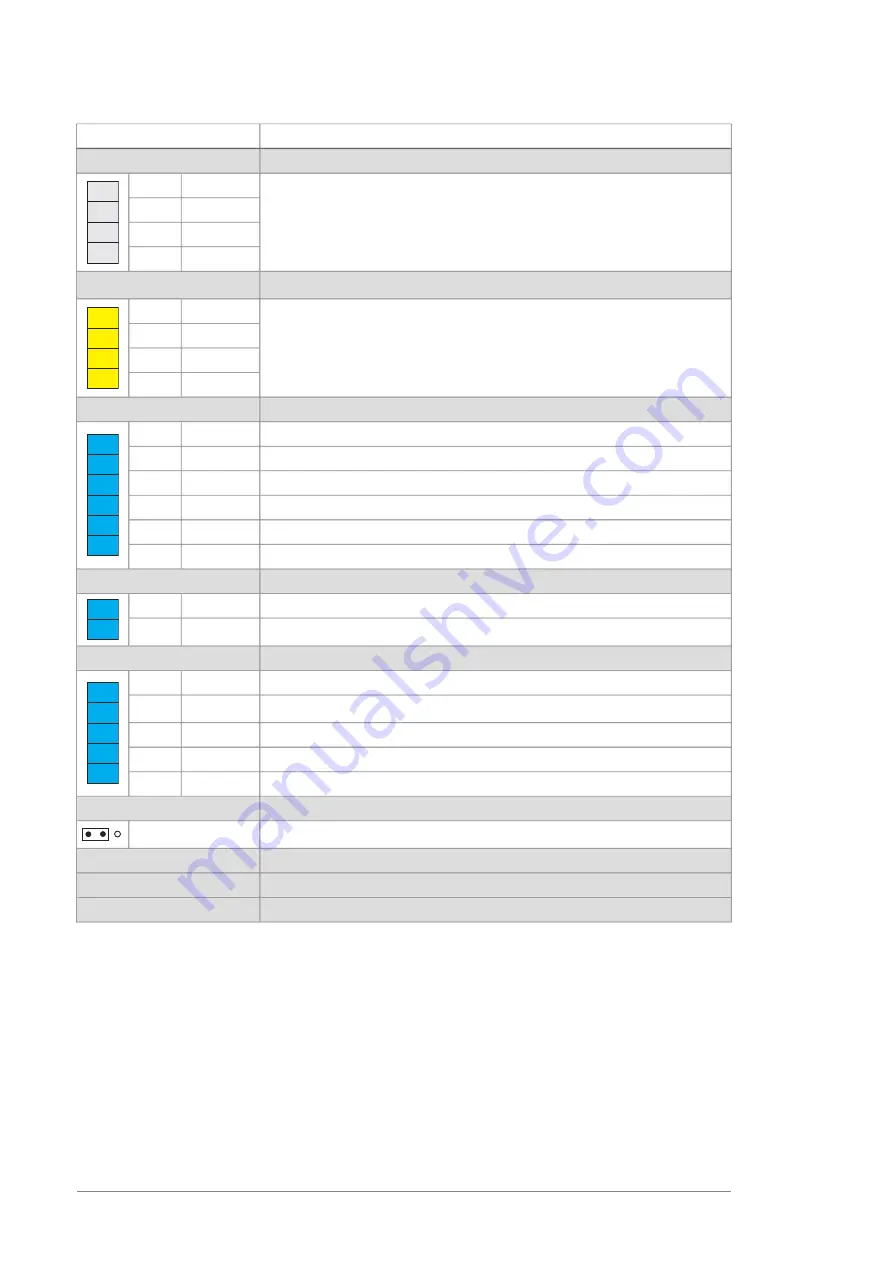
Description
Terminal
Drive-to-drive link
XD2D
Not in use by default
SHIELD
4
4
3
2
1
BGND
3
A
2
B
1
Safe torque off
6)
XSTO
Factory connection. Both circuits must be closed for the unit to start (IN1
and IN2 must be connected to OUT).
