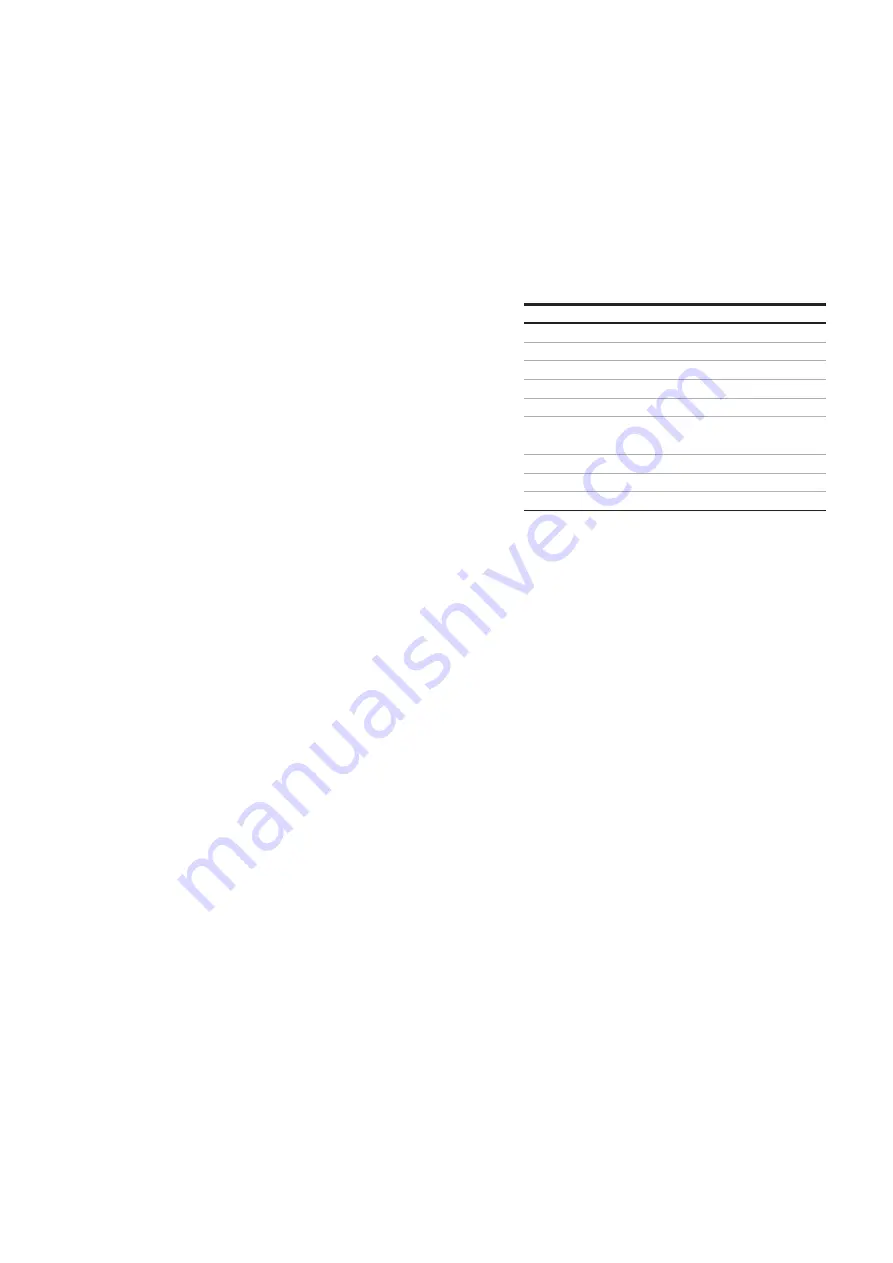
22
UniGear ZS1
I N S T A L L A T I O N , O P E R A T I O N A N D M A I N T E N A N C E
—
5 Assembly of the switchgear on site
In order to obtain an optimum installation sequence
and ensure high quality standards, on-site
installation of the switchgear should only be
carried out by specially trained and skilled
personnel, or at least by personnel supervised
and monitored by responsible persons.
5.1 General
On commencement of installation on site, the
switch room must be completely finished. This
means it must be provided with lighting and an
electricity supply. In addition, it must be lockable,
dry and with facilities for ventilation. All the
necessary preparations, such as wall openings,
ducts, etc., for routing the power and control
cables up to the switchgear must already be
complete. The ceiling height must be sufficient
for the opening travel of the pressure relief plates
(Higher than 3 m).
The ceiling must be high enough for the assembly
of a pressure relief duct (Higher than 3 m).
Compliance with the conditions for indoor
switchgear according to IEC 62271-1, including
the conditions for the indoor temperature class
must be ensured.
5.2 Foundations
It is recommended that the switchgear is installed
on the base irons of a “C” profile shape set into
the concrete floor of switch room.
