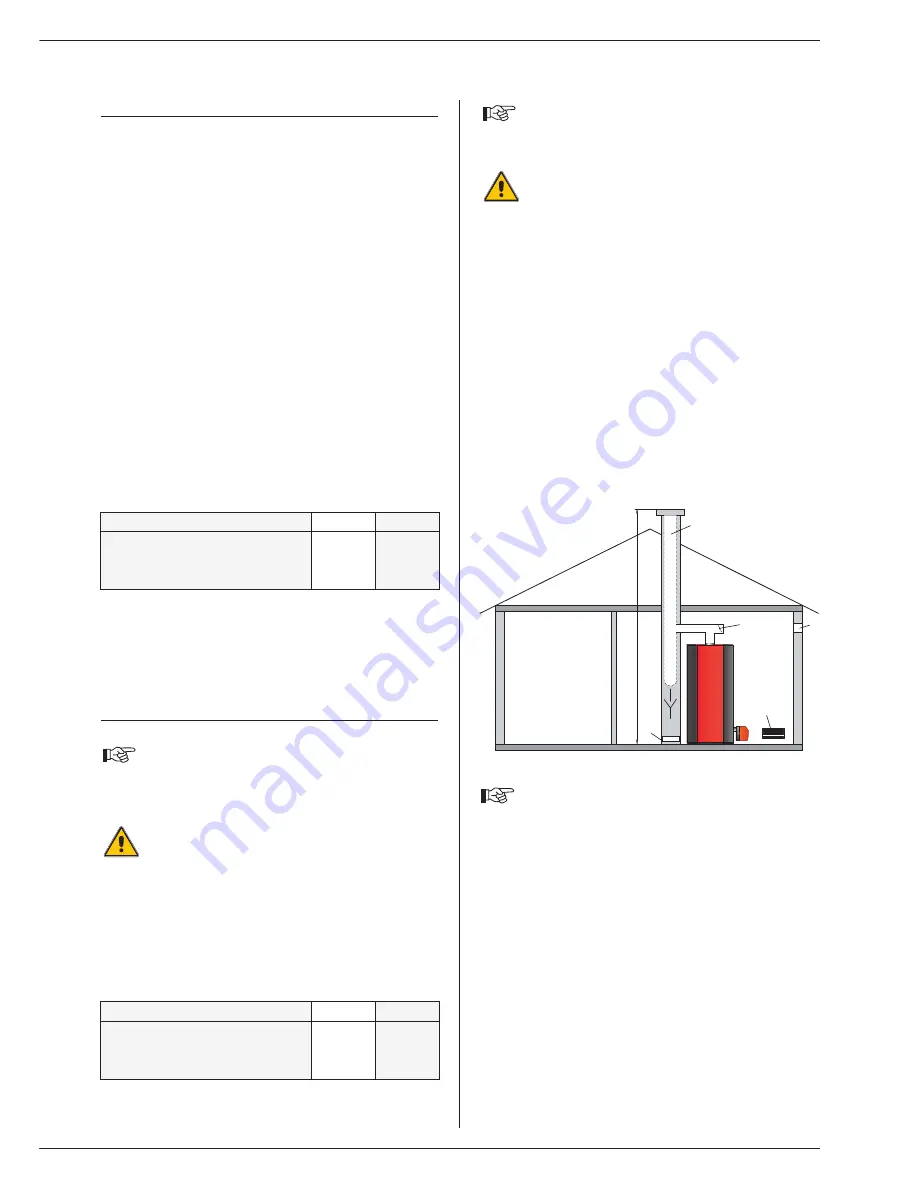
7
INSTALLATION
BOILER ROOM
Important
• Keep vents free at all times.
• Do not store inflammable products in the boiler room.
• Do not store corrosive products near the boiler, such as paints,
solvents, chlorine, salt, soap and other cleaning products.
• If you smell gas, do not switch on the light or light a flame. Turn off
the mains gas tap at the meter and inform the appropriate
services immediately.
Access
The boiler room must be large enough to allow good access to the
boiler. The following minimum distances are required around the
boiler:
- front
500 mm
- side
100 mm
- behind
150 mm
- above
350 mm
Ventilation
The boiler room must have both low- and high-level ventilation,
in accordance with the local standards and provisions force.
The table below gives an example conforming to the Belgian standards.
Other countries should refer to their own standards.
Base
The base on which the boiler rests must be made of non-combustible
materials.
CHIMNEY CONNECTIONS
IMPORTANT
Boilers must be installed by an approved heating
engineer, in accordance with the prevailing local
standards and regulations.
The duct size may not be smaller than the boiler outlet
duct.
Typical boiler connection: B23
The boiler is connected to the chimney by a metal pipe rising at an
angle from the boiler to the chimney.
A flue disconnection piece is required.
This must be easy to remove to give access to the flue pipes when
servicing the boiler.
Ventilation
200 N
200 F
Min. fresh air requirement
m
3
/h
277
353
Bottom
dm
2
2.45
2.45
Top
dm
2
4.62
5.88
Chimney / minimum flue diameter
200 N
200 F
E = 5 m
Ø F min.
mm
284
320
E = 10 m Ø F min.
mm
250
269
E = 15 m Ø F min.
mm
250
250
Note:
Regulations vary from country to country therefore
the table above is intended only as a guide.
Due to the high efficiency of our boilers, the flue gasses
exit at low temperature. Accordingly, there is risk that
the flue gasses could condense, which could damage
the chimney. In order to avoid this risk, it is strongly
recommended that the chimney be lined.
A condensation drain outlet must be fitted close to the
boiler to prevent condensation products from the
chimney running into the boiler.
To avoid condensation water running out of the
terminal, all horizontal flue runs must fall back towards
the boiler.
B23
D
A
B
C
F
E
A. Top vent
B. Bottom vent
C. Draught regulator
D. Inspection window
E. Height of lined chimney
F. Chimney diameter
When connecting the flue-gas outlet to an existing
chimney, do not take into account the pressure drop
on the “flue gas side”.