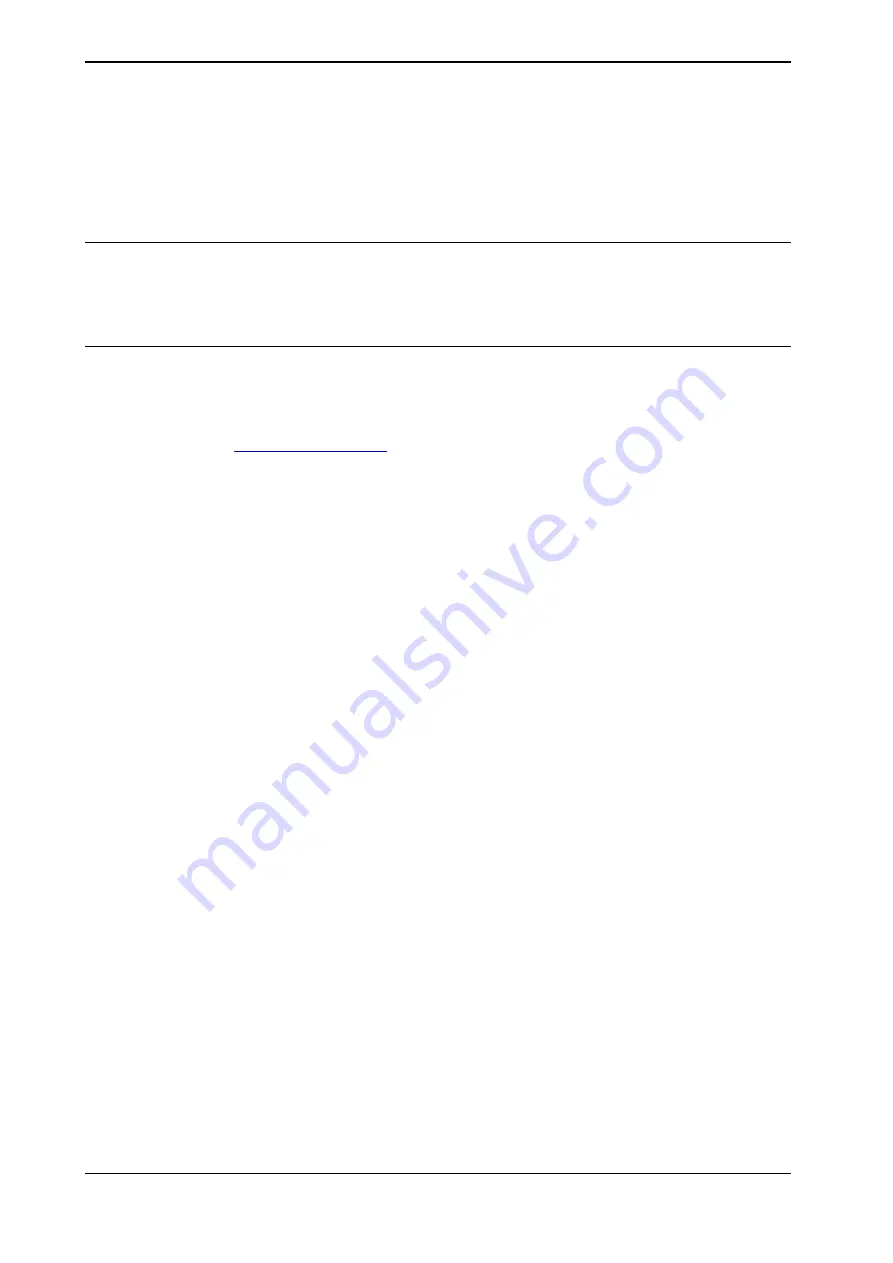
3.4 Replacement/changing activities
3.4.1 Type of lubrication in gearboxes
Introduction
This section describes where to find information about the type of lubrication,
article number and the amount of lubrication in the specific gearbox. It also
describes the equipment needed when working with lubrication.
Type and amount of oil in gearboxes
Information about the type of lubrication, article number as well as the amount in
the specific gearbox can be found in
Technical reference manual - Lubrication in
gearboxes
available for registered users on myABB Business Portal,
.
Continues on next page
142
Product manual - IRB 6700Inv
3HAC058254-001 Revision: L
© Copyright 2017 - 2020 ABB. All rights reserved.
3 Maintenance
3.4.1 Type of lubrication in gearboxes
Summary of Contents for IRB 6700I
Page 1: ...ROBOTICS Product manual IRB 6700Inv ...
Page 16: ...This page is intentionally left blank ...
Page 40: ...This page is intentionally left blank ...
Page 182: ...This page is intentionally left blank ...
Page 672: ...This page is intentionally left blank ...
Page 704: ...This page is intentionally left blank ...
Page 720: ...This page is intentionally left blank ...
Page 722: ...This page is intentionally left blank ...
Page 729: ......