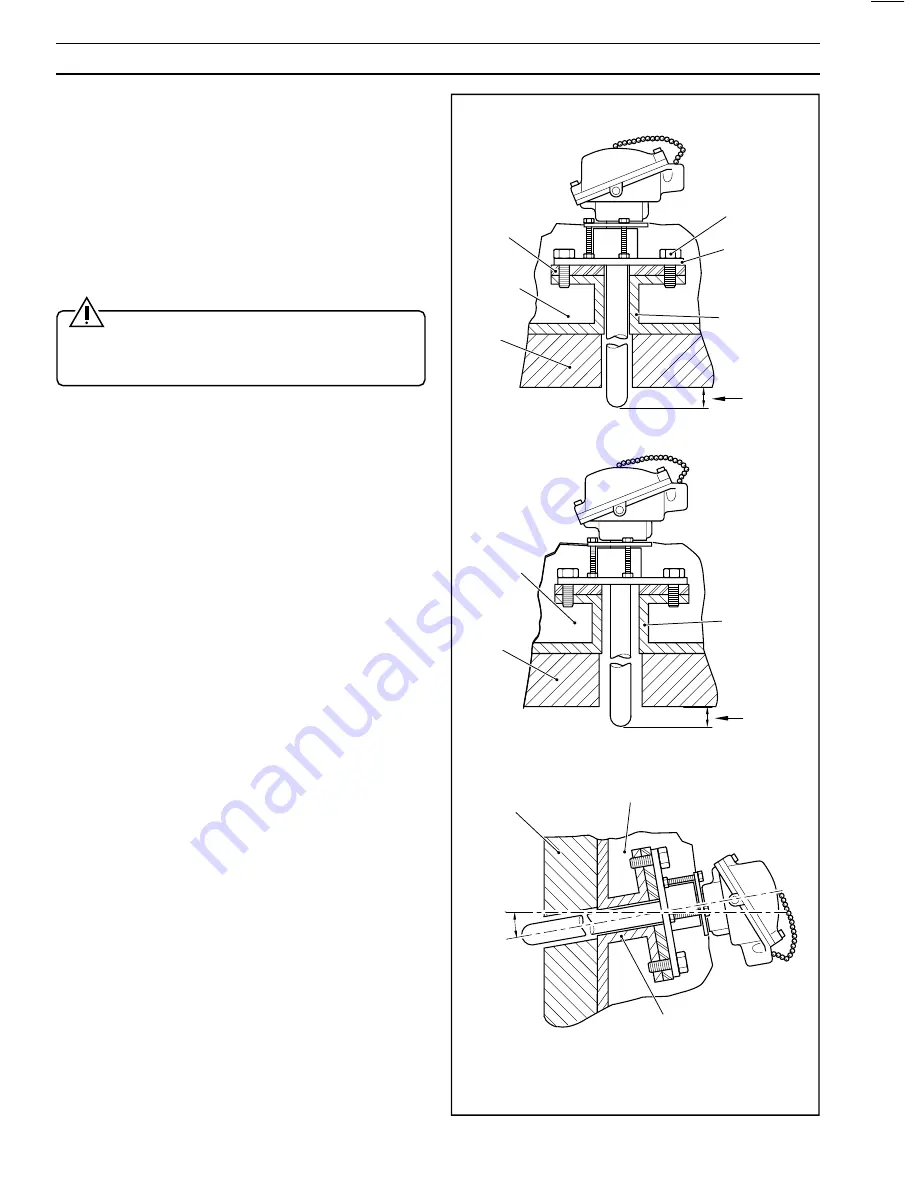
8
3.2.1
Mounting Configurations – Fig. 3.3
The probe may be fitted horizontally or, preferably, vertically
for prolonged high temperature operation.
Mount the probe through the furnace wall using the preferred
method shown in Fig. 3.3A. Ensure that a sufficiently large
hole is provided through the mounting – min. bore 1.65ins
(42mm) diameter – to avoid damage to the probe during
insertion or use.
Drill the fixing flange to suit the local fixing requirements before
assembling the probe – see Section 2.3.
Caution. To prevent furnace gas from
contaminating the reference air, always ensure that the
clamp ring, fixing flange and sealing ring are fitted to the
probe as described in Section 2.3.
With applications such as high temperature incinerators, fluid
bed boilers and ore roasters, where the level of water vapor in
the waste gases to be measured can be extremely high, it is
important that the mounting flange of the probe, including any
standoff which may be used, is thermally insulated to minimize
condensation within the probe – see Fig. 3.3A.
Condensation within the probe sheath, particularly in outdoor
installations, can be sufficient to allow water to come into
contact with the hot ceramic (zirconia) tube leading to thermal
shock and failure of the sensor. This problem is most likely to
occur on such installations where the plant is shut down
regularly over the weekend. Additionally, take care to protect
the head of the probe from the elements in outdoor
installations.
Raising the temperature of the probe as rapidly as possible
assists in reducing the level of condensation. This is not
possible on some processes where the plant temperature is
gradually raised to the normal operating level. The
temperature rise at the head of the probe can be assisted by
having a large clearance hole in the refractory allowing hot
gases to get up to the mounting flange/standoff – see Fig.
3.3B.
Horizontal installations are more likely to exhibit the problems
described. Where it is not possible to mount the probe in the
vertical position, install the probe with a slope of at least 10 to
15
°
downwards from the head of the probe – see Fig. 3.3C.
Clamp Bolt
Fixing Flange
Support Tube
and Flange
5.90
(150) min.
Furnace
Wall
Thermal
Insulation
Packing
A – Standard Configuration
Support Tube
and Flange
Thermal
Insulation
Furnace
Wall
5.90
(150) min.
B – Improved Probe Heating
Support Tube
and Flange
Thermal
Insulation
Furnace Wall
10
°
Min.
C – Inclined Configuration
Dimensions in inches (mm)
…3
INSTALLATION
Fig. 3.3 Probe Mounting