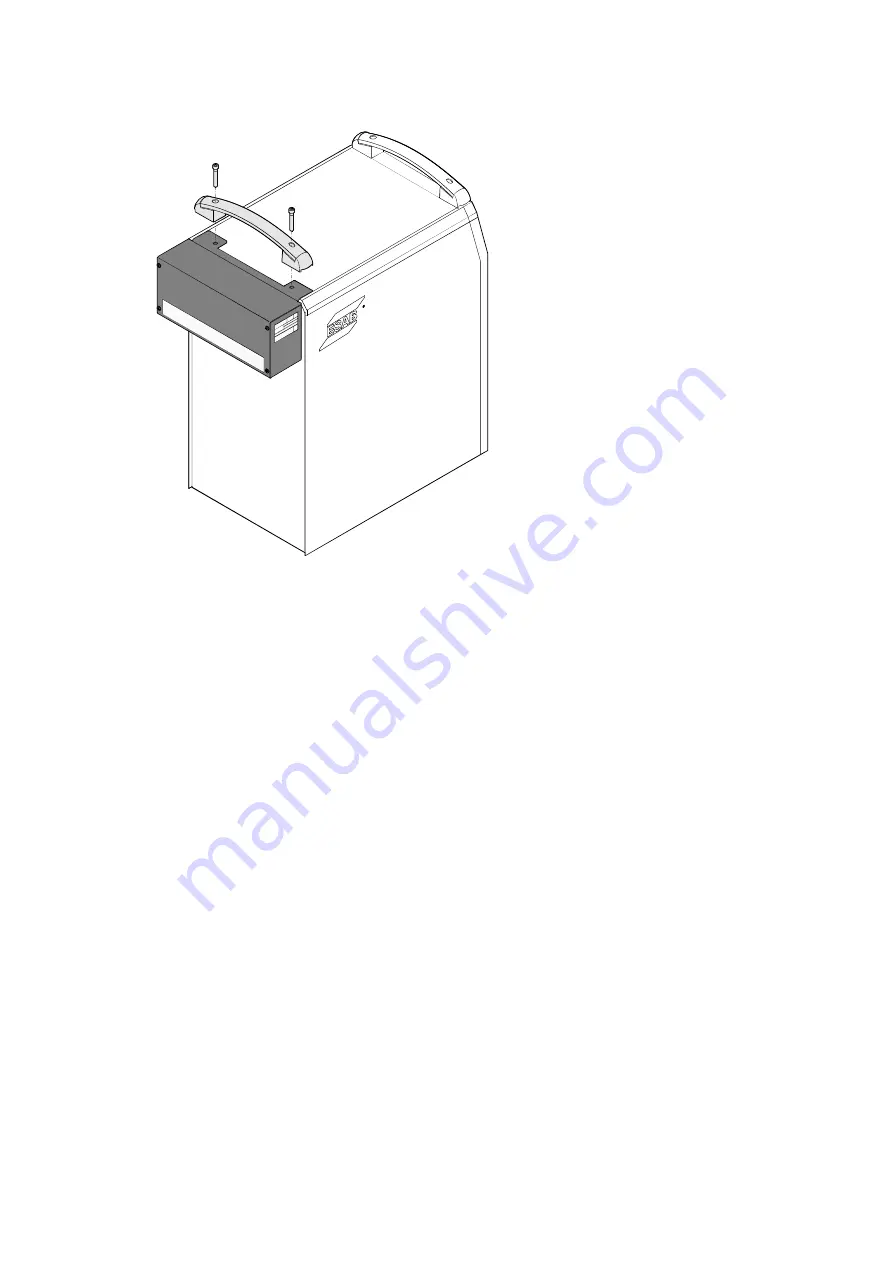
- 17 -
cr09_02
Mounting W82 on Mig 5000i
S
On the power source, remove the two screws that holds the rear handle.
S
Remove handle.
S
Place the interface box onto the welding power source.
S
Place handle on top of the interface box.
S
Fasten interface box and handle with the two screws.
Mounting W8
2
on Mig 4002c, Mig 5002c and Mig 6502c
S
On the power source, use the “keyholes” that is normally used for the chain
holding the gas tube.
S
Place the interface box onto the welding power source.
S
Fasten interface box with the two screws.
Installing the wire feeder and control unit
Mount the feeder unit and controller according to the mounting instruction that
comes in the same box as the units.
Power source
Unpack and install the power source according to the user manual.
Installing the welding gun
Unpack and install the welding gun according to the user manual.
Installing the bobbin holder
Unpack and install the bobbin holder according to the user manual, refer to the
assembly instruction for Robot Bobbin Kit “RoboFeed 3004HW”.