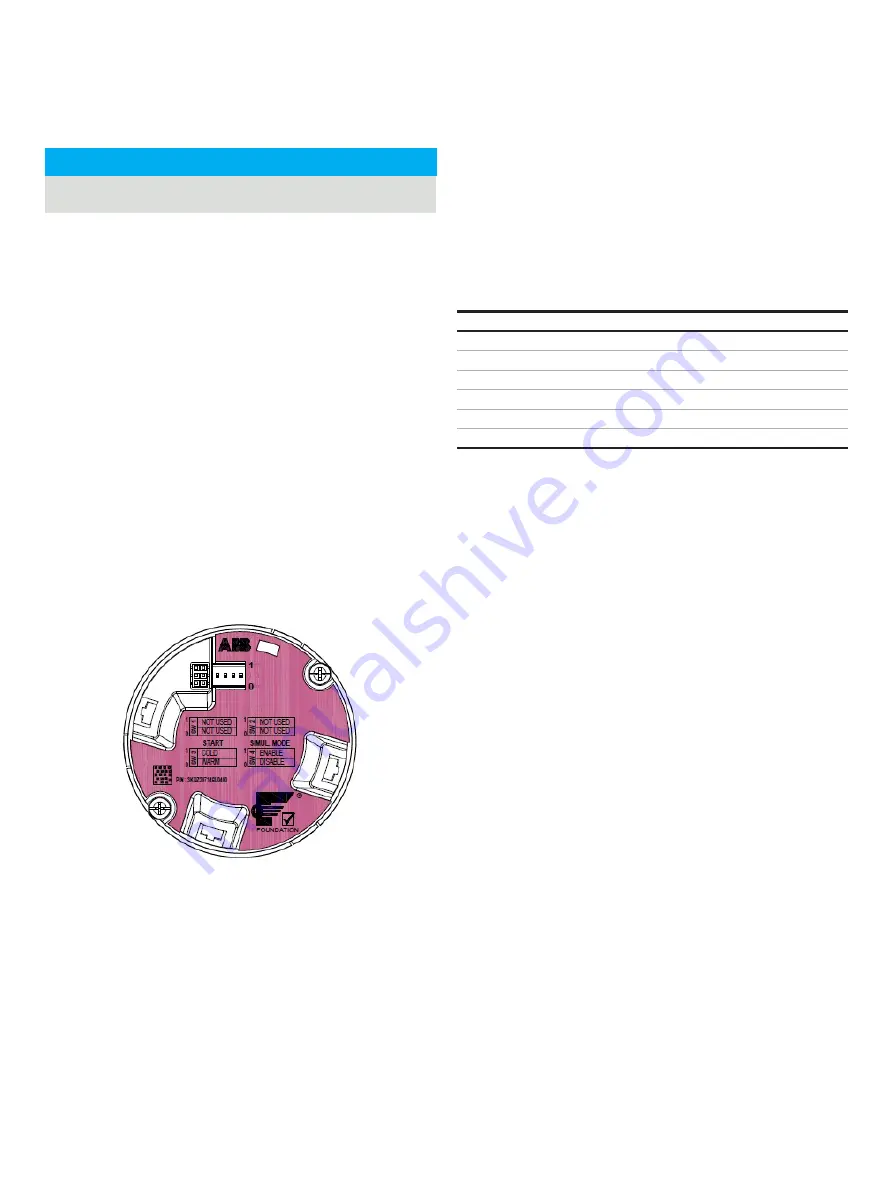
J DF 3 0 0 |
FI EL D I N D I C ATO R | O I/J D F 3 0 0 - EN R E V. B
11
Test voltage withstand capability can no longer be ensured
when this protective circuit is used.
7 Electronic Board
Fault protection
The JDF300 FF electronic implements a special circuitry for the
fault current protection. Whenever a fatal failure occurs and the
current consumption increase over the 20 mA, this circuitry
provides to disconnect the device from the bus, in order to
preserve the rest of the bus that, otherwise, risks to drop down
all the other connected devices.
On board switches
On the electronic unit under the display there are 4 dip switches
with the following functionality:
• Switch 1 and 2
are reserved for future use
• Switch 3
selects the start mode between COLD and WARM-
START UP. When in ON position and COLD start is selected, it
means that when a new power cycle is executed the device
will be set to a predefined basic configuration.
Some parameters of the HMITB, RB and MAO blocks are
written to a well defined value while all the other function
blocks are set to their FF standard default (“Initial Values”).
Figure 7 Electronic board view
After the Cold Start the JDF300 is ready to work displaying the
value of MAO_IN1 (input 1) with its default Subtag and unit code
while the quality status is displayed as textual format. Refer to
the Block’s table at the end of this manual to see which
parameters are forced to a default value by the Cold Start-up
function. They are in Bold/italic/underlined (pink color).
The basic parameters set by the Cold start up are the following:
Cold start-up condition
MAO_Channel
IN1 (1)
HMITB_IN1_SUBTAG
“Input 1”
HMITB_IN1_Unit
“none”
HMITB_IN_ENABLED
Only IN1 enabled (00000001)
HMITB_SEQUENCE
Disabled (1 – OFF)
HMITB_NUM_STATUS_ENA
Status byte in Text format (1)
Switch 4
selects the simulation mode which is a mandatory
requirement for FF devices.
JDF300O can simulate only diagnostic conditions writing the
error to be simulated into
“RB_FD_SIMULATE” (index 67)
.
However, this writing has effect only if the HW switch4 has
been previously moved in ON position (SIMUL MODE ENABLED).
IMPORTANT