Further structural data guidelines enable a rough
calculation of the space required to be made and
the planning of the room design for a switchgear
project.
When the final construction documents are
compiled for the execution of a building, the
binding data supplied by ABB for a particular
case must always be taken into account!
5.2.1 Method of installation A – Installation of
the base irons
Due to different switchgear dimensions, one or
more parts make up the base irons. Their
installation is usually carried out by site personnel
and should, if possible, be performed under the
supervision of an ABB specialist.
Method of installation - Installation of the base
irons:
•
When base irons are composed of several parts,
connect them with a bolt in the required order
and position them horizontally
•
Lay the irons in the specified position on the
concrete floor as shown in the relevant foundation
drawing
•
Mark out holes for drilling. These holes are
for the anchoring bolts that will fix the base
irons in the floor
•
Put the plugs in the holes and use the bolts
to attach the base irons to the floor. Do not
tighten the bolts until the base irons have been
correctly leveled
•
Carefully level the base irons both longitudinally
and transversally over the entire length and
correct the height by using strips with a suitable
thickness and a levelling instrument. Usually
the top edge of floor frame should be 2 mm
above the finished floor surface (Fig. 26, 29)
Tolerances for laying the floor frame are:
•
Evenness tolerance: ±1 mm within a measuring
length of 1 m
•
Straightness tolerance: 1 mm per 1 m, but not
Rated voltage
Panel width FT
Aisle width
1)
G
Switchgear room door width
Switchgear room door height
2)
Opening in ceiling if transported
through roof:
Width
Length
Ceiling load
3)
kV
mm
mm
mm
mm
mm
mm
kg/m
2
12
500
1300
700/1200
2400
1000
1500
1200
Dimension chart of structural data (Also see figures 5/1 to 5/11)
1) Pay attention to the appropriate national standards.
2) Applies to low-voltage compartments of standard height.
3) Approximate numbers depending on the type of panels.
more than 2 mm over the entire length of the
frame
•
After levelling the base irons, the bolts can be
tightened. The adjusted position of the base
irons on the concrete floor must not be changed
during this operation
Check again and, if need be, correct any deviations.
•
Weld the individual parts of the base irons
inside the “C” profile together at the seams
so that a conductive connection is achieved
•
When the floor top covering is applied, carefully
backfill the floor frame, leaving no gaps
•
The base irons must not be subjected to any
harmful impacts or pressures, particularly during
the installation phase
If these conditions are not respected, problems
during switchgear assembly and possibly with
movement of the withdrawable parts, as well as
with the opening and closing of the doors cannot
be ruled out.
5.2.2 Method B – installation on the levelled
concrete floor
Installation directly on the levelled concrete floor
makes much higher demands on the floor levelling,
which must, in this case, fulfil the same tolerances
as the base irons during method A installation.
Fastening is carried out by anchoring bolts in the
concrete floor.
•
Clean the switchgear installation area carefully
•
On the slab, visibly trace the perimeter of all
the units making up the switchgear according
to the relevant draw-ing, taking the minimum
wall and obstacle clearances into account
•
Level the floor both longitudinally and
transversally, evenness tolerance is ±1 mm over
a measuring length of 1 m
•
Drill the floor at the intended fixing points,
referring to the slab drilling drawings. To make
the holes, use a hammer drill with a bit according
to the steel plugs used
•
Insert the plugs in the holes and put the individual
panels on the traced perimeters of the units
to create the switchgear
•
Level the units and then bolt them together
in the front and rear part
•
Fix the units with bolts with special washers
(the coupling material is supplied on request)
•
In the case of a metal floor - to make the holes,
use a drill with a suitable bit for the type of
fixing to be made (through or threaded hole)
5.2.3 Method C – installation on a raised false floor
In this case, fastening of the units is carried out
by welding outside panels to the steel floor frame
in the places where the frame is larger than the
base of the switchgear, i.e. on the outside lateral
walls of the unit row. This method of installation
is not recommended if seismic resistance is
required.
•
Clean the installation area
•
After installation of the frame, take any necessary
measures for perfect earthing of the frame with
galvanized steel strips with min. dimensions
30x4 mm. Two earthing connections are
recommended for a panel row longer than
approx. 5 panels
•
Place the units on the frame according to the
relevant foundation drawings, taking the
minimum wall and obstacle clearances into
account
•
Level the units and then bolt them together
in the front and rear part
•
Carry out attachment by welding the outside
panels to the steel floor frame in the place
where the frame juts out from the switchgear
bottom, i.e. on the outside lateral walls of the
unit row. This method of installation is not
recommended if seismic resistance is required
•
In the case of a metal floor - to make the holes,
use a drill with a suitable bit for the type of
fixing to be made (through or threaded hole)