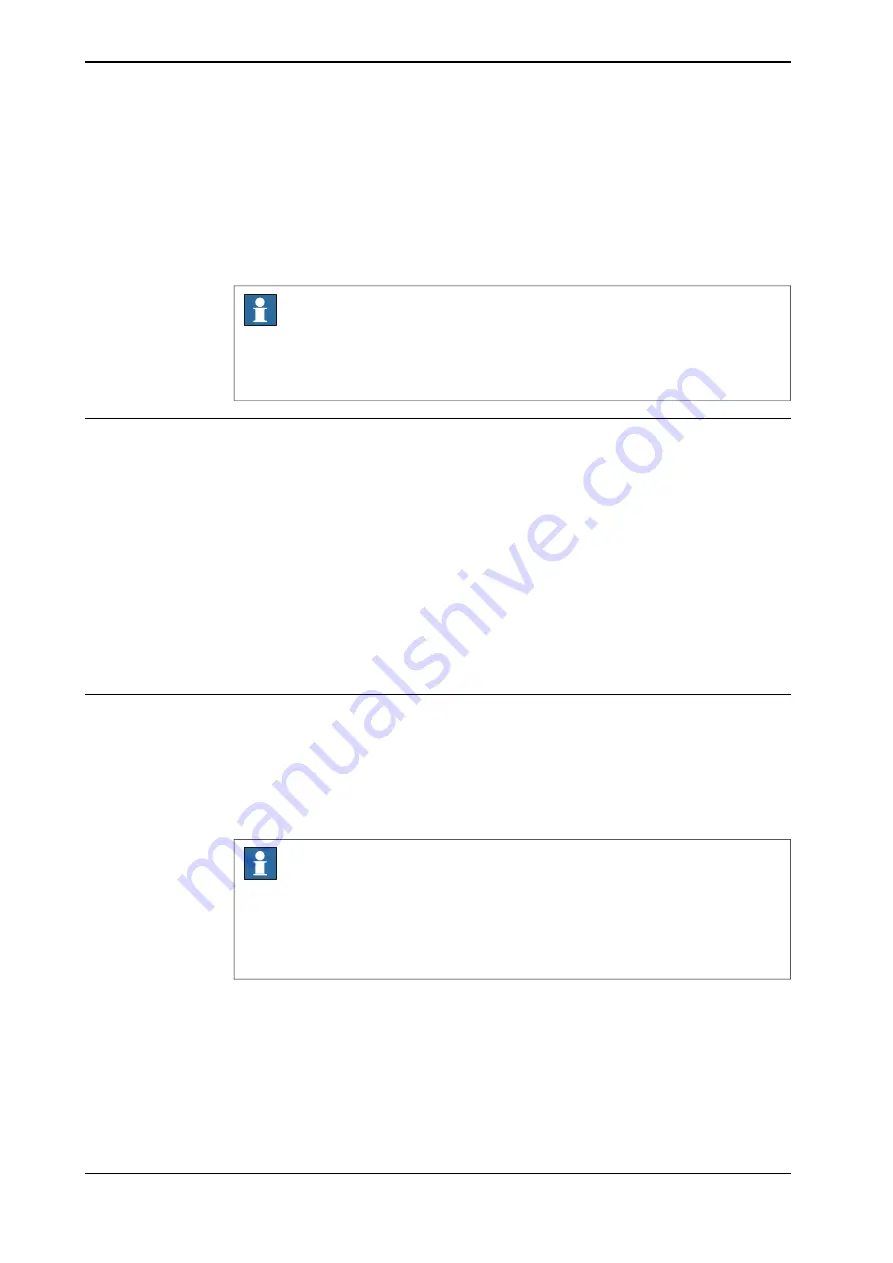
The I/O template configuration file,
PN_Internal_Anybus.cfg
, can be obtained from
the RobotStudio or the IRC5 controller.
•
In the RobotWare installation folder in RobotStudio
:
...\RobotPackages\
RobotWare_RPK_<version>\utility\service\ioconfig\PROFINET\
•
On the IRC5 Controller
:
<SystemName>\PRODUCTS\
<RobotWare_xx.xx.xxxx>\utility\service\ioconfig\PROFINET\
Note
Navigate to the RobotWare installation folder from the RobotStudio
Add-Ins
tab,
by right-clicking on the installed RobotWare version in the
Add-Ins
browser and
selecting
Open Package Folder
.
Communication status
To have control of the communication status, that is, to know if the controller (for
example, a PLC) to device communication is working or not, the following scheme
could be used.
The controller can set one signal during start-up or within the controller loop, this
signal (on the internal device) could then be attached to a system input in the robot
controller as a communication supervision signal. If the communication between
the controller and the device is interrupted, all the inputs of the internal device will
go to fail safe state (that is, be set to zero only) after the specified watchdog time.
This means that the user defined communication supervision signal will also go
to zero. The watchdog time is configured in the external PROFINET configuration
tool.
Limitations
The predefined PROFINET internal anybus device,
PN_Internal_Anybus
has the
following limitations:
•
8 digital input bytes and 8 digital output bytes but can be increased to the
maximum value, which is 64 digital input bytes and 64 digital output bytes.
•
Both the input and output map starts at bit 0 and ends at bit 63.
Note
If the PROFINET anybus device loses connection with the master, the configured
input signals are cleared (reset to zero). The output signals are kept and are
possible to change.
When the connection is re-established, the controller updates the input signals.
24
Application manual - PROFINET Anybus Device
3HAC050968-001 Revision: C
© Copyright 2008-2016 ABB. All rights reserved.
3 Software overview
3.1 Information about the Anybus device
Continued
Summary of Contents for DSQC1000
Page 1: ...Application manual PROFINET Anybus Device ...
Page 6: ...This page is intentionally left blank ...
Page 14: ...This page is intentionally left blank ...
Page 18: ...This page is intentionally left blank ...
Page 22: ...This page is intentionally left blank ...
Page 34: ...This page is intentionally left blank ...
Page 42: ...This page is intentionally left blank ...
Page 44: ......
Page 45: ......