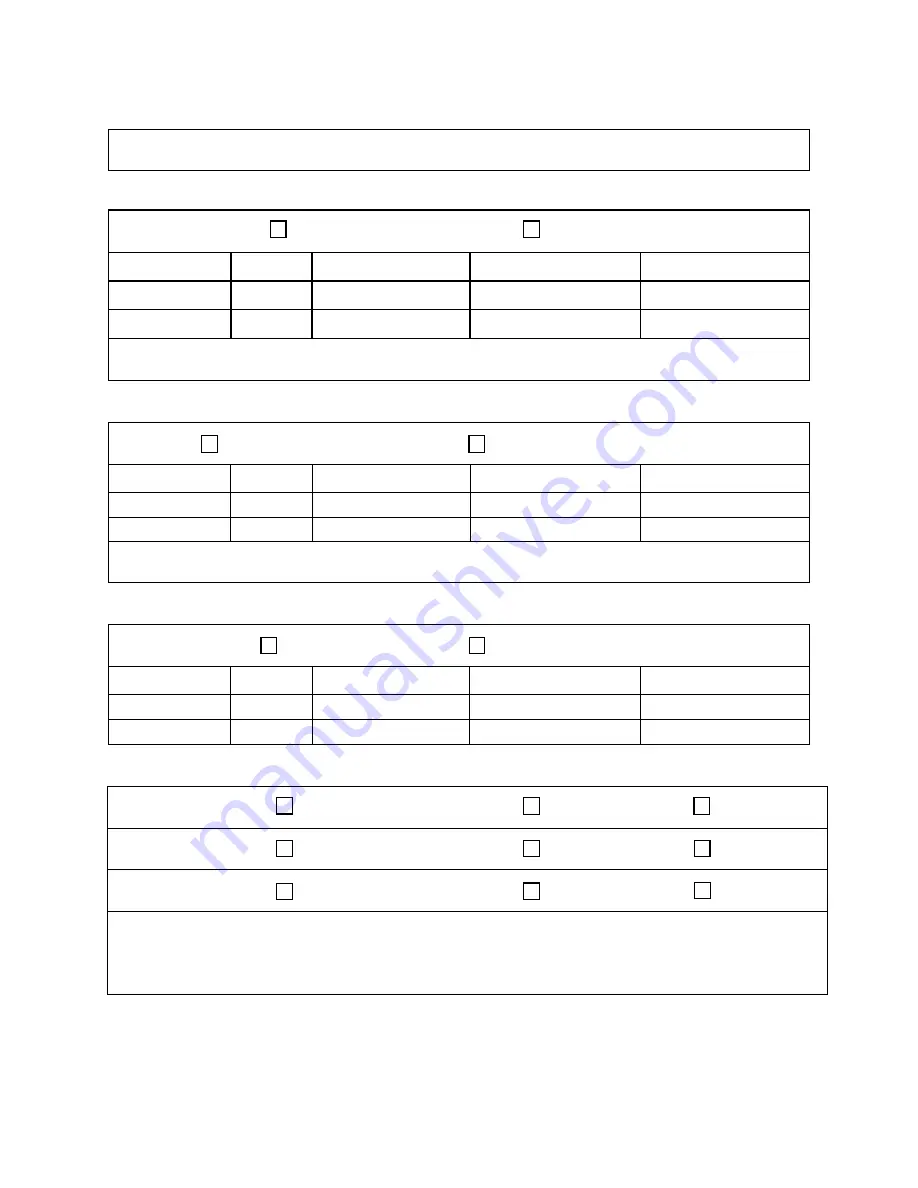
78
Ambient Temperature
Ambient Dry Bulb Temperature ________°F
Ambient Wet Bulb Temperature ________°F
Supply Fan Assembly
Alignment
Check Rotation
Nameplate Amps________
Number
hp
L1
L2
L3
1
2
VFD Frequency________________
VAV Controls_________________
Power Exhaust Fan Assembly
Alignment
Check Rotation
Nameplate Amps________
Number
hp
L1
L2
L3
1
2
VFD Frequency________________
VAV Controls_________________
Energy Recovery Wheel Assembly
Wheels Spin Freely
Check Rotation
FLA ________
Number
hp
L1
L2
L3
1
2
Dampers
OA Operation Check
Damper Wiring Check
Gears Check
RA Operation Check
Damper Wiring Check
Gears Check
EA Operation Check
Damper Wiring Check
Gears Check
Damper Actuator Type:__________________________________________________________
Economizer Changeover Type and Operation:_______________________________________