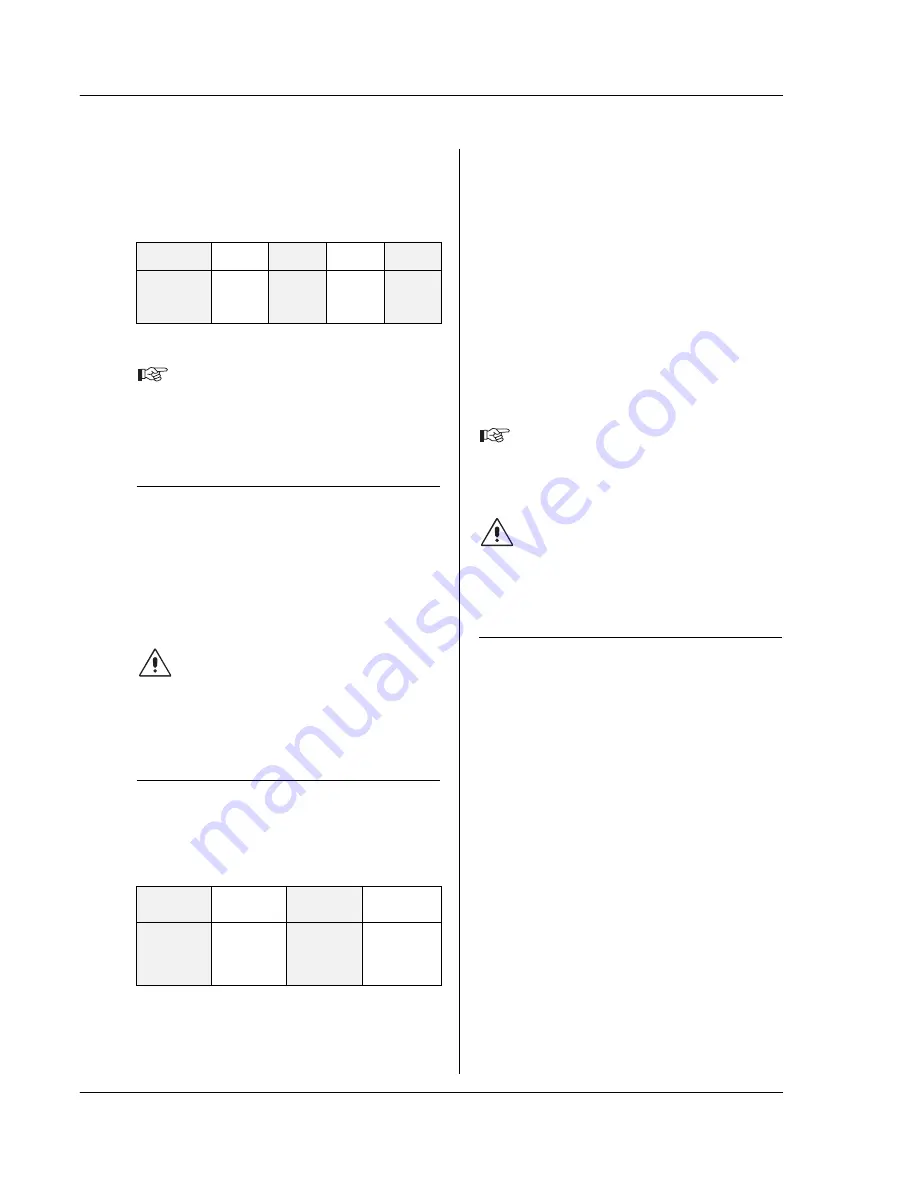
3
Calculation of maximum flue length;
Maximum allowable total air and flue pipe resistance is 1,4 mbar. It
is not allowed to connect air- exhaust ducts with higher
resistance. The maximum length in meters for parallel and concentric
systems is given in the table below.
Note:
• A 90 ° bend is considered to have the same resistance
as 1 m straight tube.
• The air-supply and exhaust system has to fulfill the
local and national regulations.
FROST PROTECTION
The boiler is protected against frost. During long absence in the
winter the installation must be protected from freezing by partially
opening all convector valves. In this case the room thermostat is not
to be setted at a temperature under 15 °C.
When the flow sensor diminishes to 7 °C, the pump will be activated.
