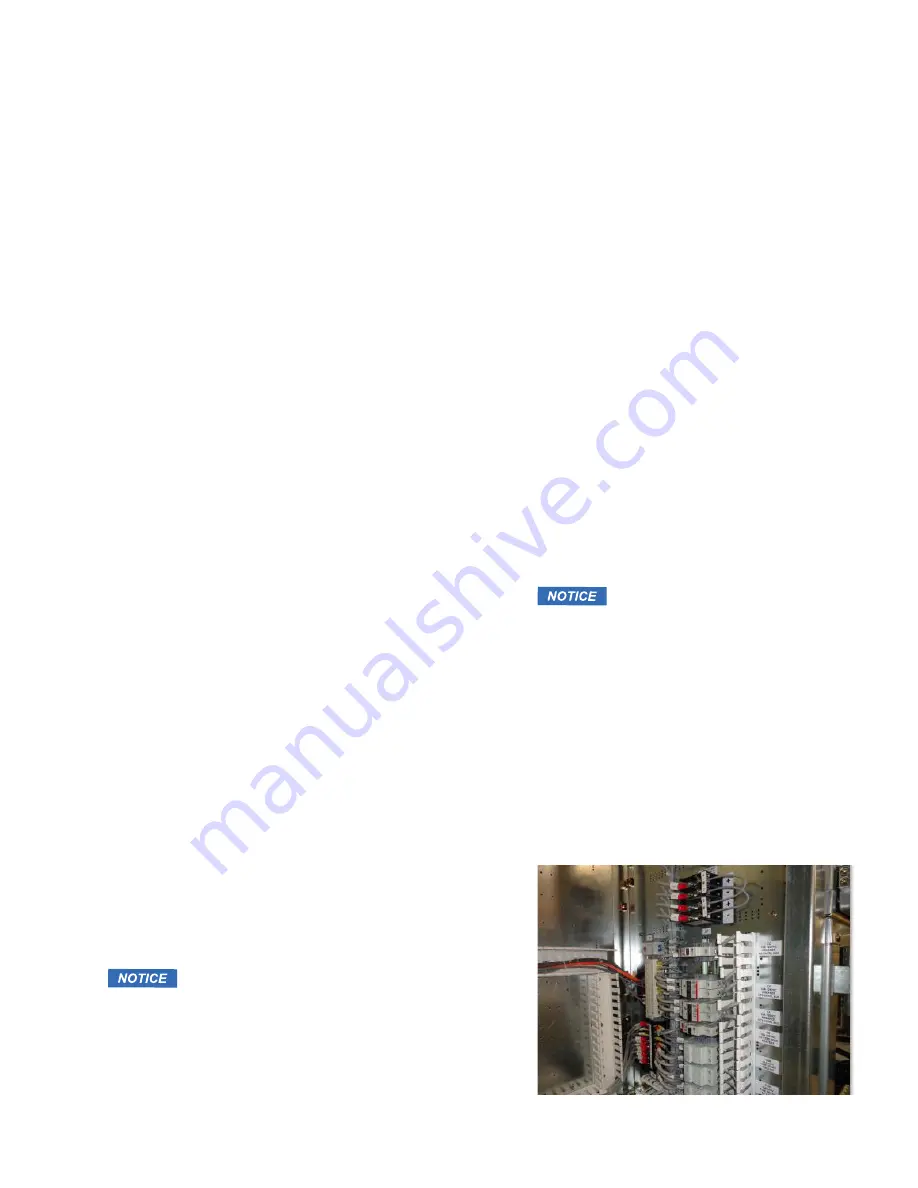
6
R E LI AG E A R
®
N D A NS I N A R ROW DE S IG N ME TA L- CL A D S WITCHG E A R
—
Receiving, handling and storage
Receiving inspection
Before shipment, the equipment is inspected and
marked with its number and position. Switchgear
frames are factory-assembled and shipped with the
doors closed. The factory ships circuit breakers in
separate cartons, or as an option, inside the
switchgear frame with the breakers in disconnect
position.
Upon receipt of the equipment, examine the
shipment for damage or missing components.
Check the contents against the packing list before
discarding any packing material. Check the
consignment for completeness and lack of any
damage (e.g., moisture and its detrimental effects).
In case of doubt, the packing must be opened and
then properly resealed, putting in new drying agent
bags, when intermediate storage is necessary.
If any quantities are short, or defects or transport
damage are noted, these must be documented on
the respective shipping document. Notify ABB and
the carrier at once of any discrepancies. If there is
damage from improper handling, file a claim for
damages at once with the carrier and notify ABB.
Always photograph damage. Unless otherwise
noted in the project contract documents, ABB
standard shipments are “FOB Factory.” ABB is
not responsible for damage after delivery of
the equipment to the carrier.
3.2 Handling the equipment
Transport panels upright. Take the high center
of gravity into account. Carry out loading
operations only when it has been ensured that all
precautionary measures to protect personnel and
materials have been taken into consideration.
Notice: All doors and panels must be in place and
securely fastened before moving the equipment.
Storing the equipment
Leave the equipment on the shipping base. Store
all equipment indoors in a well-ventilated area.
The storage building should have a well-drained
paved floor. The temperature should be above 60 °F.
The air should be dry (60% maximum humidity).
The shipping sections are ship wrapped in plastic
for protection during shipment only. Remove the
plastic wrap after placing into storage. Cover with
heavy wrapping paper or other moisture barrier.
Use materials that will not trap moisture inside the
unit. Do not cover louvered openings.
For long-term storage, i.e., durations exceeding
two weeks, or in high-humidity areas, use heaters
to keep the interior dry. Bring power for the heaters
to the load terminals of the device that controls the
heater circuits (figure 1).
Notice: Remove all the packing
materials from the switchgear
before energizing the heaters.
Open the breaker or cutout device
that controls the heaters when using
a separate power source.
For circuit breakers shipped in crates, store circuit
breakers upright in their original shipping carton
oriented as indicated on the shipping crates. For
circuit breakers shipped in the switchgear, do not
remove for storage. See document 1VAL057601-MB
for details on breaker storage.
—
01 Heater load
terminals in low
voltage compartment
—
01
Summary of Contents for ReliaGear ND
Page 2: ......