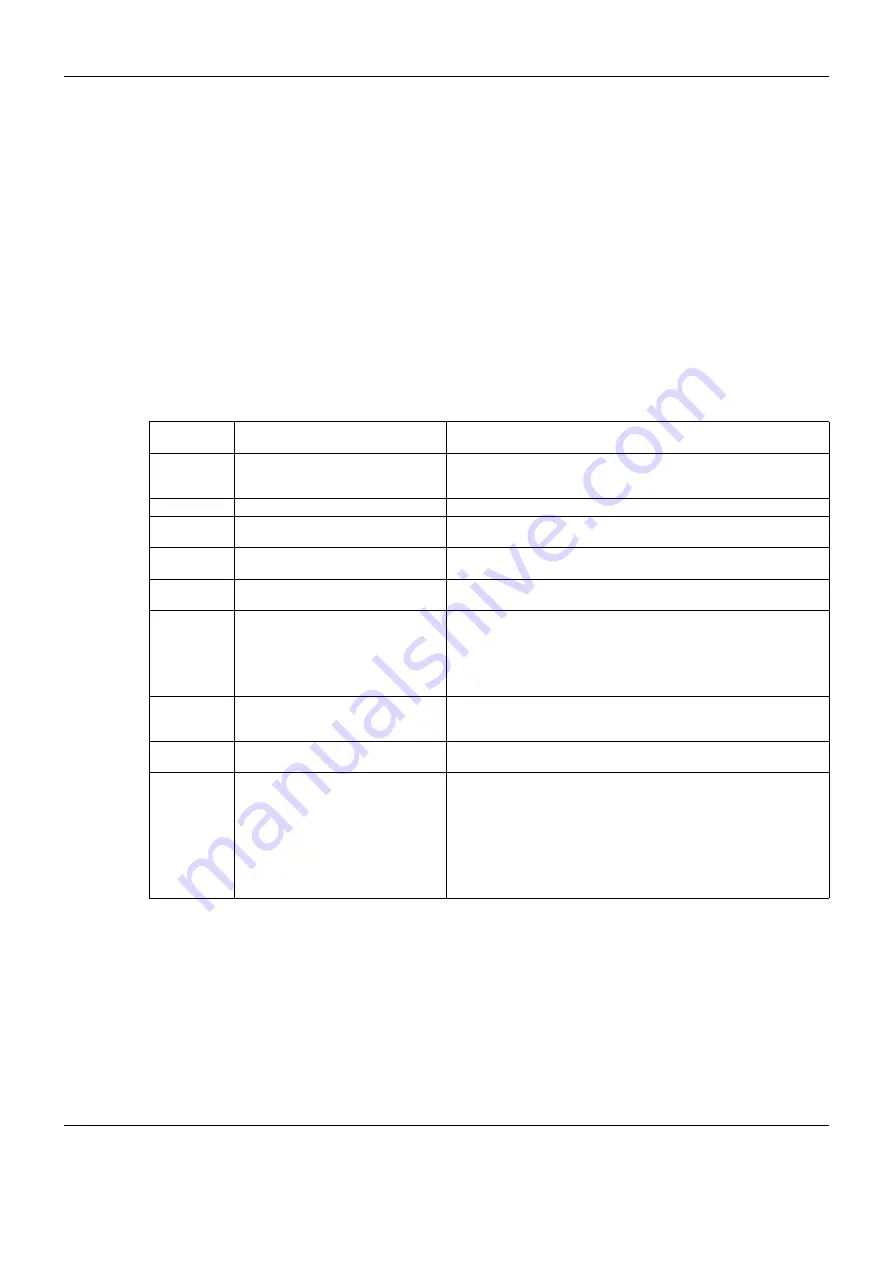
3
Pressure Transmitter Series 2000T and 265Ax, 265Gx, 265Vx, 265Dx, 265Jx, 267Cx, 269Cx
SM 265/7/9 SIL-EN
Instructions for Functional Safety
1
Field of application
Differential pressure, gauge pressure and absolute pressure measurements that shall meet the special safety
requirements according to IEC 61508/ IEC 61511-1.
The measuring unit meets the requirements regarding
• functional safety in accordance with IEC 61508/IEC 61511-1
• explosion protection (depending on the version)
• electromagnetic compatibility in accordance with EN 61326 and NAMUR recommendation NE 21.
2
User benefits
Use for
• Pressure limit monitoring
• Continuous measurement
• Easy commissioning
3
Acronyms and abbreviations
Acronym/ Ab-
breviation
Designation
Description
HFT
Hardware Fault Tolerance
The hardware fault tolerance of the device.
This is the capability of a functional unit to continue the execution of the
demanded function in case of faults or deviations.
MTBF
Mean Time Between Failures
This is the mean time period between two failures.
MTTR
Mean Time To Repair
This is the mean time period between the occurrence of a failure in a
device or system and its repair.
PFD
Probability of Failure on Demand
This is the likelihood of dangerous safety function failures occurring on
demand.
PFD
av
Average Probability of Failure on
Demand
This is the average likelihood of dangerous safety function failures
occurring on demand.
SIL
Safety Integrity Level
Safety Integrity Level
The international standard IEC 61508 specifies four discrete Safety
Integrity Levels (SIL 1 to SIL 4). Each level corresponds to a specific
probability range regarding the failure of a safety function. The higher
the Safety Integrity Level of the safety-related systems, the lower the
likelihood of non-execution of the demanded safety functions.
SFF
Safe Failure Fraction
The fraction of non-hazardous failures, i.e. the fraction of failures without
the potential to set the safety-related system to a dangerous or
impermissible state.
TI
Test interval between life testing of
the safety function
Time interval between the functional tests of the safety function.
XooY
"X out of Y" Voting (e.g. 2oo3)
Classification and description of the safety-related system regarding
redundancy and the selection procedure used.
"Y“ indicates how often the safety function is carried out (redundancy).
"X“ determines how many channels must work properly.
Example (pressure measurement): 1oo2 architecture. When one out of
two pressure sensors reaches a defined limit value, a safety-related
system decides, that the pressure limit has to be considered as
exceeded. In a system with a 1oo1 architecture only one pressure
sensor exists.