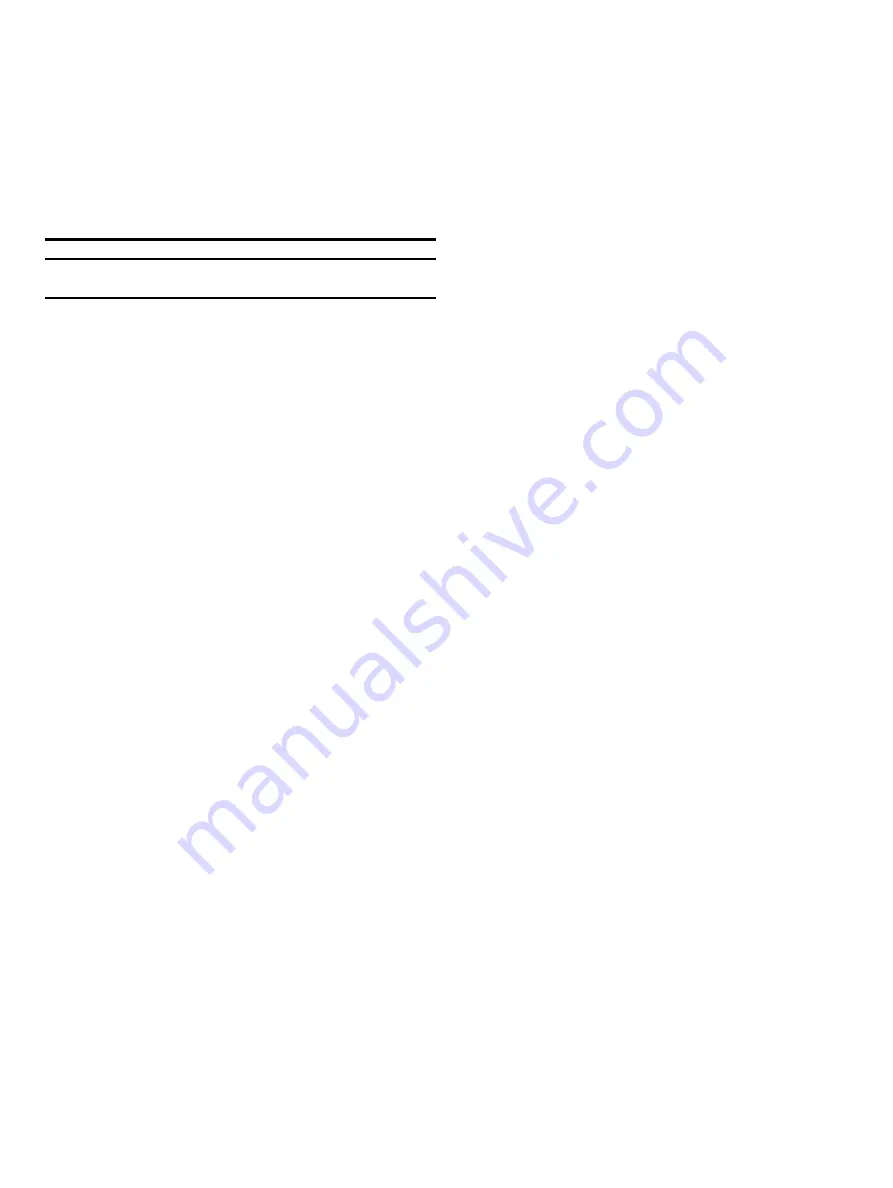
14
4 69 0 S E R I E S |
T U R B I D I T Y SEN S O R | O I/AT S 410 - EN R E V. A
6 Maintenance
The servicing schedule in Table 1 is a guide only. Because the
turbidity systems are designed for a wide range of
applications, and the nature of the sample can vary
considerably, it might be necessary to change the schedule to
apply to the particular installation and sample conditions.
Task
Recommended frequency
Wiper blade replacement
Quarterly
LED light source (ISO 7027) replacement kit
Every 5 years
Table 1 Suggested maintenance schedule
Cleaning the sensors without a wiper unit
These sensors are normally used on clean water samples. Under
normal conditions, they may only require manual monthly
cleaning of the flow chamber.
However, if a high turbidity breakthrough occurs, clean the flow
chamber immediately to make sure that the readings are
accurate.
Cleaning the sensors with a wiper unit
The required automatic cleaning frequency of the flow chamber
and optical windows of the sensors can be determined only by
plant experience.
It is recommended to do checks at appropriate intervals.
7 Fault-finding
Unstable or erratic readings
There are a number of possible causes of unstable or erratic
readings. Look for air bubbles in the sample. The bubbles might
be due to degassing of the sample, caused by either a drop in
sample pressure, or a rise in temperature.
Frequent cleaning of the optical windows helps prevent the
accumulation of bubbles. If you see bubbles, it is recommended
to install the optional de-bubbler unit. Refer to
Where the noise level gradually worsens over time, this usually
indicates that solids accumulated in the flow cell. An increase in
the flow rate through the flow cell might reduce this build up.
The flow cell must be cleaned manually.
Intermittent short-term spikes in turbidity
readings
This is usually caused by bubbles that go through the light path
in the flow cell. The bubbles are a result of degassing.
Degassing is not an instantaneous process, and it is possible
that it occurs after the sample has gone through the
de-bubbler. The bubbles start to form in the sample pipework
and the flow cell. As the bubbles grow gradually, the bubbles
finally release and flow through the light path. This causes a
spike in the turbidity reading.
The analyzer can be programmed for bubble rejection to
remove short-term spikes from the readings. For optimum
operation, operate the wiper unit frequently to prevent bubbles
accumulating on the windows.