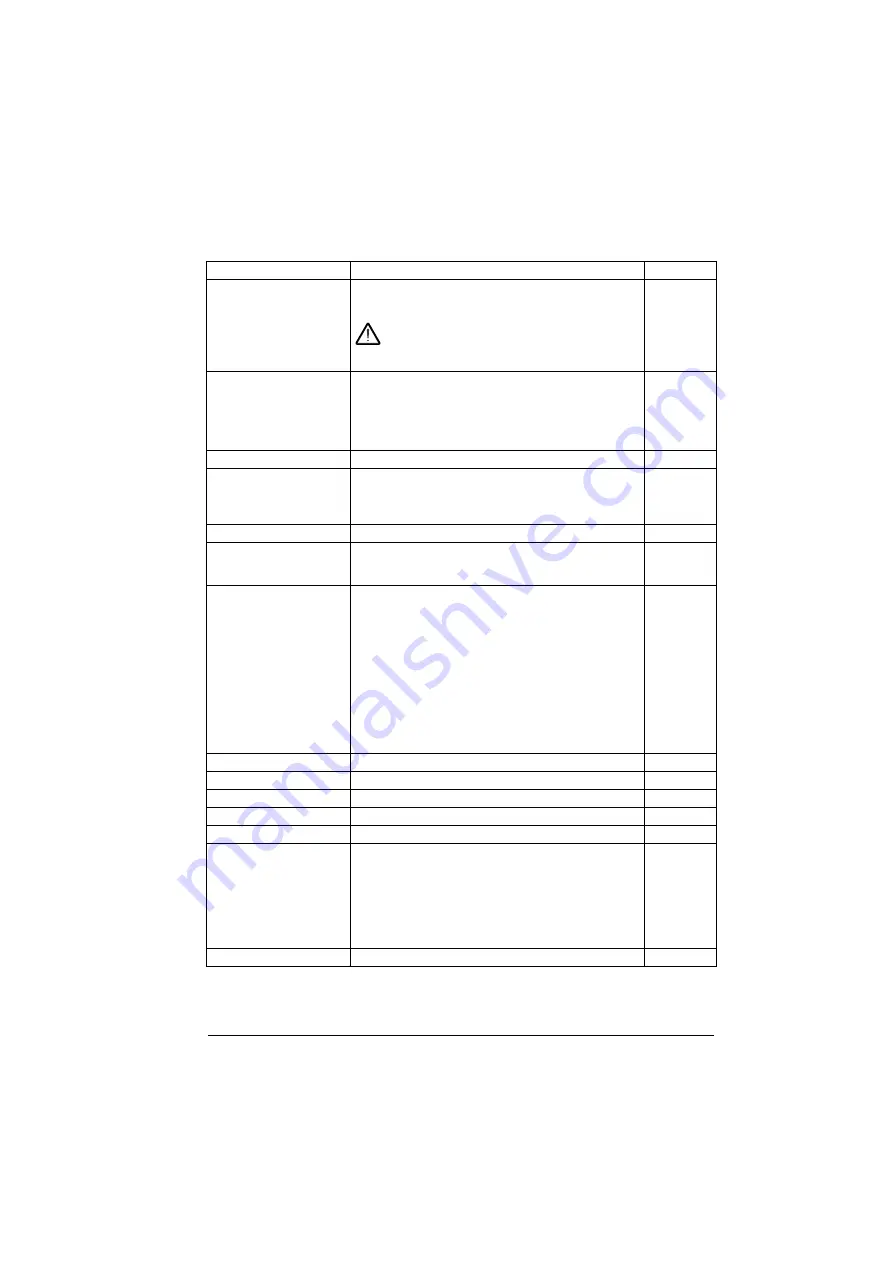
Parameters 289
Full
Maximum braking power. Almost all available current is used
to convert the mechanical braking energy to thermal energy
in the motor.
WARNING!
Using full flux braking heats up the motor
especially in cyclic operation. Make sure that the
motor can withstand this if you have a cyclic
application.
2
This parameter can be used to improve the control dynamics
of a synchronous reluctance motor or a salient permanent
magnet synchronous motor.
As a rule of thumb, define a level to which the output torque
must rise with minimum delay. This will increase the motor
current and improve the torque response at low speeds.
0.0%
0.0 … 1600.0%
Optimizer torque limit.
10 = 1%
An optimization setting for balancing between control
performance and motor noise level.
Note:
This is an expert level parameter and should not be
adjusted without appropriate skill
Normal
Control performance optimized for long motor cables.
0
Low noise
Minimizes motor noise.
Note:
This setting requires derating. Refer to the rating data
in the
Hardware manual
.
1
Enables the anti-cogging function: a high-frequency
alternating signal is injected to the motor in the low speed
region to improve the stability of torque control. This removes
the “cogging” that can sometimes be seen as the rotor passes
the motor magnetic poles. Anti-cogging can be enabled with
different amplitude levels.
Notes:
• This is an expert level parameter and should not be
adjusted without appropriate skill.
• Use as low a level as possible that gives satisfactory
performance.
• Signal injection cannot be applied to asynchronous
motors.
Disabled
Anti-cogging disabled.
0
Enabled (5%)
Anti-cogging enabled with amplitude level of 5%.
Enabled (10%)
Anti-cogging enabled with amplitude level of 10%.
2
Enabled (15%)
Anti-cogging enabled with amplitude level of 15%.
3
Enabled (20%)
Anti-cogging enabled with amplitude level of 20%.
4
Rotor time constant tuning.
This parameter can be used to improve torque accuracy in
closed-loop control of an induction motor. Normally, the motor
identification run provides sufficient torque accuracy, but
manual fine-tuning can be applied in exceptionally
demanding applications to achieve optimal performance.
Note:
This is an expert level parameter and should not be
adjusted without appropriate skill.
100%
25…400%
Rotor time constant tuning.
1 = 1%
No.
Name/Value
Description
Def/FbEq16
Summary of Contents for ACQ580
Page 1: ...ABB drives for water Firmware manual ACQ580 pump control program ...
Page 4: ... 2017 ABB Oy All Rights Reserved 3AXD50000035867 Rev C EN EFFECTIVE 2017 06 21 ...
Page 30: ...26 Start up control with I O and ID run ...
Page 40: ...36 Default configuration ...
Page 304: ...300 Parameters ...
Page 340: ...336 Additional parameter data ...