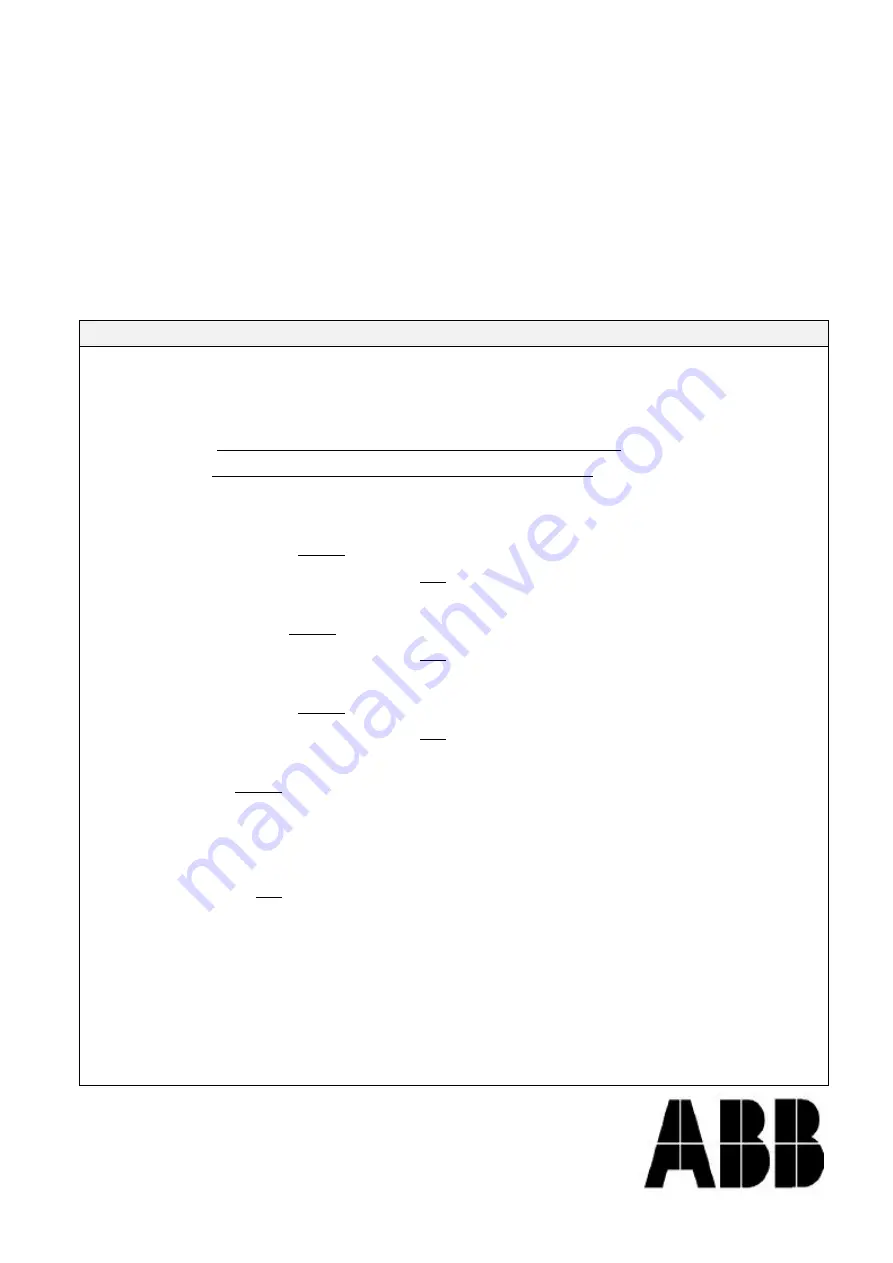
Softstart
Installation and
maintenance instruction
PS D75 ... 840
PS DH30 ... 720
5309 680-1
Edition 8 Dec-01
(English)
Contents
1A. Brief instructions .......................................................................................................................... 3
1B. Brief instructions for installations that require CE-marking............................................................ 4
Mandatory requirement by the European Union (EU)................................................................ 4
Installations of Softstarters type PSD(H) in industrial network: ........................................ 4
Installation of Softstarters type PSD(H) in public network: .............................................. 5
2. Mounting ....................................................................................................................................... 8
3. Installation...................................................................................................................................... 9
3.1 PS D75 ... 840 without built-in electronic overload protection.............................................. 9
3.2 PS D75 ... 840 / PS DH30 ... 720 with built-in electronic overload protection. ................... 11
4. Description, settings, signals ........................................................................................................ 13
4.1 PS D75.. 840 without built-in electronic overload protection.............................................. 15
4.2 PS D75 .. .840 / PS DH30 ... 720 with built-in electronic overload protection .................... 16
5. Operation and function ................................................................................................................. 17
5.1 PS D75 ... 840 without built-in electronic overload protection............................................ 17
5.2 PS D75 ... 840 / PS DH30 ... 720 with built-in electronic overload protection .................... 18
6. Trouble shooting .......................................................................................................................... 19
6.1 PS D without electronic overload protection...................................................................... 19
6.1.1 Different status on LED's and signal relays ......................................................... 19
6.1.2 Fault codes.......................................................................................................... 21
6.1.3 Flow chart............................................................................................................ 22
6.2 PS D(H) with electronic overload protection...................................................................... 24
6.2.1 Different status on LED's and signal relays .......................................................... 24
6.2.2 Fault codes.......................................................................................................... 26
6.2.3 Flow chart............................................................................................................ 27
7. Technical data.............................................................................................................................. 30
8. Circuit Diagrams .......................................................................................................................... 32
9. Dimensions .................................................................................................................................. 33