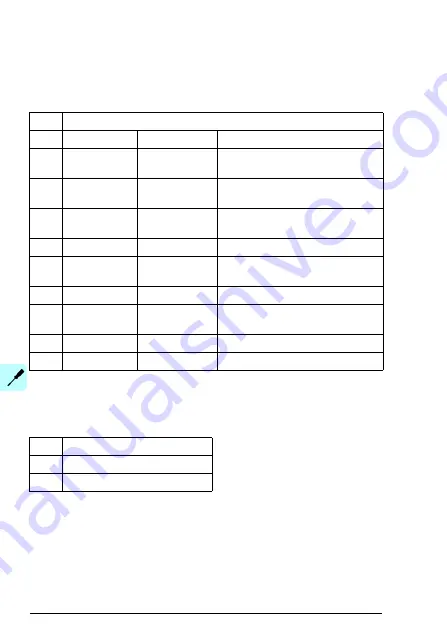
24 Electrical installation
Terminal designations
Pin allocation of the encoder interface connector 1
(X31)
Pin allocation of the power supply connector
(X81)
X31
HTL
No.
Name
Specification Description
1
VCC_ENC_1
15 V DC
Encoder channel 1 power supply
output
2
COM_ENC_1 0 V
Encoder channel 1 supply/signal
common (ground)
3
A+_1
0…15 V DC
Encoder channel 1 signal A+
input
4
A-_1
0…15 V DC
Encoder channel 1 signal A- input
5
B+_1
0…15 V DC
Encoder channel 1 signal B+
input
6
B-_1
0…15 V DC
Encoder channel 1 signal B- input
7
Z+_1
0…15 V DC
Encoder channel 1 signal Z+
input
8
Z-_1
0…15 V DC
Encoder channel 1 signal Z- input
9
SHIELD_1
N/A
Encoder channel 1 cable shield
X81
Description
1/+
Supply voltage
2/-
Supply ground
Summary of Contents for FSE-31
Page 1: ... OPTIONS FOR ABB DRIVES FSE 31 pulse encoder interface module User s manual ...
Page 4: ......
Page 10: ...10 Safety instructions ...
Page 17: ...Hardware description 17 Layout 6 7 3 4 1 2 1 5 X31 Pin no 1 2 3 4 5 6 7 8 9 ...
Page 21: ...Mechanical installation 21 5 3 4 2 ...
Page 22: ...22 Mechanical installation ...
Page 36: ...36 Technical data ...