If the flow temperature decreases further, the boiler will light when
the flow sensor detects a temperature of 3 °C. The burner will remain
on until the flow temperature has risen to 10 °C. After this the pump
will run for another 15 minutes.
WARNING:
This is only an automatic protection of the boiler.
This does not prevent the installation from freezing.
Convectors, which are likely to freeze, can be equipped
with a frost thermostat, which is to be connected
parallel to the room thermostat.
SETTING GAS-AIR RATIO CONTROL
The boiler is equipped with a gas-air-ratio control. This means that
the amount of gas is automatically controlled depending on the
amount of air. The advantage is that the %CO
2
is more or less
constant over the whole modulation level of the boiler.
The %CO
2
is, depending of the type of gas, setted according the
table below:
The manufacturer has setted the boiler for - E-group / G20.
This is indicated by means of a sticker, which is mounted below the
type-plate.
Checking of the %CO
2
has to be done both on max load
and min load:
•
Open the appliance by removing the front cover
•
Light the boiler in max load by means of the servicemode
H (mode and + button)
•
Wait for equilibrium
•
Now the CO
2
has to be 8,9 ± 0,2 %
•
In case the %CO
2
is not correct, you can adjust it by turning the
brass screw near the venturi (clockwise = lower CO
2
, counter
clockwise = higher CO
2
)
•
Set the boiler to the min load by means of the servicemode
L (mode and - button)
•
Wait for equilibrium
•
Now the CO
2
has to be 8,7 ± 0,2 %
•
In case the %CO
2
is not correct, you can adjust it by turning the
white plastic screw on the gas valve (clockwise = higher CO
2
,
counter clockwise = lower CO
2
)
In case the installation is supplied with a different type of
gas, the boiler has to be re-adjusted by the installer
according the procedure mentioned above.
NOTE:
• For setting to LL-group, the brass screw near the
venturi has to be turned a few times counter clockwise.
• For setting to LPG, the brass screw near the venturi
has to be turned a few times clockwise.
IMPORTANT:
Subsequently the enclosed sticker “setted for LL
group” or “setted for LPG” has to be put over the
original sticker “setted for E-group»!!!
ELECTROTECHNICAL CONNECTION
1.
The electrical installation has to meet the actual regulations
2.
The wall socket has to be mounted in an easy accessible
position near the boiler.
3.
It is not allowed to modify the internal wiring of the boiler.
4.
The appliance is equipped with an earthed plug.
5.
The connection of the room thermostat is in the control box. This
contact is standard foreseen with a bridge. To replace this bridge
by the wires of the room thermostat, hinge the lower front cover
down. Unscrew the display cover and open the control box by
hinging the display cover down as well. The room thermostat
has to be connected at the pos 12 + 14 of the screw terminals.
The maximum cross section of the wires is 0,75 mm2.
The contact of the room thermostat has to be potentialfree.
6.
To connect timers which need 24 V supply from the boiler, there
is 2,4 VA available on the pos 11 and 13 of the screw terminals.
7.
To connect a sanitary thermostat, sanitary NTC, 3-wayvalve or
sanitary pump, there are screw terminals available.
Out-door temperature control
The out-door sensor has to be mounted to the northern wall of the
house at a height of approximately 2 m.
The boiler is standard set to operate with a room thermostat.
The MCBA will automatically detect when an out-door sensor is
connected. The control will automatically be adapted to operate with
room-ther out-door sensor.
Personal computer connection
For service and maintenance purposes it is possible to connect a
personal computer to the control of the boiler.
Please contact the manufacturer to receive more information about
this.
INSTALLATION
Ø 80 /
Ø 100 /
Ø 80 /
Ø 100 /
Ø 80
Ø100
Ø 125
Ø 150
Prestige 47
13
47
17
34
Prestige 64
9
33
12
24
Prestige 85
-
-
-
25
Type of gas
supply
% CO
2
% CO
2
pressure
(max. load)
(min. load)
E-group / G20
20 mbar
9,0 ± 0,2
8,7 ± 0,2
LL-group / G25
20 mbar
9,0 ± 0,2
8,7 ± 0,2
LPG / G30
50 mbar
11,6 ± 0,2
11,3 ± 0,2
LPG / G31
50 mbar
10,6 ± 0,2
10,3 ± 0,2