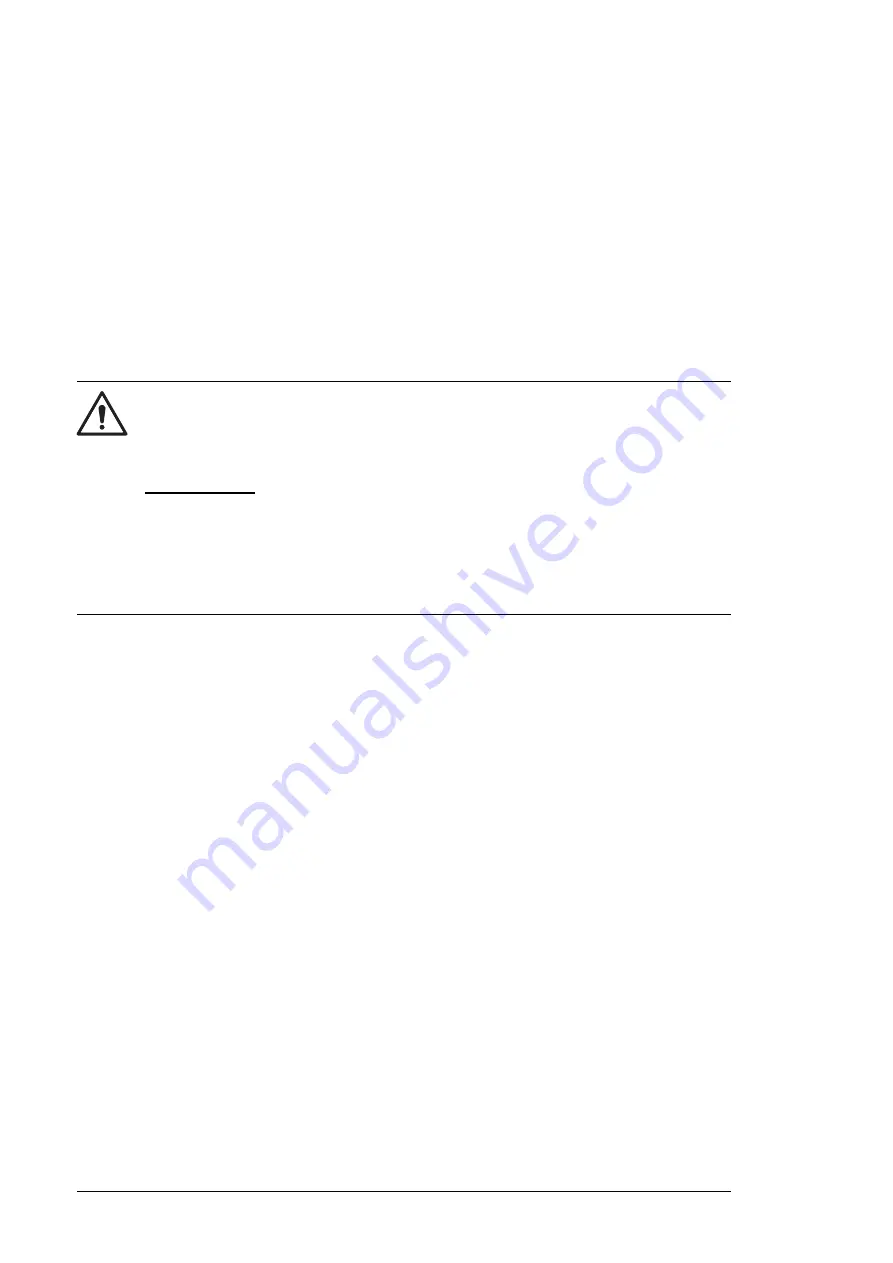
Implementing motor and motor cable short-circuit and
thermal overload protection
■
Protecting the motor and motor cable in short-circuits
The drive protects the motor cable and motor in a short-circuit situation when the motor
cable is sized according to the nominal output current of the drive.
■
Protecting the motor cables against thermal overload
The drive protects the motor cables against thermal overload when the cables are sized
according to the nominal output current of the drive. No additional thermal protection devices
are needed.
WARNING!
If the drive is connected to multiple motors, use a separate overload protection for
each motor cable and motor. The drive overload protection is tuned for the total
motor load. It may not detect an overload in one motor circuit only.
North America: The local code (NEC) requires an overload protection and a
short-circuit protection for each motor circuit. Use, for example:
• a manual motor protector
• circuit breaker, contactor and overload relay or
• fuses, contactor and overload relay.
■
Protecting the motor against thermal overload
According to regulations, the motor must be protected against thermal overload and the
current must be switched off when overload is detected. The drive includes a motor thermal
protection function that protects the motor and switches off the current when necessary.
Depending on a drive parameter value, the function either monitors a calculated temperature
value (based on a motor thermal model) or an actual temperature indication given by motor
temperature sensors.
The motor thermal protection model supports thermal memory retention and speed sensitivity.
The user can tune the thermal model further by feeding in additional motor and load data.
The most common temperature sensor types are PTC or Pt100.
For more information, see the firmware manual.
■
Protecting the motor against overload without thermal model or
temperature sensors
Motor overload protection protects the motor against overload without using motor thermal
model or temperature sensors.
Motor overload protection is required and specified by multiple standards including the US
National Electric Code (NEC) and the common UL/IEC 61800-5-1 standard in conjunction
with UL/IEC 60947-4-1. The standards allow for motor overload protection without external
temperature sensors.
The protection feature allows the user to specify the class of operation in the same manner
as the overload relays are specified in standards UL/IEC 60947-4-1 and NEMA ICS 2.
The motor overload protection supports thermal memory retention and speed sensitivity.
90 Guidelines for planning the electrical installation
Summary of Contents for ACS880-14
Page 1: ...ABB INDUSTRIAL DRIVES ACS880 14 drive modules 132 400 kW 200 400 hp Hardware manual...
Page 2: ......
Page 4: ......
Page 14: ...14...
Page 24: ...24...
Page 30: ...30...
Page 54: ...54...
Page 64: ...64...
Page 98: ...98...
Page 114: ...With twin connectors in the control panel holder 1 2 3 1 114 Electrical installation...
Page 115: ...With FDPI 02 modules OPEN TERMIN ATED 1 1 2 2 OPEN TERMINATED 3 Electrical installation 115 11...
Page 142: ...4 5 6 3 3 1 1 1 1 2 142 Installation example with full cabling panels option H381...
Page 150: ...150 Installation example with full cabling panels option H381...
Page 156: ...156...
Page 204: ...Standard configuration 204 Dimension drawings...
Page 206: ...Drive module with options 0B051 H356 0H371 206 Dimension drawings...
Page 207: ...Configuration with option H381 3AXD50000323210 Dimension drawings 207...
Page 208: ...LCL filter module 208 Dimension drawings...
Page 212: ...External control unit 3AXD50000011687 212 Dimension drawings...
Page 230: ...Declaration of conformity 230 The Safe torque off function...
Page 241: ...241...
Page 246: ...246...