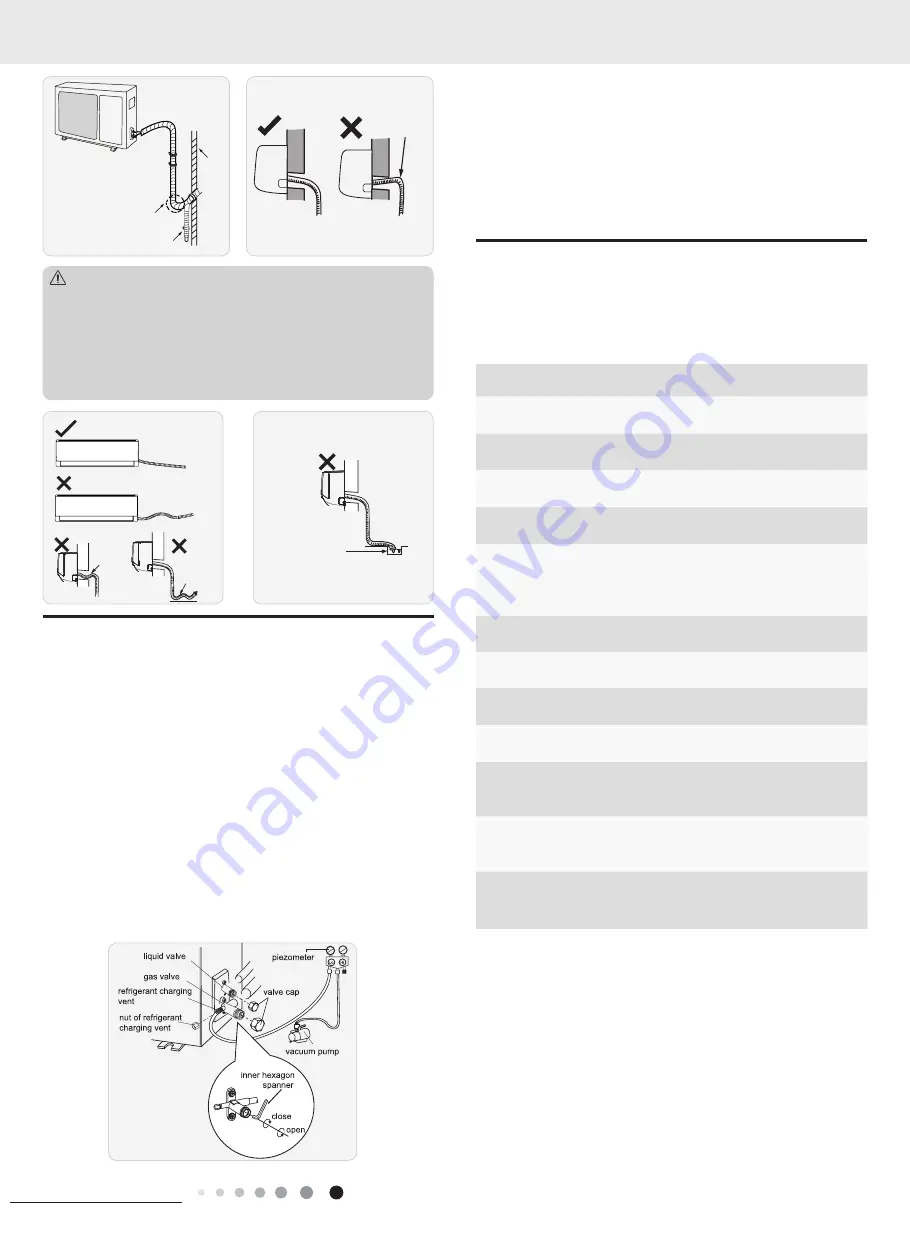
12
Installation and Maintenance
Service Manual
The drain hose
can't raise
upwards.
Fig.24
Fig.25
Wall
U-shaped curve
Drain hose
(1) The through-wall height of drain hose shouldnt be higher
than the outlet pipe hole of indoor unit.(As show in Fig.25)
(2) Slant the drain hose slightly downwards. The drain hose
can't be curved, raised and fluctuant, etc.(As show in Fig.26)
(3) The water outlet can't be placed in water in order to drain
smoothly.(As show in Fig.27)
Note:
、
、
、
、
The drain hose can't be fluctuant
The drain
hose can't
be fluctuant
The water
outlet can't
be fluctuant
The water outlet
can't be placed
in water
Fig.26
Fig.27
Use vacuum pump
1.Remove the valve caps on the liquid valve and gas valve and
the nut of refrigerant charging vent.
2. Connect the charging hose of piezometer to the refrigerant
charging vent of gas valve and then connect the other charging
hose to the vacuum pump.
3 . Open the piezometer completely and operate for 10-15min to
check if the pressure of piezometer remains in -0.1MPa.
4. Close the vacuum pump and maintain this status for 1-2min
to check if the pressure of piezometer remains in -0.1MPa. If the
pressure decreases, there may be leakage.
5. Remove the piezometer, open the valve core of liquid valve
and gas valve completely with inner hexagon spanner.
6. Tighten the screw caps of valves and refrigerant charging vent.
7. Reinstall the handle.
8.8 Leakage Detection
(1) With leakage detector:
Check if there is leakage with leakage detector.
(2) With soap water:
If leakage detector is not available, please use soap water for
leakage detection. Apply soap water at the suspected position
and keep the soap water for more than 3min. If there are air
bubbles coming out of this position, There's a leakage.
8.9 Check after Installation and Test
operation
1. Check after Installation
Check according to the following requirement after finishing
installation.
NO.
Items to be checked
Possible malfunction
1
Has the unit been installed
firmly?
The unit may drop, shake or
emit noise.
2
Have you done the
refrigerant leakage test?
It may cause insufficient
cooling (heating) capacity.
3
Is heat insulation of pipeline
sufficient?
It may cause condensation
and water dripping.
4
Is water drained well?
It may cause condensation
and water dripping.
5
Is the voltage of power
supply according to the
voltage marked on the
nameplate?
It may cause malfunction or
damage the parts.
6
Is electric wiring and pipeline
installed correctly?
It may cause malfunction or
damage the parts.
7
Is the unit grounded
securely?
It may cause electric
leakage.
8
Does the power cord follow
the specification?
It may cause malfunction or
damage the parts.
9
Is there any obstruction in
air inlet and air outlet?
It may cause insufficient
cooling (heating) capacity.
10
The dust and sundries
caused during installation
are removed?
It may cause malfunction or
damaging the parts.
11
The gas valve and liquid
valve of connection pipe are
open completely?
It may cause insufficient
cooling (heating) capacity.
12
Is the inlet and outlet of
piping hole been covered?
It may cause insufficient
cooling(heating) capacity or
waster eletricity.
2. Test Operation
(1) Preparation of test operation
● The client approves the air conditioner installation.
● Specify the important notes for air conditioner to the client.
(2) Method of test operation
● Put through the power, press ON/OFF button on the remote
controller to start operation.
● Press MODE button to select AUTO, COOL, DRY, FAN and
HEAT to check whether the operation is normal or not.
● If the ambient temperature is lower than 16
℃
, the air
conditioner can't start cooling.
8. Installation
8.7 Test and operation