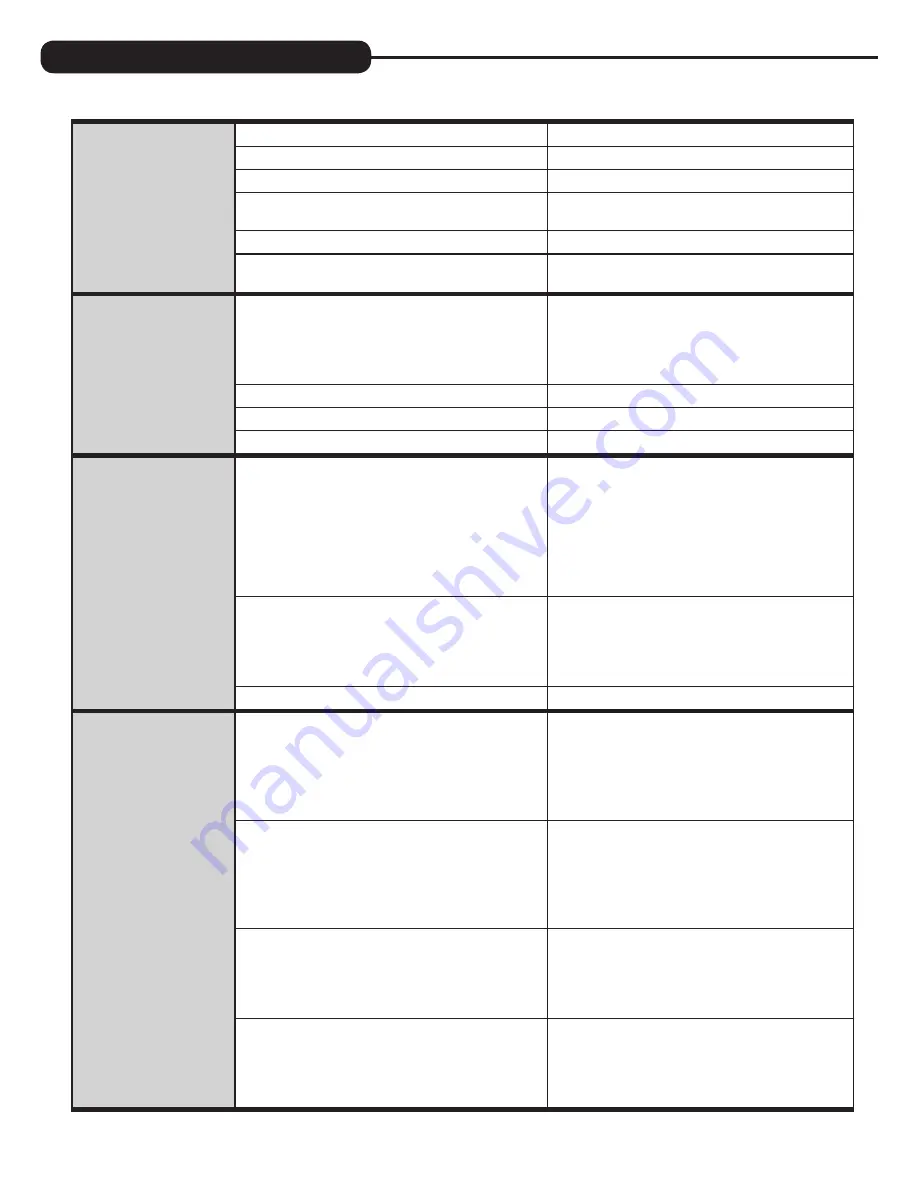
14
12. Control valve fails to
draw in regenerant
A . Injector is plugged
A . Remove injector and clean or replace
B . Faulty regenerant piston
B . Replace regenerant piston
C . Regenerant line connection leak
C . Inspect regenerant line for air leak
D . Drain line restriction or debris cause excess
back pressure
D . Inspect drain line and clean to
correct restriction
E . Drain line too long or too high
E . Shorten length and or height
F . Low water pressure
F . Check incoming water pressure – water
pressure must remain at minimum of 25 psi
13. Water running to
drain
A . Power outage during regeneration
A . Upon power being restored control will finish
the remaining regeneration time . Reset time of
day . If PC board has battery back up present
the battery may be depleted . See front cover
and drive assembly drawing for instructions .
B . Damaged seal/stack assembly
B . Replace seal/stack assembly
C . Piston assembly failure
C . Replace piston assembly
D . Drive cap assembly not tightened in properly
D . Retighten the drive cap assembly
14. E1, Err – 1001,
Err – 101 =
Control unable
to sense motor
movement
A . Motor not inserted full to engage pinion,
motor wires broken or disconnected
A . Disconnect power, make sure motor is fully
engaged, check for broken wires, make sure
two pin connector on motor is connected to the
two pin connection on the PC board labeled
MOTOR . Press NEXT and REGEN buttons for
3 seconds to resynchronize software with piston
position or disconnect power supply from PC
board for 5 seconds and then reconnect .
B . PC board not properly snapped into drive bracket
B . Properly snap PC board into drive bracket and
then Press NEXT and REGEN buttons for 3
seconds to resynchronize software with piston
position or disconnect power supply from PC
board for 5 seconds and then reconnect .
C . Missing reduction gears
C . Replace missing gears
15. E2, Err – 1002, Err –
102 = Control valve
motor ran too short
and was unable to
find the next cycle
position and stalled
A . Foreign material is lodged in control valve
A . Open up control valve and pull out piston
assembly and seal/stack assembly for
inspection . Press NEXT and REGEN buttons for
3 seconds to resynchronize software with piston
position or disconnect power supply from PC
board for 5 seconds and then reconnect .
B . Mechanical binding
B . Check piston and seal/stack assembly, check
reduction gears, check drive bracket and main
drive gear interface . Press NEXT and REGEN
buttons for 3 seconds to resynchronize software
with piston position or disconnect power supply
from PC board for 5 seconds and then reconnect .
C . Main drive gear too tight
C . Loosen main drive gear . Press NEXT and
REGEN buttons for 3 seconds to resynchronize
software with piston position or disconnect
power supply from PC board for 5 seconds
and then reconnect .
D . Improper voltage being delivered to PC board
D . Verify that proper voltage is being supplied .
Press NEXT and REGEN buttons for 3 seconds
to resynchronize software with piston position
or disconnect power supply from PC board for
5 seconds and then reconnect .
PROBLEM
CAUSE
CORRECTION
TROUBLESHOOTING GUIDE
Summary of Contents for iSoftenH2O
Page 26: ...26 NOTES ...
Page 27: ...27 ...