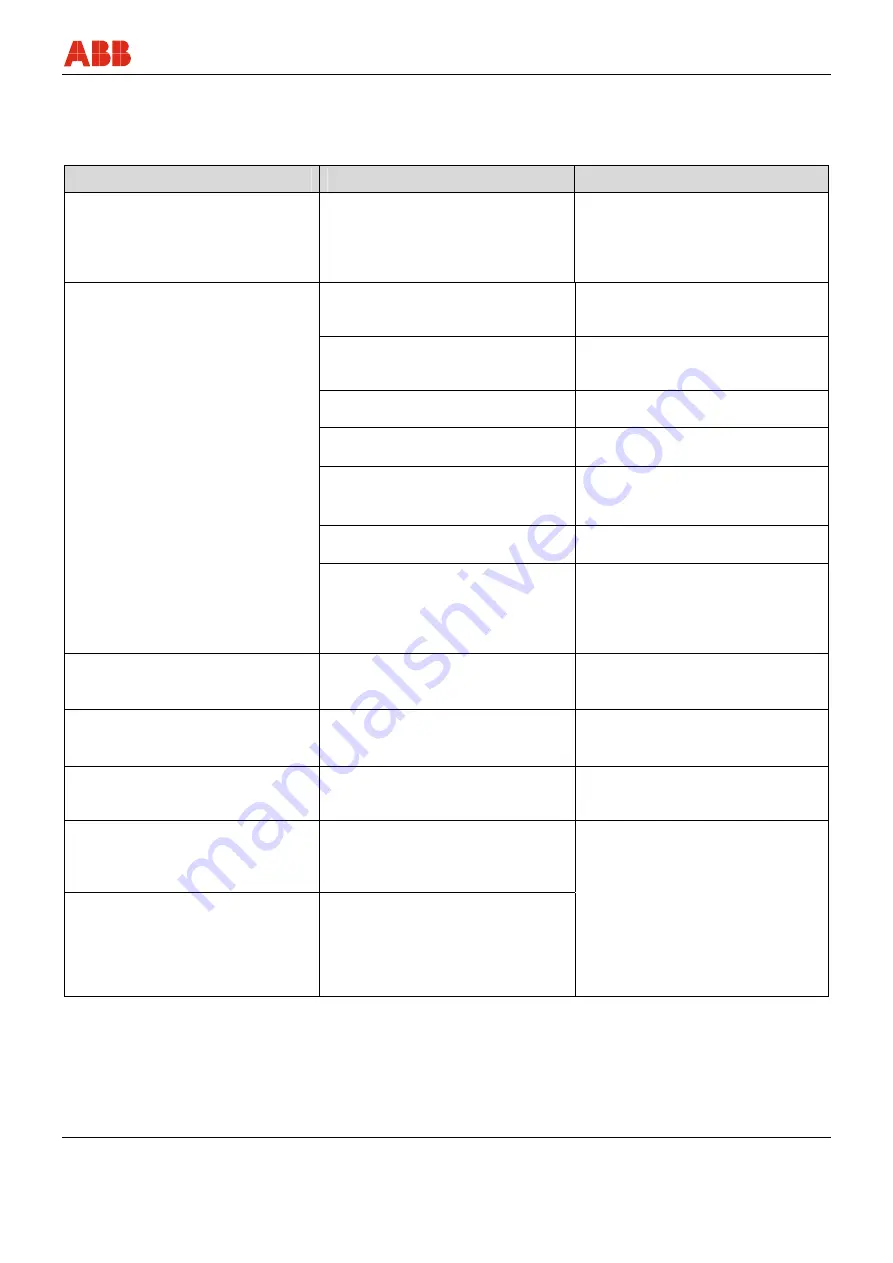
Trouble
shooting
OI/PME/LME/EAN823/EBN853/EBN861-EN
37
8 Trouble
shooting
This chapter only covers hardware-related errors. For additional troubleshooting information, refer to the online
help for the operator interface.
Error
Possible cause
Troubleshooting
Valve cannot be moved by actuator.
Failure either on the actuator or the
valve (e.g., stuffing box tightened
too much).
Disconnect actuator from valve.
If the actuator moves, the valve is
the possible cause.
If the actuator does not move, the
actuator is the possible cause.
Incorrect electronic unit or incorrect
data record.
Compare information on name
plates for actuator and electronic
unit.
Incorrectly configured electronic
unit.
Check / change. Change the
settings via the parameterization
software.
No communication with the control
system.
Check wiring.
Incorrect wiring between actuator
and electronic unit.
Check wiring.
Defective motor/brake.
Check the winding resistance of the
motor and brake.
Check the brake lock.
Binary inputs on the electronic unit
are not wired.
Make connection.
The actuator does not respond.
Brake does not release (no
mechanical "click").
Check the brake air gap (approx.
0.25 mm (0.010 inch)) and
electrical connection to the brake.
Check winding resistance of the
brake coil.
Actuator does not run in AUT mode,
although “AUT” is selected in the
user interface.
Digital input 1 (DI 1) not wired.
Make connection.
Check the software settings for the
digital inputs.
Actuator does not respond to control
(LED 5 flashing at 1 Hz) (software
version 2.00 and higher).
Actuator to manual mode (MAN) via
ISF.
Switch actuator to automatic mode
(AUT).
LEDs in the commissioning and
service panel (ISF) are flashing
synchronously.
Actuator is not adjusted properly.
Adjust actuator.
LEDs flash alternately.
Electronic unit / drive malfunction.
Malfunction when approaching the
end position.
Actuator in limit range of positioning
sensor.
Drive the actuator beyond the
adjusted end position, either
manually or using the buttons on the
ISF; (if necessary disconnect from
valve before)
Drive the actuator back into the
operating range and connect it to the
valve.
Readjust the actuator for the
operating range.