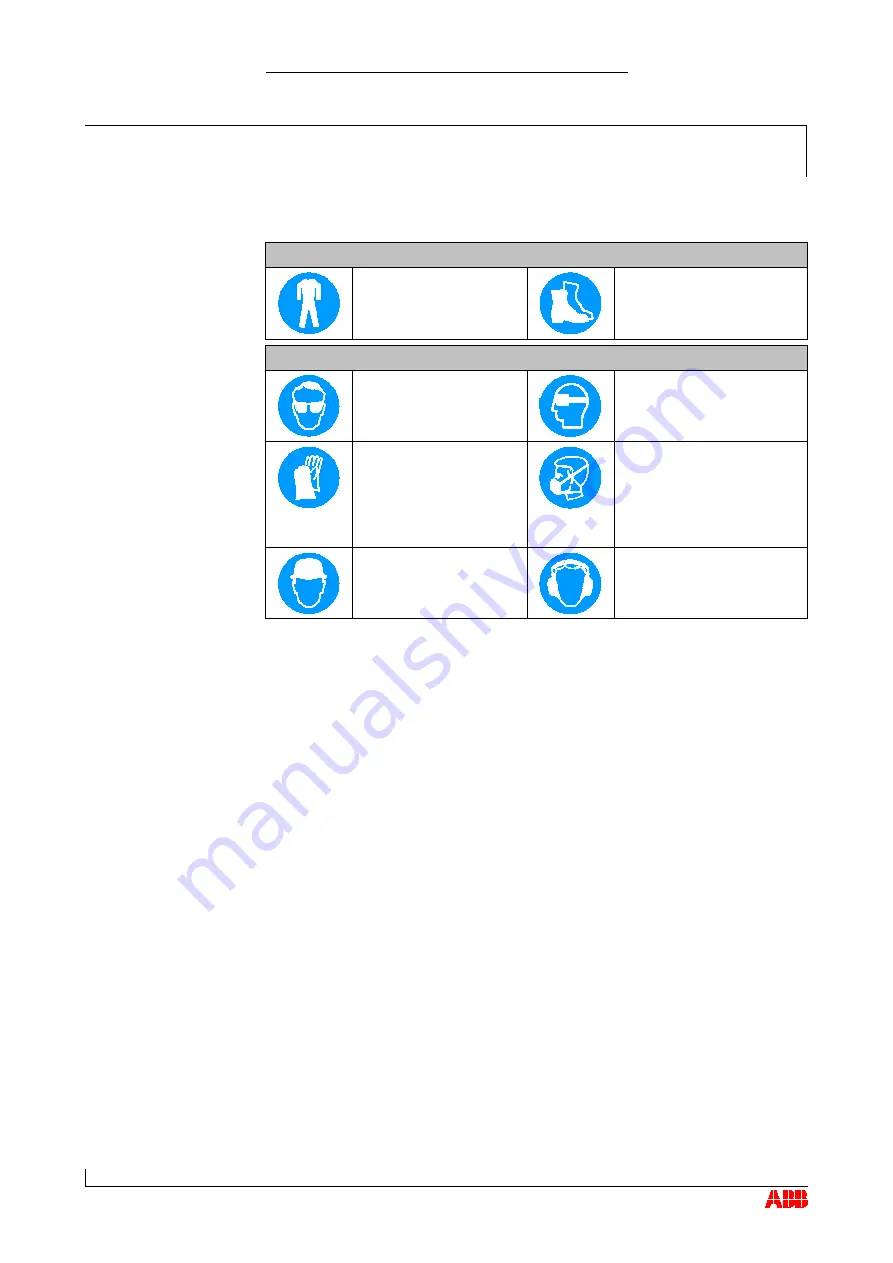
Operation Manual / TPS44-F.. - TPS61-F..
Safety
2
Definition of mandatory signs
2.3
Page 19
© Copyright 2016 ABB. All rights reserved.
Sept
em
ber
2016
H
ZT
L2412_
EN
R
ev
is
ion
F
Definition of mandatory signs
2.3
To be worn at all times
Protective clothing
Safety footwear to protect
against mechanical hazard
and risk of falling
To be worn according to the specific work
Safety glasses
Safety goggles
Safety gloves to protect
against
- Mechanical hazard
- Chemical hazard
- Thermal hazard
Respiratory mask to protect
against
- Dusts
- Gases
Safety helmet
Ear protection
2.3