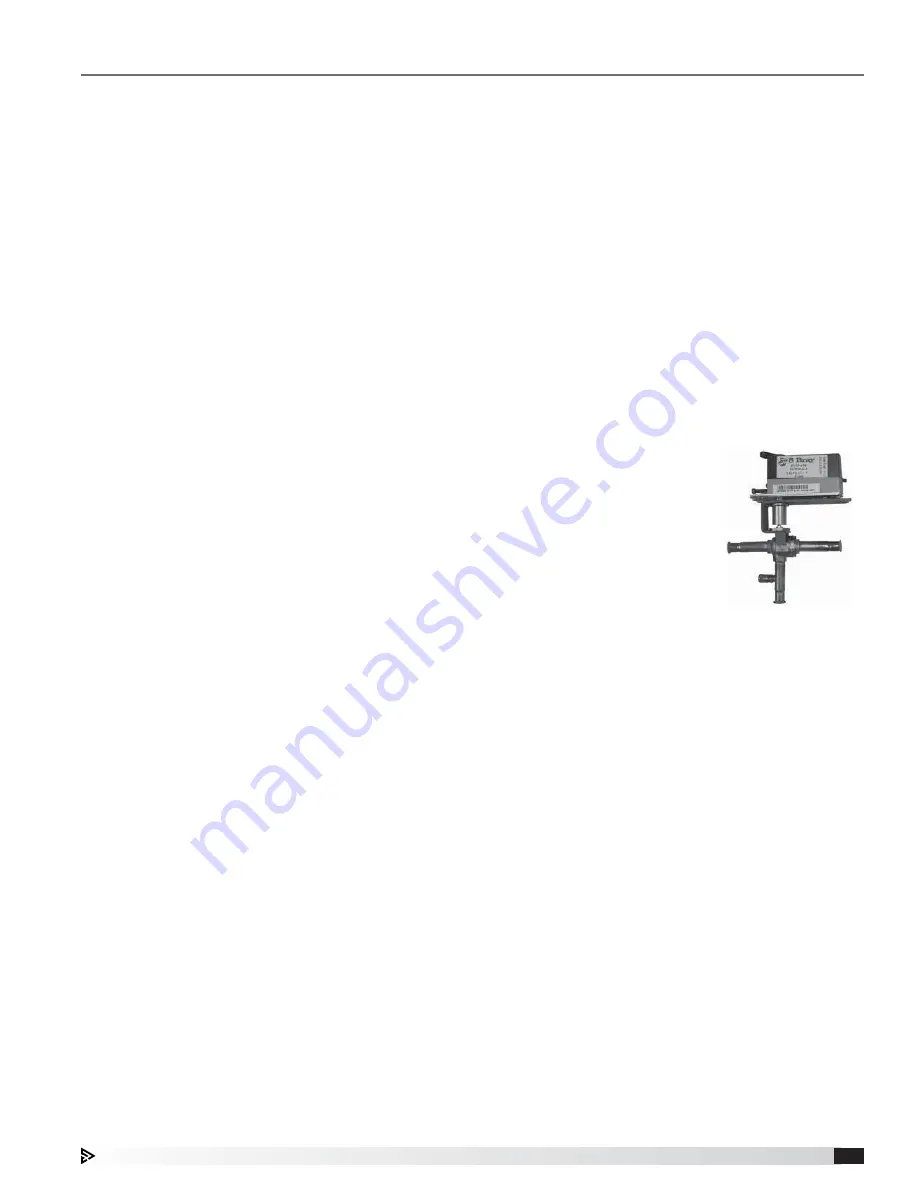
Packaged Rooftop Ventilator
15
Optional Component Operation
Dirty Filter Sensor
Dirty filter sensors monitor pressure drop across the
outdoor air filters, exhaust air filters, or both. If the
pressure drop across the filters exceeds the set point,
the sensor will close a set of contacts in the unit control
center. Field-wiring of a light (or other alarm) to these
contacts will notify maintenance personnel when
filters need to be replaced. The switch has not been
set at the factory due to external system losses that
will affect the switch. This switch will need minor field
adjustments after the unit has been installed with all
ductwork complete. The dirty filter switch is mounted in
the exhaust inlet compartment next to the unit control
center or in unit control center.
Microprocessor Control
The microprocessor controller is specifically designed
and programmed to optimize the performance of
the unit with supplemental heating and cooling. This
option ensures that the outdoor air is conditioned to
the desired discharge conditions. The controller and
accompanying sensors are factory-mounted, wired and
programmed. Default settings are pre-programmed, but
are easily field-adjustable.
The microprocessor controller can be interfaced with
a Building Management System through LonWorks®,
BACnet®, or ModBus.
Please refer to the Installation, Operation and
Maintenance manual for detailed information.
Unoccupied Recirculation Damper
The unoccupied recirculation option provides a
recirculation damper from the return air intake to the
supply airstream. If equipped with a room temperature
and/or relative humidity sensor, the unit can cycle on to
maintain unoccupied room set points if there is a call
for unoccupied heating, cooling, or dehumidification.
During the unoccupied mode, the supply and exhaust
(if equipped) fans will be off unless there is a call for
cooling, heating, or dehumidification in the space.
Vapor Tight Lights
Vapor tight lights provide light to each of the
compartments in the energy recovery unit. The lights
are wired to a junction box mounted on the outside of
the unit. The switch to turn the lights on is located in
the unit control center. The switch requires a separate
power source to allow for power to the lights when the
unit main disconnect is off for servicing.
Hot Gas Bypass Valve
(standard scroll)
On units equipped with hot gas bypass, hot gas
from the compressor is injected into the liquid line of
the evaporator coil after the thermostatic expansion
valve. This process starts to occur when suction gas
temperatures drop below 28°F, which is 32°-34°F coil
surface temperature. Hot gas helps the evaporator coil
from freezing up and the compressor from cycling. The
valve needs to be adjusted to exact specifications once
unit is installed in the field.
Hot Gas Reheat Valve
Units equipped with a reheat coil use a three-way
valve with actuator to control the supply air discharge
temperature of the unit during dehumidification mode.
The unit controller provides a 0-10 VDC signal to control
the amount of reheat to meet the supply temperature
set point.
Controls by Others
The reheat coil needs to be purged to ensure adequate
oil return. It is recommended
that every six hours of reheat
compressor run time should
initiate a six minute purge
cycle. During the purge cycle,
the reheat valve should be
modulated to 100% open to
the reheat coil.