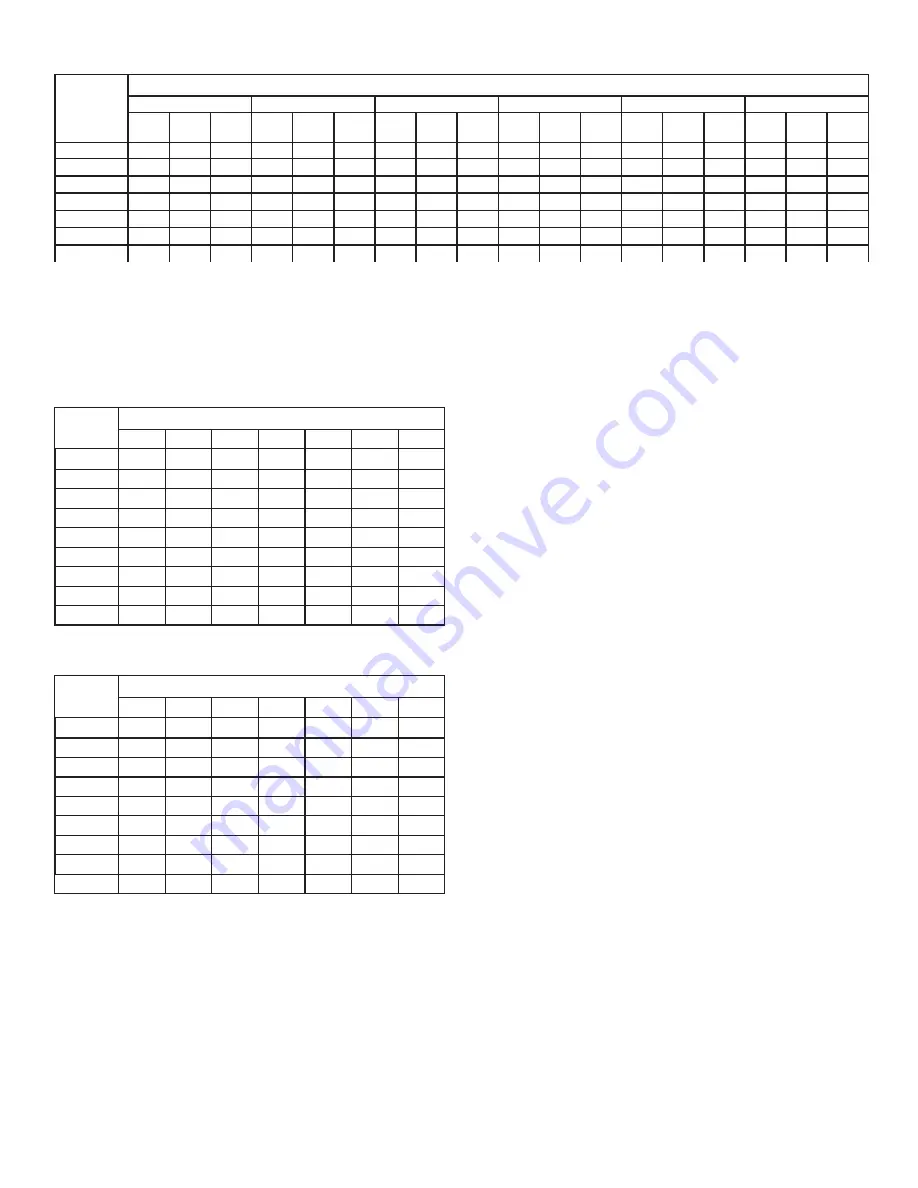
4
Table 1 - Oil Volumes
Reducer
Size
Volume of Oil Required to Fill Reducer to Oil Level Plug
Position A
Position B
Position C
Position D
Position E
Position F
Fluid
Oz.
Qts. Liters Fluid
Oz.
Qts. Liters Fluid
Oz.
Qts. Liters
Fluid
Oz.
Qts. Liters Fluid
Oz.
Qts. Liters Fluid
Oz.