IN2
4
4
3
2
1
IN1
3
SGND
2
OUT
1
Digital inputs
XDI
(0 -> 1 = fault reset)
DI6
6
3
2
1
6
5
4
Not in use by default. Can be used for eg. earth fault monitoring.
DI5
5
Auxiliary circuit breaker fault
DI4
4
MCB feedback
(0 = main contactor/breaker open)
DI3
3
Run enable
(1 = run enable)
DI2
2
Temp fault
(0 = overtemperature)
DI1
1
Digital input/outputs
XDIO
Not in use by default
DIO2
2
2
1
Not in use by default
DIO1
1
Auxiliary voltage output
XD24
Digital input/output ground
DIOGND
5
3
2
1
5
4
+24 V DC 200 mA
7)
+24VD
4
Digital input ground
DICOM
3
+24 V DC 200 mA
+24VD
2
Not in use by default. Can be used for eg. emergency stop.
DIIL
1
Ground selection
J6
Ground selection jumper
8)
J6
Not in use in supply units
X12
Control panel connection
X13
Memory unit connection
X205
1) Default use of the signal in the control program. The use can be changed by a parameter. See also the delivery-specific
circuit diagrams.
2) Use of the signal in the control program (fixed). See also the delivery-specific circuit diagrams.
3) Current [0(4)…20 mA, R
in
= 100 ohm] or voltage [0(2)…10 V,
R
in
> 200 kohm] input selected by jumper J2. Change
of setting requires reboot of control unit.
4) Current [0(4)…20 mA, R
in
= 100 ohm] or voltage [0(2)…10 V,
R
in
> 200 kohm] input selected by jumper J1. Change
of setting requires reboot of control unit.
5) Must be set to ON when the supply unit is the first or last unit on the drive-to-drive (D2D) link. On intermediate
units, set termination to OFF.
6) This input only acts as a true Safe torque off input in inverter units. In other applications (such as a supply or brake
unit), de-energizing the IN1 and/or IN2 terminal will stop the unit but not constitute a true safety function.
7) Total load capacity of these outputs is 4.8 W (200 mA at 24 V) minus the power taken by DIO1 and DIO2.
134 The control unit
Summary of Contents for ACS880-304LC Series
Page 1: ... ABB INDUSTRIAL DRIVES ACS880 304LC A019 diode supply modules Hardware manual ...
Page 2: ......
Page 4: ......
Page 30: ...30 ...
Page 34: ...34 ...
Page 46: ... Stage 1 Installation of common parts 46 Cabinet construction ...
Page 47: ... Stage 2 Module installation parts Cabinet construction 47 10 ...
Page 48: ... Stage 3 Liquid cooling system components 48 Cabinet construction ...
Page 49: ... Stage 4 AC and DC busbar installation Cabinet construction 49 10 ...
Page 50: ... Stage 5 AC and DC connection 50 Cabinet construction ...
Page 51: ... Stage 6 Cabinet fan and heat exchanger Cabinet construction 51 10 ...
Page 52: ... Stage 7 Shroud installation parts 52 Cabinet construction ...
Page 53: ... Stage 8 Door covers and explosion exhaust kit Cabinet construction 53 10 ...
Page 54: ...54 ...
Page 74: ...74 ...
Page 87: ...5 Maintenance 87 ...
Page 88: ...6 7 8 9 9 88 Maintenance ...
Page 92: ...92 ...
Page 108: ...108 ...
Page 118: ...118 ...
Page 140: ...Liquid cooled D8D module Dimensions in mm 1 mm 0 0394 in 140 Dimension drawings ...
Page 142: ...ZCU 14 control unit 142 Dimension drawings ...
Page 143: ...Support plate for ZCU 14 UDZKROH 0 GRZQ UDZKROH 0 GRZQ Dimension drawings 143 ...
Page 144: ...CIO 01 module 144 Dimension drawings ...
Page 152: ...152 ...