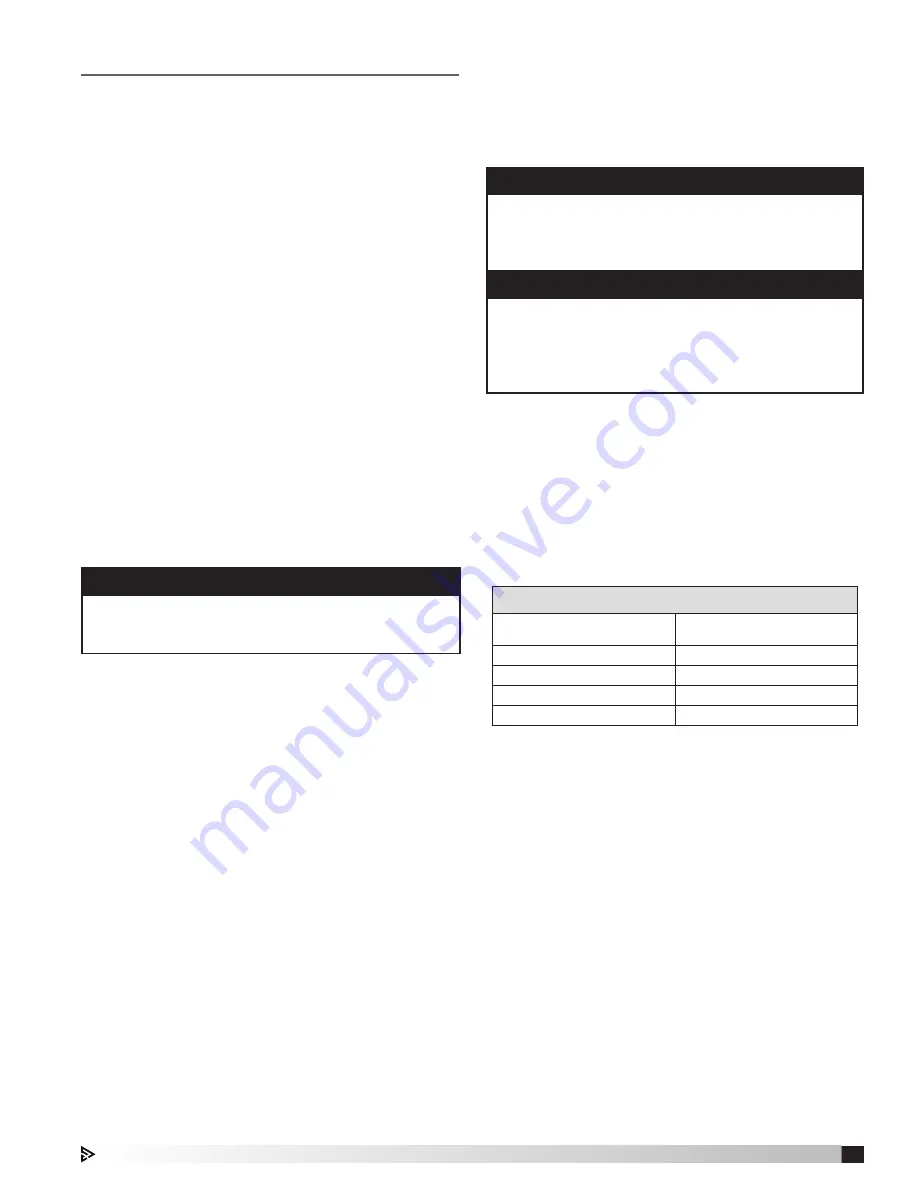
Electrical Information
The unit must be electrically grounded in accordance
with the current National Electrical Code, ANSI/NFPA
70. In Canada, use the current CSA Standard C22.1,
Canadian Electrical Code, Part 1. In addition, the
installer should be aware of any local ordinances or
electrical company requirements that might apply.
System power wiring must be properly fused and
conform to the local and national electrical codes.
System power wiring is to the unit main disconnect
(door interlocking disconnect switch standard on most
units) or distribution block and must be compatible
with the ratings on the nameplate: supply power
voltage, phase and amperage (Minimum Circuit
Amps - MCA; Maximum Overcurrent Protection -
MOP). All wiring beyond this point has been done by
the manufacturer and cannot be modified without
affecting the unit’s agency / safety certification. If
field installing an additional disconnect switch, it
is recommended that there is at least four feet of
service room between the switch and system access
panels. When providing or replacing fuses in a fusible
disconnect, use dual element time delay fuses and
size according to the rating plate.
Field Power Connection
All power and control connections should be run
through the floor or side panel of the unit.
If power supply is desired through bottom of unit, run
the wiring through the curb, cut a hole in the cabinet
bottom and run wires to the disconnect switch. Seal
the penetration in cabinet bottom to prevent leakage.
The electric supply to the unit must meet stringent
requirements for the system to operate properly.
Voltage supply and voltage imbalance between
phases should be within the following tolerances.
If the power is not within these voltage tolerances,
contact the power company prior to operating the
system.
Voltage Supply
See Voltage Use Range on the rating plate. Measure
and record each supply leg voltage at all line
disconnect switches. Readings must fall within the
allowable range on the rating plate.
Voltage Imbalance
In a 3-phase system, excessive voltage imbalance
between phases will cause motors to overheat and
eventually fail. Maximum allowable imbalance is 2%.
To determine voltage imbalance, use recorded voltage
measurements in this formula.
Low Voltage Controller Circuitry
Manufacturer recommends that all low voltage
wiring be run in conduit wherever it may be
exposed to the weather.
Most factory-supplied electrical components are
pre-wired. To determine what electrical accessories
require additional field wiring, refer to the unit-specific
wiring diagram located on the inside of the control
center access door.
The low voltage control circuit is 24 VAC and control
wiring should not exceed 0.75 ohms.
Refer to Field Control Wiring Length/Gauge table for
wire length maximums for a given wire gauge.
Control wires should not be run inside the same
conduit as that carrying the supply power. Make sure
that field-supplied conduit does not interfere with
access panel operation. All low voltage wiring should
be run in conduit wherever it may be exposed to the
weather.
If wire resistance exceeds 0.75 ohms, an industrial-
style, plug-in relay should be added to the unit
control center and wired in place of the remote
switch (typically between terminal blocks R and G
on the terminal strip (refer to Typical Control Center
Components). The relay must be rated for at least 5
amps and have a 24 VAC coil. Failure to comply with
these guidelines may cause motor starters to “chatter”
or not pull in which can cause contactor failures and/
or motor failures.
WARNING
The roof lining contains high voltage wiring. To
prevent electrocution, do not puncture the interior or
exterior panels of the roof.
Key:
V1, V2, V3 = line voltages as measured
VA (average) = (V1 + V2 + V3) / 3
VD = Line voltage (V1, V2 or V3) that
deviates farthest from average (VA)
Formula:
% Voltage Imbalance = [100 x (VA-VD)] / VA
CAUTION
If any of the original wire as supplied with the unit
must be replaced, it must be replaced with wiring
material having a temperature rating of at least
105ºC.
WARNING
To prevent injury or death due to electrocution or
contact with moving parts, lock disconnect switch
open.
For units with a gas furnace, if you turn off the
power supply, turn off the gas.
Field Control Wiring Length/Gauge
Total
Wire Length
Minimum
Wire Gauge
125 ft.
18
200 ft.
16
300 ft.
14
450 ft.
12
9
Model MPX Make-Up Air Unit
Model XMPX Make-Up Air Unit