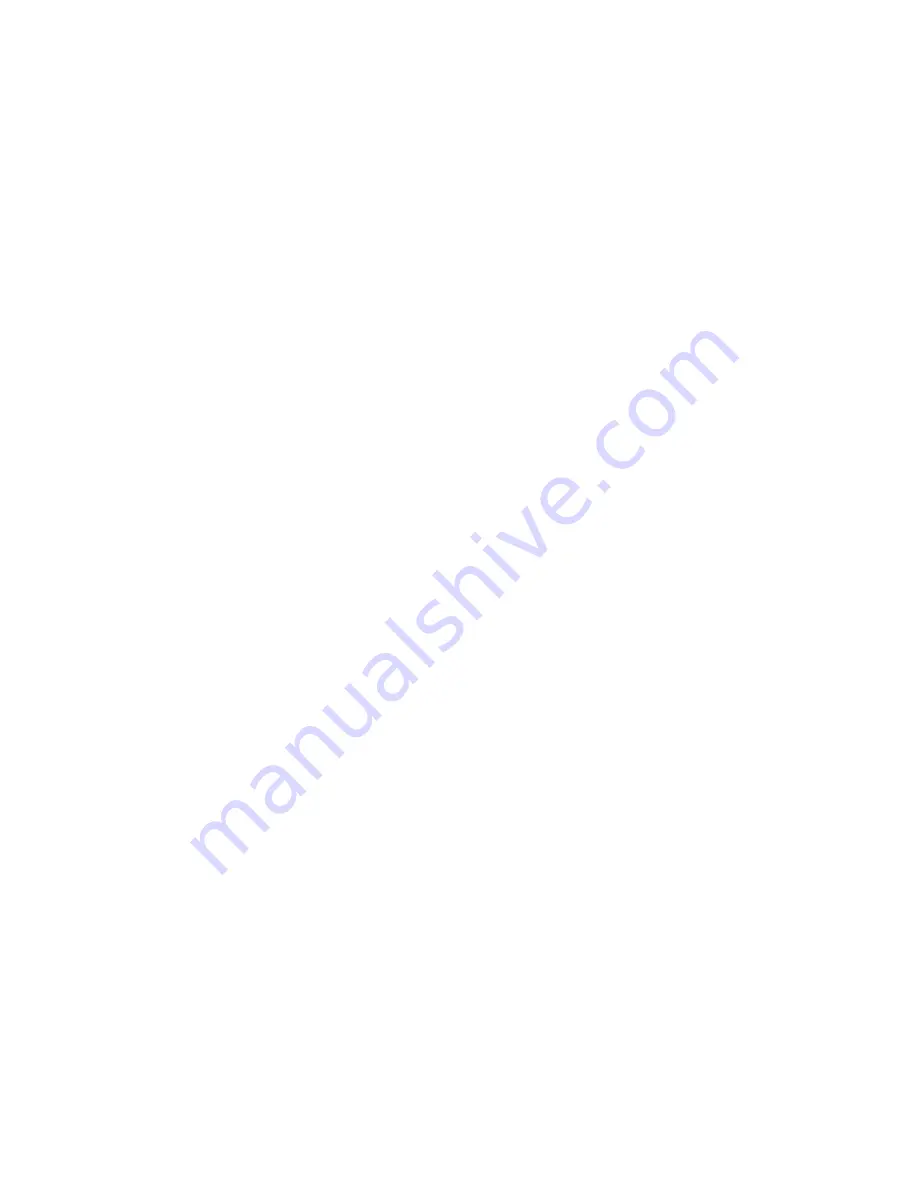
5
GAS HEATING SYSTEM
The heating section is for use with natural gas supply
pressure of 6" to 10.5" Water Column. The unit may also
utilize propane gas with a supply pressure to the valve
of 11" to 12" Water Column. The rating plate on the
furnace must be inspected to make sure the unit is
stamped for proper gas. A 1/8" pressure tap should be
field supplied by the installer in the piping just ahead of
the gas valve. The pressure tap on the outlet end of the
gas valve can be checked to verify manifold pressure of
3.2" to 3.5" for natural gas.
Combustion air is supplied by a centrifugal blower
which draws in outside air through a protected opening.
This induced draft blower introduces the air to the
burner tubes which assures even primary and secondary
air flow.
All heating system and related safety controls are 100%
tested on each unit prior to shipment.
INSTALLATION IS TO BE ADJUSTED
TO OBTAIN AN AIR TEMPERATURE RISE
WITHIN THE RANGE SPECIFIED ON THE
RATING PLATE.
The units are equipped with a direct spark ignition
system which proves the burner operation during each
call for heat. Power to the ignition control is 24 Vac to
reduce hazards. Burner ignition is by a high intensity
spark.
When heat is called for, the cooling system is inoperable
except for the indoor blower motor. Heating is accom-
plished by firing gas into the heat exchanger assembly.
ELECTRIC HEATING SYSTEM
Heating is accomplished by passing electrical current
through a specified amount of resistance heaters which
produce the required heat. The indoor blower motor
energizes at the same time as the heaters.
STEAM OR HOT WATER HEATING SYSTEM
Heating is accomplished by passing steam or hot water
through the steam or hot water coil assembly.
COOLING SECTION • DX
All direct expansion refrigeration systems are factory
assembled, charged with refrigerant, tested and oper-
ated. On all units 8 ton and larger the refrigerant system
includes multiple circuit evaporator and condenser coils
providing two or more stages of cooling. These systems
include liquid line filter driers, expansion valves and
fully hermetic compressors. Compressors are equipped
with a positive pressure forced lubrication system. The
air cooled condenser coil(s) are constructed of copper
tubes and mechanically bonded aluminum fins and air is
pulled through by propeller fans. The evaporator coil is
draw through type constructed of copper tubes and
mechanically bonded aluminum fins.
The refrigeration section of these appliances has been
found acceptable with applicable provisions of "ANSI /
UL 1995" and current "C.S.A. Standard C22.2" by E.T.L.
NOTE: Crankcase Heater Operation
Some units are equipped with a compressor crankcase
heater, which should be energized at least 24 hours prior
to setting the thermostat for cooling operation.
COOLING SECTION • CHILLED WATER
or NON-COMPRESSORIZED UNIT
Chilled water or non-compressorized units have factory
installed coils. Systems are provided with internal
header connections for field piping.
Coils are constructed of copper tubes and mechanically
bonded aluminum fins.
HEATING & COOLING SYSTEMS
NORMAL OPERATION
HEATING
Set the thermostat system switch to "HEAT".
Set the thermostat fan switch to "AUTO" or "ON".
Set the thermostat temperature at the desired point.
COOLING
Set the thermostat system switch to "COOL".
Set the thermostat fan switch to "AUTO" or "ON".
Set the thermostat temperature at the desired point.
AIR CIRCULATION
Set the thermostat system switch to "OFF".
Set the thermostat fan switch to "ON".
Do not change temperature setting.
With these settings, the air circulating blower will run
continuously but the air will not be heated or cooled.
SYSTEM OFF
Set the thermostat system switch to "OFF".
Set the thermostat fan switch to "AUTO".
Do not change temperature setting.
With these settings, the system is shut down, with the
exception of the control system power (24 Vac), and the
crankcase heater of the compressor (approx. 60W).
DO NOT TURN OFF THE MAIN POWER SWITCH.
NIGHT AND VACANT WEEKEND OPERATION
To reduce the operation time during low load periods,
it is recommended that the temperature setting be
increased five degrees during these periods of the cooling
season, and decreased ten degrees during the heating
season.