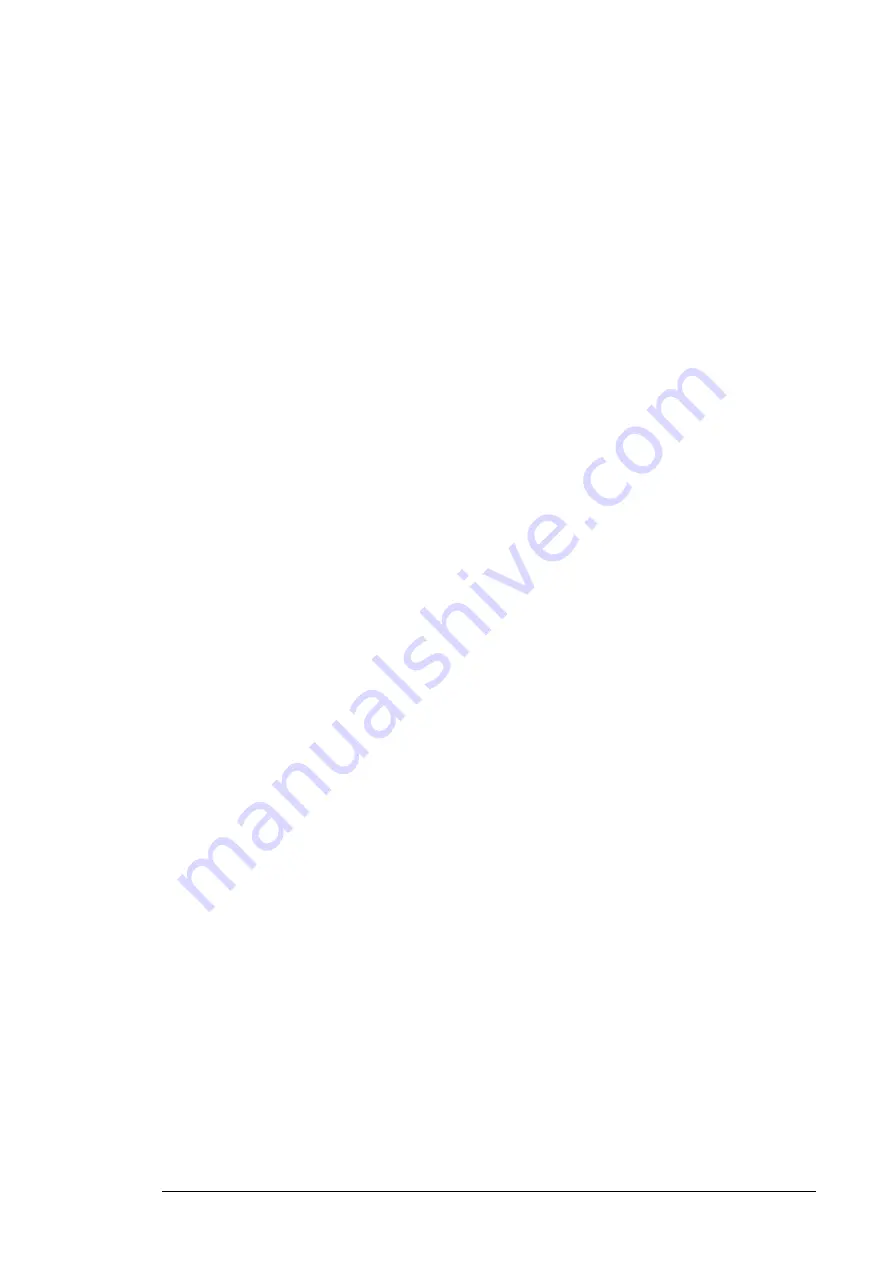
STO circuit are detected by the proof test. To perform the proof test, do the
.
Note:
See also the Recommendation of Use CNB/M/11.050 (published by the European
co-ordination of Notified Bodies) concerning dual-channel safety-related systems with
electromechanical outputs:
•
When the safety integrity requirement for the safety function is SIL 3 or PL e (cat. 3 or
4), the proof test for the function must be performed at least every month.
•
When the safety integrity requirement for the safety function is SIL 2 (HFT = 1) or PL d
(cat. 3), the proof test for the function must be performed at least every 12 months.
The STO function of the drive does not contain any electromechanical components.
In addition to proof testing, it is a good practice to check the operation of the function when
other maintenance procedures are carried out on the machinery.
Include the Safe torque off operation test described above in the routine maintenance
program of the machinery that the inverter runs.
If any wiring or component change is needed after start up, or the parameters are restored,
follow the test given in section
Acceptance test procedure (page 196)
Use only ABB approved spare parts.
Record all maintenance and proof test activities in the machine logbook.
■
Competence
The maintenance and proof test activities of the safety function must be carried out by a
competent person with adequate expertise and knowledge of the safety function as well as
functional safety, as required by IEC 61508-1 clause 6.
Fault tracing
The indications given during the normal operation of the Safe torque off function are selected
by inverter control program parameter
31.22
.
The diagnostics of the Safe torque off function cross-compare the status of the two STO
channels. In case the channels are not in the same state, a fault reaction function is
performed and the inverter trips on an “STO hardware failure” fault. An attempt to use the
STO in a non-redundant manner, for example activating only one channel, will trigger the
same reaction.
See the firmware manual of the inverter control program for the indications generated by
the inverter, and for details on directing fault and warning indications to an output on the
control unit for external diagnostics.
Any failures of the Safe torque off function must be reported to ABB.
The Safe torque off function 199
Summary of Contents for ACS880-07CLC
Page 1: ...ABB industrial drives Hardware manual ACS880 07CLC drives ...
Page 2: ......
Page 4: ......
Page 64: ...64 ...
Page 82: ...82 ...
Page 91: ...PE PE 10 13 12 22 Electrical installation 91 ...
Page 122: ...122 ...
Page 124: ...124 ...
Page 132: ...5 4 11 7 6 8 132 Maintenance ...
Page 133: ...14 15 16 12 13 17 Maintenance 133 ...
Page 141: ...5 Set the real time clock Maintenance 141 ...
Page 142: ...142 ...
Page 150: ...150 ...
Page 176: ...ACS880 07CLC 0390A 7 C121 marine construction 176 Dimensions ...
Page 177: ...ACS880 07CLC 1310A 7 Dimensions 177 ...
Page 178: ...ACS880 07CLC 2180A 7 C121 marine construction 178 Dimensions ...
Page 179: ...ACS880 07CLC 3260A 7 C121 marine construction Dimensions 179 ...
Page 181: ... 2 D8D Dimensions 181 ...
Page 182: ... 3 D8D 182 Dimensions ...
Page 183: ... 4 D8D Dimensions 183 ...
Page 185: ...Inverter module cubicle with two R8i modules bottom cable exit Dimensions 185 ...
Page 186: ...Inverter module cubicle with three R8i modules bottom cable exit 186 Dimensions ...
Page 187: ...Brake chopper cubicle D150 Dimensions 187 ...
Page 188: ...188 ...
Page 202: ...202 ...
Page 211: ......
Page 212: ......
Page 214: ...Contact us www abb com drives 3AXD50000131457 Rev A EN EFFECTIVE 2018 03 09 3AXD50000131457A ...