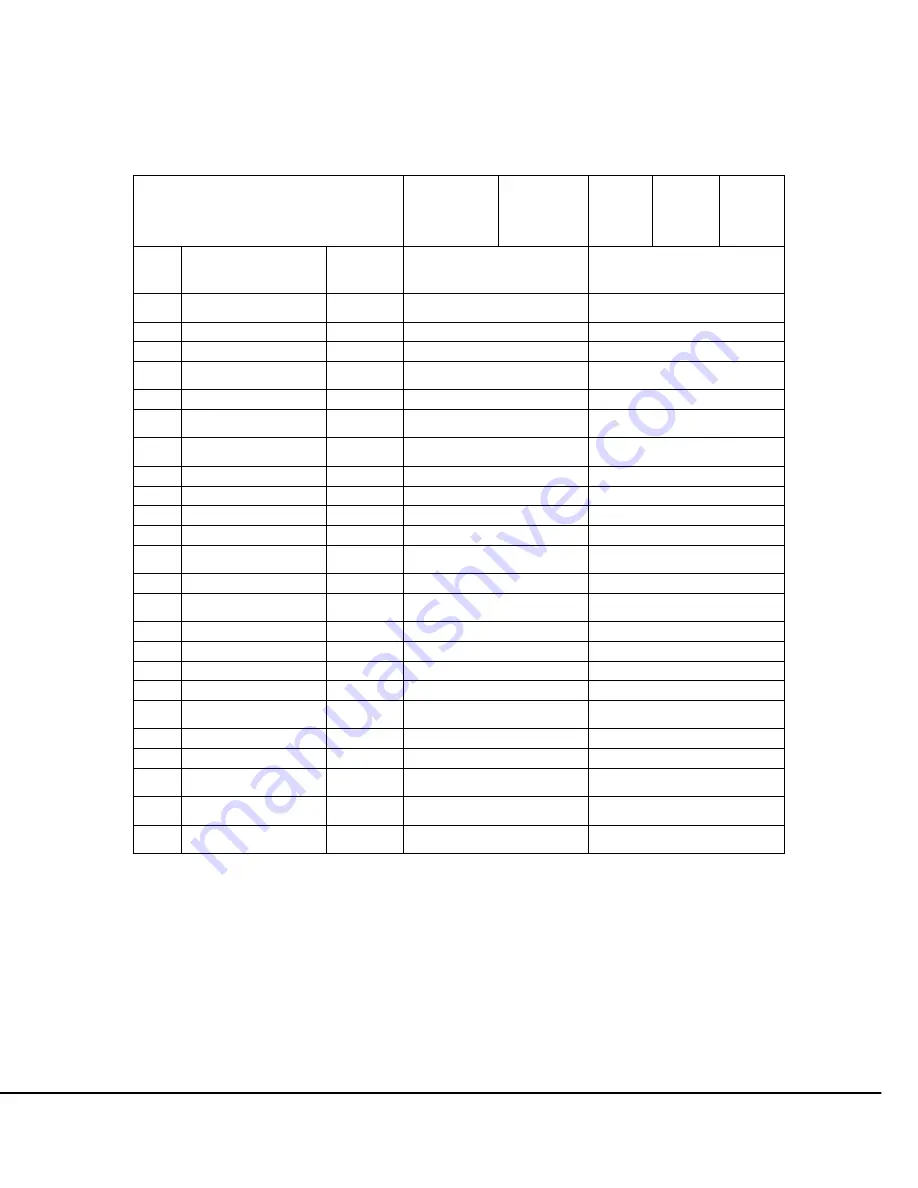
Electric Chain Hoists (Single Brake)
Model NECH
PAGE: 76
NECH-0214
ACI Hoist & Crane | 2721 NE 4th Ave Pompano Beach, FL 33064| 954.367.6116
Visit WWW.ACIHOIST.COM for the most current information
11.9
Parts List: Gear Box Assembly
Table 11.9.1
Gear Box Assembly Parts List: 6.3-7.1 mm
Hoist Model
NECH-
00526
NECH-
02013
NECH-
01016
NECH-
01026
NECH-
04008
NECH-
04013
NECH-
02016
NECH-
02013
NECH-
04008
NECH-
06009
Item
Spare Parts Name
Quantity
0.5 TO 1 TON
6.3mm chain
1 TO 3 TON
7.1mm chain
1
Deep groove ball
bearing
1
KD4-001
KD4-101
2
circlip for shaft
1
KD4-002
KD4-102
3
Output gear
1
KD4-003
KD4-103
4
Deep groove ball
bearing
1
KD4-004
KD4-104
5
Gear-gear shaft
1
KD4-005
KD4-105
6
Deep groove ball
bearing
1
KD4-006
KD4-106
7
Deep groove ball
bearing
1
KD4-007
KD4-107
8
Oil seal
1
KD4-008
KD4-108
9
Chain wheel
1
KD4-009
KD4-109
10
Oil seal
1
KD4-010
KD4-110
11
Output shaft assembly
1
KD4-011
KD4-111
12
Deep groove ball
bearing
1
KD4-012
KD4-112
13
Bearings fixed ring
1
KD4-013
KD4-113
14
Deep groove ball
bearing
1
KD4-A014
KD4-A114
15
Circlip for hole
1
KD4-015
KD4-115
16
Spring straight pins
2
KD4-016
KD4-116
17
Spring washer
3
KD4-017
KD4-117
18
socket head cap screws
3
KD4-018
KD4-118
19
Reduction gear fixed
axis
1
KD4-019
KD4-119
20
Bearing
2
KD4-020
KD4-120
21
Dual gears
1
KD4-021
KD4-121
22
Reduction gear fixed
frame
1
KD4-022
KD4-122
23
Reduction gear fixed
stator
1
KD4-023
KD4-123
24
Cross Recessed
Countersunk Screw
1
KD4-024
KD4-124