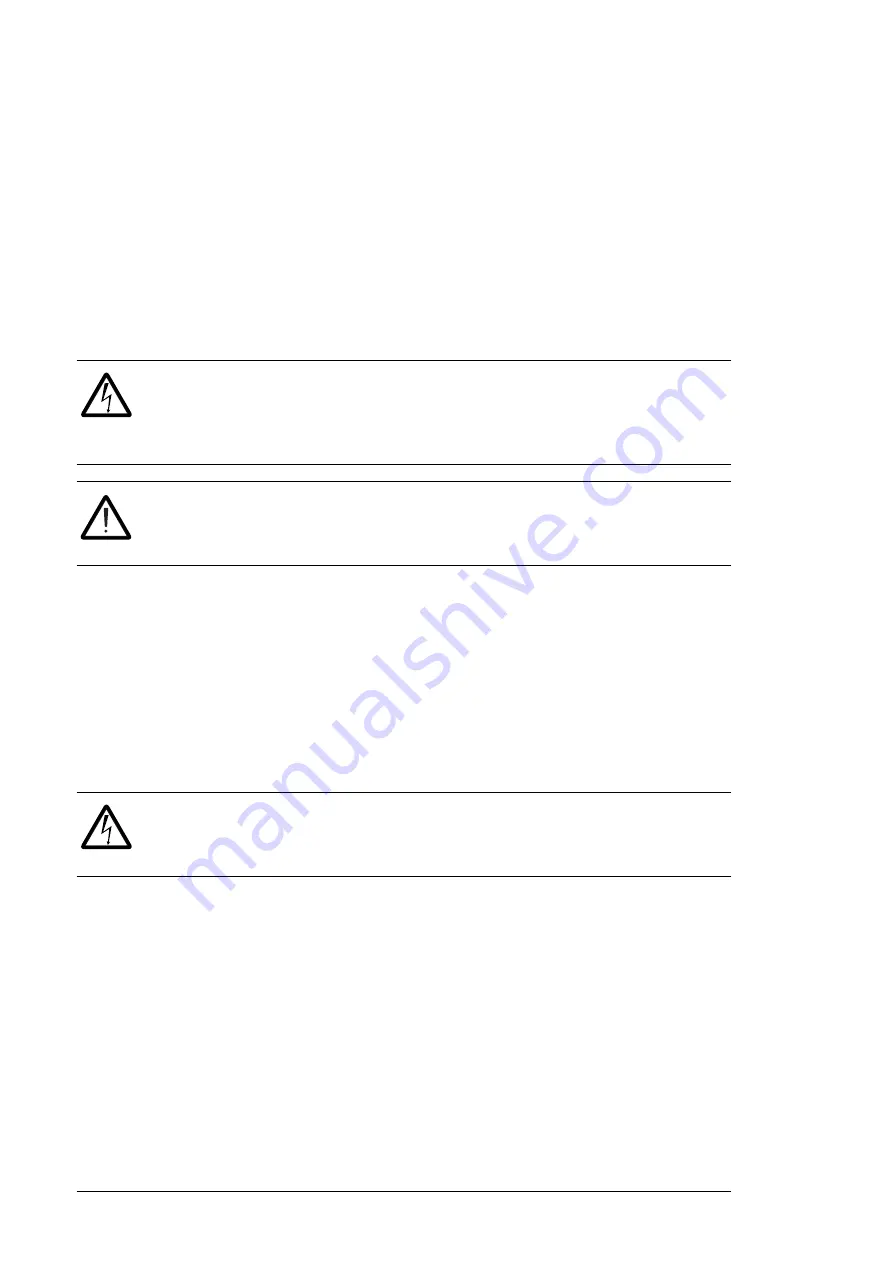
Implementing the Safe torque off function
See chapter
The Safe torque off function (page 189)
Implementing the Power-loss ride-through
Implement the power-loss ride-through function as follows:
•
Check that the power-loss ride-through function of the inverter unit is enabled with
parameter
30.31 Undervoltage control
in the ACS880 primary control program.
•
Make sure that the control of the main contactor/breaker either keeps the contactor
closed over the short power break, or closes it after the break automatically.
WARNING!
Make sure that the automatic re-connection of the input power does not cause
any danger. If you are in doubt, do not implement the Power-loss ride-through
function.
WARNING!
Make sure that the flying restart of the motor will not cause any danger. If you are
in doubt, do not implement the Power-loss ride-through function.
Implementing a bypass connection
If bypassing is required, employ mechanically or electrically interlocked contactors between
the motor and the drive and between the motor and the power line. Make sure with
interlocking that the contactors cannot be closed simultaneously. The installation must be
clearly marked as defined in IEC/EN 61800-5-1, subclause 6.5.3, for example, “THIS
MACHINE STARTS AUTOMATICALLY”.
Bypass connection is available as a factory-installed option for certain cabinet-built drive
types. Consult ABB for more information.
WARNING!
Never connect the drive output to the power line. The connection may damage
the drive.
Supplying power for the auxiliary circuits
The customer/installer must provide the auxiliary voltage from an external supply to the
drive. For details, see the circuit diagrams delivered with the drive.
The following options are to be supplied from external power sources:
•
+G300/+G301: Cabinet heaters and/or lighting (230 or 115 V AC; external fuse: 16 A gG)
•
+G313: Power supply connection (230 V AC; external fuse 16 A gG) for a motor space
heater output.
Using power factor compensation capacitors with the drive
Power factor compensation is not needed with AC drives. However, if a drive is to be
connected in a system with compensation capacitors installed, note the following restrictions.
78 Guidelines for planning the electrical installation
Summary of Contents for ACS880-07CLC
Page 1: ...ABB industrial drives Hardware manual ACS880 07CLC drives ...
Page 2: ......
Page 4: ......
Page 64: ...64 ...
Page 82: ...82 ...
Page 91: ...PE PE 10 13 12 22 Electrical installation 91 ...
Page 122: ...122 ...
Page 124: ...124 ...
Page 132: ...5 4 11 7 6 8 132 Maintenance ...
Page 133: ...14 15 16 12 13 17 Maintenance 133 ...
Page 141: ...5 Set the real time clock Maintenance 141 ...
Page 142: ...142 ...
Page 150: ...150 ...
Page 176: ...ACS880 07CLC 0390A 7 C121 marine construction 176 Dimensions ...
Page 177: ...ACS880 07CLC 1310A 7 Dimensions 177 ...
Page 178: ...ACS880 07CLC 2180A 7 C121 marine construction 178 Dimensions ...
Page 179: ...ACS880 07CLC 3260A 7 C121 marine construction Dimensions 179 ...
Page 181: ... 2 D8D Dimensions 181 ...
Page 182: ... 3 D8D 182 Dimensions ...
Page 183: ... 4 D8D Dimensions 183 ...
Page 185: ...Inverter module cubicle with two R8i modules bottom cable exit Dimensions 185 ...
Page 186: ...Inverter module cubicle with three R8i modules bottom cable exit 186 Dimensions ...
Page 187: ...Brake chopper cubicle D150 Dimensions 187 ...
Page 188: ...188 ...
Page 202: ...202 ...
Page 211: ......
Page 212: ......
Page 214: ...Contact us www abb com drives 3AXD50000131457 Rev A EN EFFECTIVE 2018 03 09 3AXD50000131457A ...