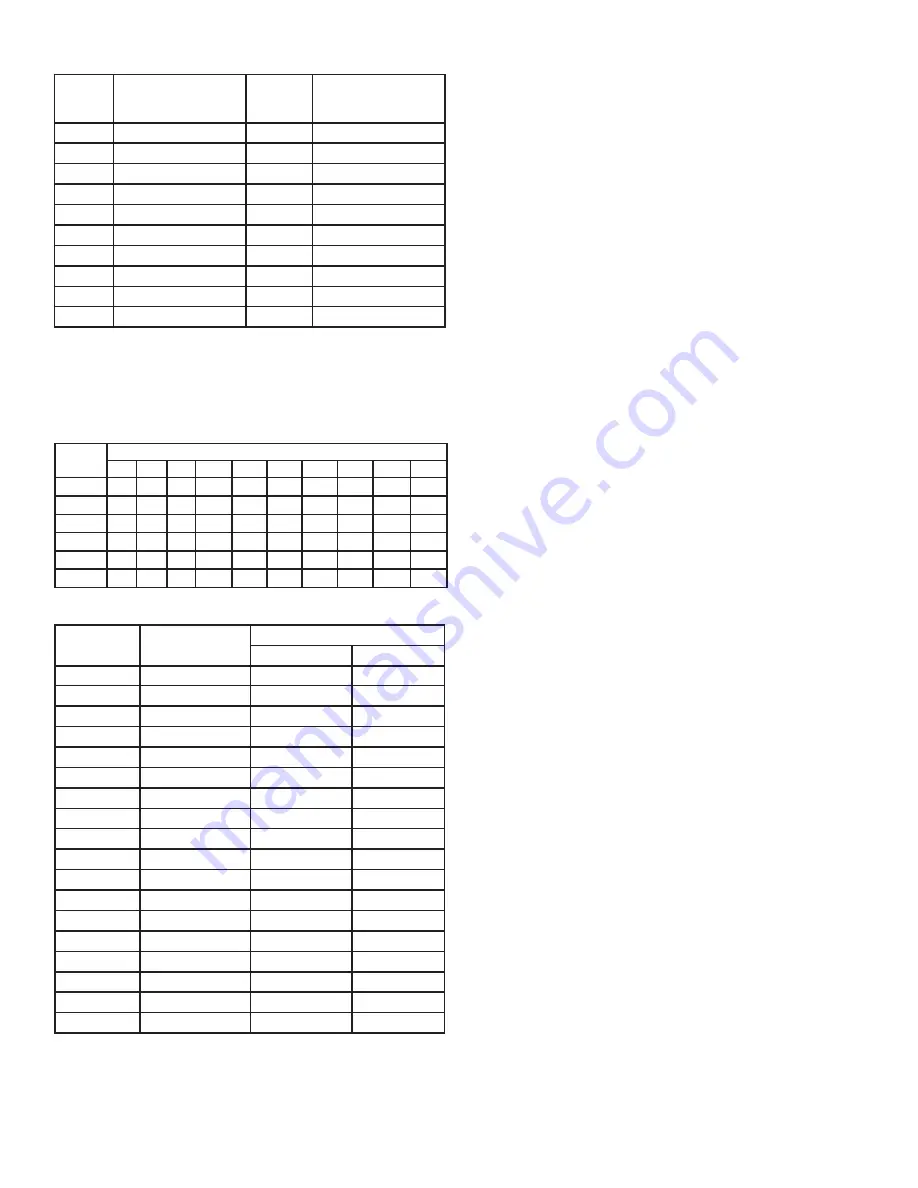
6
Table 7 - Viscosity of Oil in the Grease
DN
Viscosity for Loads Up
To 18% of Dyn. Cap*
(Cst @ Oper. Temp.)
DN
Viscosity for Loads Up
To 18% of Dyn. Cap*
(Cst @ Oper. Temp.)
2500
700
35000
125
5000
650
40000
100
7500
580
45000
85
10000
500
50000
75
12500
425
75000
62
15000
390
100000
42
17500
325
125000
30
20000
280
150000
27
22500
235
175000
22
25000
200
200000
20
DN = Bore Diameter (mm) x RPM
* = For loads above 18% of dynamic capacity an EP grease with the
above viscosity oil is recommended.
Table 8 - Regreasing Intervals (Months) *
(Based on 12 Hours Per Day - 66
° Max.)
Size,
mm
RPM*
250 500 750 1000 1250 1500 2000 2500 3000 3500
35-60
8
6
4
3
2
1
.5
.5
.25
.25
65
7
5
3
2
1
1
.5
.25
.25
70-85
6
4
3
2
1
.5
.25
.25
90-100
5
3
2
1
.5
.5
.25
110-130 4
3
2
1
.5
.25
140-160 3
2
1
.5
.25
Table 9 - Maximum RPM (Adapter Mount)
Shaft Size,
mm
Basic Bearing
Description
Maximum RPM
Grease
Oil
35
22308K C3
4300
5300
40
22209K C3
5600
7000
45
22210K C3
5300
6700
50
22211K C3
4500
5600
55
22212K C3
4000
5000
60
22213K C3
3600
4500
65
22215K C3
3400
4300
70
22216K C3
3200
4000
75
22217K C3
3000
3800
80
22218K C3
2600
3400
85
22219K C3
2400
3200
90
22220K C3
2200
3000
100
22222K C3
2000
2800
110
22224K C3
1800
2400
115
22226K C3
1700
2200
125
22228K C3
1600
2000
135
22230K C3
1500
1900
140
22232K C3
1400
1800
If the RPM of the application falls between 20% and 80% of
maxiumum RPM (Table 9 for adapter mount, Table 10 for direct
mount), pack the lower half of the housing one-third to one-half
full. If the RPM of the application is less than 20% of maximum
RPM, pack bearing housing cavity 100% full. If the RPM
exceeds 80% of maximum RPM, do not add grease in the lower
half of the housing nor in the cap.
At each regreasing cycle, for applications up to 80% of
maximum RPM, slowly add grease until fresh grease is
seen purging at the seals. Regreasing should be done while
running. Remote re-greasing lines should be added to avoid
endangering personnel.
If the RPM is greater than 80% of maximum RPM, add 4
strokes of a handgun at each regreasing cycle for bores up
to 50 mm. For bores greater than 50 mm up to 130 mm add 8
strokes of handgun at each regreasing cycle. For bores greater
than 130 mm add 16 strokes of a handgun at each regreasing
cycle. For units running above 80% of maximum RPM, running
temperature should be monitored. If a drastic change in running
temperature is noted, it is recommended to remove the used
grease completely and recharge with fresh grease per the
above instructions.
Select a grease with a viscosity at operating temperature
which will provide full film lubrication (See Table 7). Use a
30°C-55°C increase in bearing temperature above ambient,
depending on RPM and load. Use Table 8 as a general guide for
regreasing the bearings. A small amount of grease at frequent
intervals in preferable to a large amount of grease at infrequent
intervals. For special applications involving high speeds or high
temperatures consult your local ABB Motors and Mechanical
representative for MPT products.
Applications such as conveyor pulleys and fans are shipped
to a job site with bearings already mounted to the shafts.
Since these units may be stored for long periods of time in
unprotected areas subject to rain, dust, etc., bearings should be
packed 100% full and so tagged at bearing assembly to prevent
contamination or corrosion of the bearings.
Summary of Contents for DODGE USN 500 Series
Page 15: ...15 ...