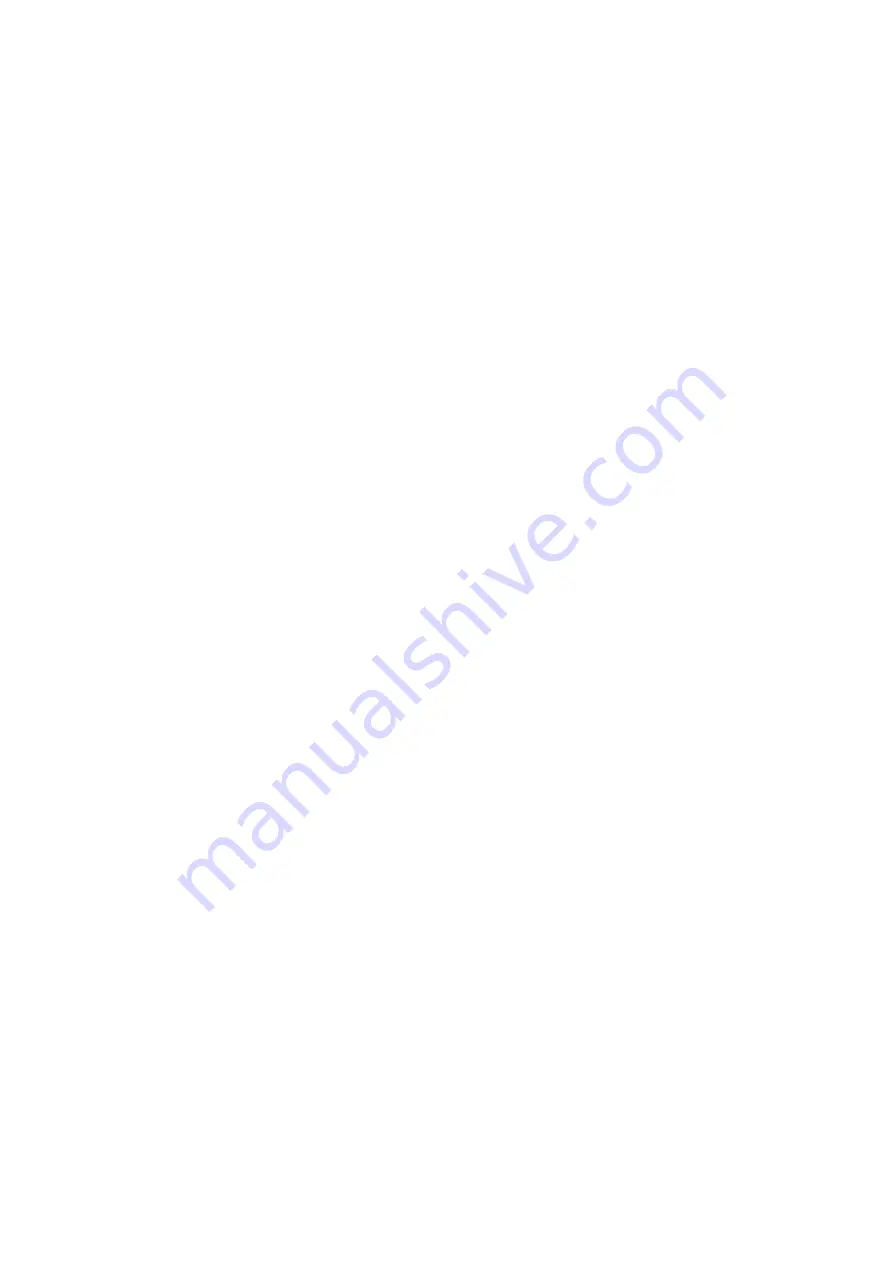
InsPECTIon And MAInTEnAnCE
25
2.
Look for any visual damage to the structure of the motor such as cracks in the structure and
corrosion in screw joints, etc. If external damage to the motor is observed and to such an extent that
it prevents operation or represents a safety risk, replace the motor as soon as possible.
3.
Verify that the earth connection is correct, re-assemble if necessary
4.
Check the condition of low and high voltage connectors, replace if necessary
NOTE:
If there is a potential safety risk, inform management and take necessary emergency
measures.
6.2.3. Bearings
The bearings, see Figure 1, are lifetime lubricated and require no maintenance. Listen for any abnormal
noise or increased vibration from the bearings and contact your local ABB sales office if such exist. The
expected lifetime of the grease inside the bearing is dependent on the motor duty cycle and external
loads. The lower the bearing temperature and operational speed and torque, the longer the expected
grease and bearing life.
6.2.4. External shaft seal
The motor is equipped with an external shaft seal on the D-end, see Figure 1. The expected lifetime of the
seal is dependent on the motor duty cycle and the external environment. Check for wear and replace if
necessary. A damaged external shaft seal might compromise the IP class of the motor.
NOTE: The external shaft seal should never run dry, lubricate if necessary.
6.2.5. Shaft spline
Inspect the shaft splines, see Figure 1, to ensure no excessive wear has occurred, and apply a suitable
molybdenum disulfide grease to the splines. See 4.2 for further information.
6.2.6. External cleaning
External cleaning can be carried out when necessary when mounted in vehicle and at revisions.
As a basic rule, a mechanical process (scraper, compressed air) should be carried out first and when
necessary.
NOTE:
External cleaning when the motor is mounted in vehicle, when necessary, is to be carried out
with dielectric fluid, like FAST-ECO (manufacturer: Smyth Morris). (Cleaning with water may
introduce a risk of rust and damage to the interior of the motor).
NOTE:
It is recommended that external cleaning during revisions is carried out with water and a
detergent like NEUTRA-PON (manufacturer: Henkel) or similar alkaline detergent. When using
alkaline detergents, it is very important to rinse off all detergent thoroughly.