Qts. Liters
(H)SCXT105
20
5/8
.59
24
3/4
.71
20
5/8
.59
24
3/4
.71
36
1
1.06
44
1
.30
(H)SCXT205
24
3/4
.71
28
7/8
.83
28
7/8
.83
28
7/8
.83
56
1-3/4
1.66
72
2-1/4
2.13
(H)SCXT305A
28
7/8
.83
48
1-1/2
1.42
44
1
1.30
44
1
1.30
80
2-1/2
2.37
100
3
2.96
(H)SCXT405A
48
1-1/2
1.42
72
2-1/4
2.13
68
2
2.01
60
1
1.78
128
4
3.79
156
4
4.61
(H)SCXT505A
108
3
3.19
136
4-1/4
4.02
124
3
3.67
120
3-3/4
3.56
248
7-3/4
7.33
288
9
8.52
SCXT605
144
4-1/2
4.30
184
5-3/4
5.40
144
4-1/2
4.30
160
5
4.70
384
12
11.40
352
11
10.4
SCXT705
240
7-1/2
7.10
288
9
8.50
240
7-1/2
7.10
296
9-1/4
8.80
608
19
18.0
552
17-1/4 16.30
Below 15 RPM output speed, oil level must be adjusted to reach the highest oil level plug (P).
Refer to Figure 3 for mounting positions.
Note:
If reducer position is to vary from those shown in Figure 3, either more or less oil may be required. Consult Dodge product support.
U.S. Measure: 1 qt. = 32 fl. oz. = .94646 liters.
All liquid measure amounts are approximate.
CAUTION: Do not use oils containing slippery additives
such as graphite or molybdenum disulphide in the reducer
when backstop is used. These additives will destroy sprag
action. Failure to observe these precautions could result in
damage to, or destruction of, the equipment.
GUIDELINES FOR TORQUE-ARM REDUCER
LONG-TERM STORAGE
During periods of long storage, or when waiting for delivery or
installation of other equipment, special care should be taken
to protect a gear reducer to have it ready to be in the best
condition when placed into service.
By taking special precautions, problems such as seal leakage
and reducer failure due to lack of lubrication, improper
lubrication quantity, or contamination can be avoided. The
following precautions will protect gear reducers during periods
of extended storage:
Preparation:
1. Drain the oil from the unit. Add a vapor phase corrosion
inhibiting oil (VCI-105 oil by Daubert Chemical Co.) in
accordance with Table 4.
2. Seal the unit air tight. Replace the vent plug with a standard
pipe plug and wire the vent to the unit.
3. Cover the shaft extension with a waxy rust preventative
compound that will keep oxygen away from the bare metal.
(Non-Rust X-110 by Daubert Chemical Co.
4. The instruction manuals and lubrication tags are paper
and must be kept dry. Either remove these documents
and store them inside or cover the unit with a durable
waterproof cover which can keep moisture away.
5. Protect the reducer from dust, moisture, and other
contaminants by storing the unit in a dry area.
6. In damp environments, the reducer should be packed
inside a moisture-proof container or an envelope of
polyethelene containing a desiccant material. If the reducer
is to be stored outdoors, cover the entire exterior with a
rust preventative.
Table 2 – Lubrication Recommendations – ISO Grades for Ambient
Temperatures of 15ºF to 60ºF
Output
RPM
Reducer Size
1
2
3
4
5
6
7
301-400
220
220
150
150
150
150
150
201-300
220
220
150
150
150
150
150
151-200
220
220
150
150
150
150
150
126-150
220
220
220
150
150
150
150
101-125
220
220
220
220
150
150
150
81-100
220
220
220
220
220
150
150
41-80
220
220
220
220
220
150
150
11-40
220
220
220
220
220
220
220
1-10
220
220
220
220
220
220
220
Table 3 – Lubrication Recommendations – ISO Grades for Ambient
Temperatures of 50ºF to 125ºF
Output
RPM
Reducer Size
1
2
3
4
5
6
7
301-400
320
320
220
220
220
220
220
201-300
320
320
220
220
220
220
220
151-200
320
320
220
220
220
220
220
126-150
320
320
320
220
220
220
220
101-125
320
320
320
320
220
220
220
81-100
320
320
320
320
320
220
220
41-80
320
320
320
320
320
220
220
11-40
320
320
320
320
320
320
320
1-10
320
320
320
320
320
320
320
Notes:
Below -23ºF call application engineering.
20ºF to -22ºF use Mobil SHC 627.
Above 125ºF use Mobil SHC 634.
NOTE: Pour point of lubricant selected should be at least 10°F lower than
expected minimum ambient starting temperature. See last page of manual
for lubricant viscosity classification equivalents. Special lubricants
may be required for food and drug industry applications where contact
with the product being manufactured may occur. Consult a lubrication
manufacturer’s representative for his recommendation.