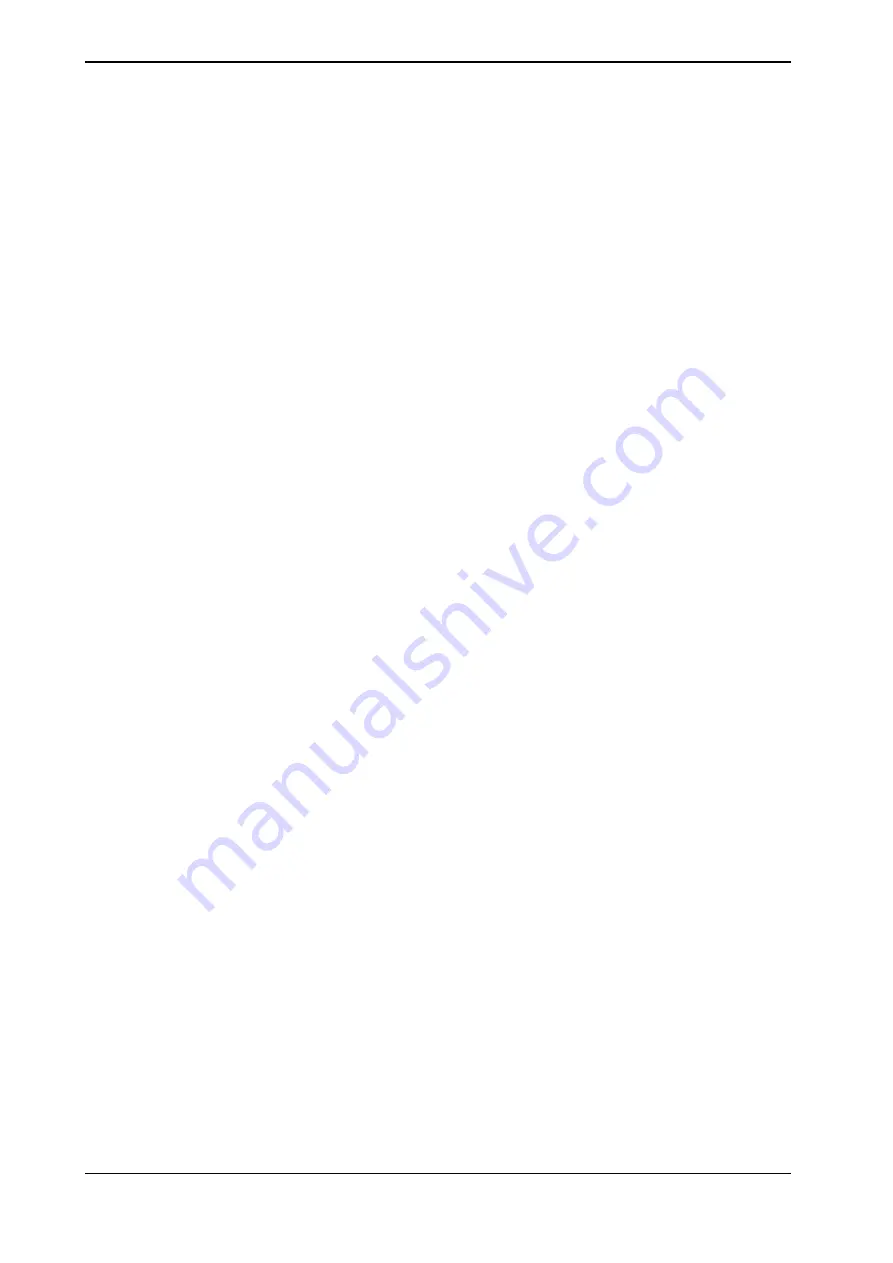
this task. It's not so important which robot task is Master as long as it is only one
task. The other robot tasks set this value to TRUE to make them slaves.
The other variables define which camera or cameras this robot should handle.
Note that it must be in order, robot 1 could handle camera 1-2 but not camera 1
and 3. Be careful when deciding camera numbers!
Normally there is one PartCamX.mod module for each camera. This module is
selected during teach-in in the mechanical tab of FlexLoader Vision and later on
loaded into the robot task that controls that camera. See example below.
! Code in InitializeMain in robot task T_ROB2
bIsSlaveVisionRobot:=TRUE;
! Assign camera 3-4 to robot 2.
nStartAcceptCamera:=3;
nStopAcceptCamera:=4;
! Code in main program of T_ROB2
GrabImage CAMERA_NO_3;
! ...normal handling to of receiving coordinates
! Then call to pick part, code in the PartCam3.mod in T_ROB2.
PickCam_3;
At start up FlexLoader Vision and RAPID code will co-work to make the
PartCam3.mod and PartCam4.mod load into T_ROB2 task according to the variable
setting.
Single camera feeder with multiple coordinate transfer for multiple picking
In certain applications, the robot is expected to pick more than one part in one pick
cycle. This can reduce cycle times.
FlexLoader Vision needs to be configured for multiple coordinate transfer (see
FlexLoader Vision ConfigurationEditor).
The main code uses following instructions to handle this case.
VAR num nPartsToPick;
! This call will make the robot pick 3 parts from the same image,
first and second pick must be a part found in position 1 and
third pick must be found in position 2.
! If this combination is not found vision system will try a new
image twice and then give up.
nPartsToPick:=PickMultiPartsAtCamera(CAMERA_NO_1,
\NumberOfPartsToPick:=3,
\DesiredPositions:=[1,1,2],\MaxImageRetries:=2);
In the part module file there must be a special pick routine named as in example
below. It should handle how to pick the different parts.
PROC PickMultiPartsCam_1(num PartNo,num Position)
VAR dnum dnGripper;
! Switch off configuration control to be sure to reach the
position, those will switch on in MoveFromCamera1.
ConfJ\Off;
ConfL\Off;
! TODO - set correct gripper to use depending on which part to
pick
Continues on next page
98
Product manual - FlexLoader SC 6000
3HAC051768-001 Revision: D
© Copyright 2014-2020 ABB. All rights reserved.
7 RAPID program
7.2 FlexLoader application functionality
Continued
Summary of Contents for FlexLoader SC 6000
Page 1: ...ROBOTICS Product manual FlexLoader SC 6000 ...
Page 8: ...This page is intentionally left blank ...
Page 12: ...This page is intentionally left blank ...
Page 78: ...This page is intentionally left blank ...
Page 172: ...This page is intentionally left blank ...
Page 174: ...This page is intentionally left blank ...
Page 176: ...This page is intentionally left blank ...
Page 178: ...This page is intentionally left blank ...
Page 182: ...This page is intentionally left blank ...
Page 184: ...This page is intentionally left blank ...
Page 186: ...This page is intentionally left blank ...
Page 192: ...This page is intentionally left blank ...
Page 224: ...This page is intentionally left blank ...
Page 283: ......