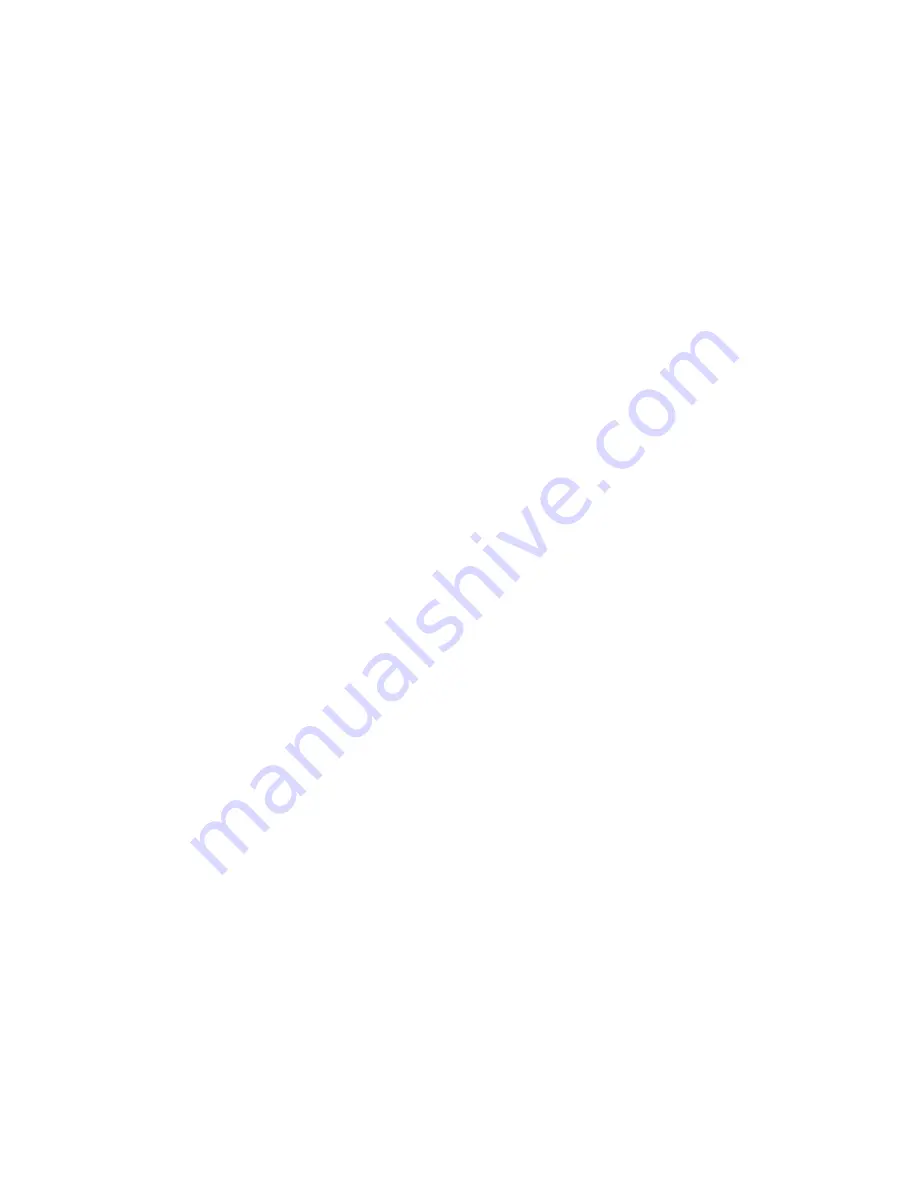
22
The pump is installed after the suction guide,
and before a combination valve (Flo-Trex).
This combination valve acts as an isolation
valve, check valve, and flow balancing valve.
The
evaporator
is
placed
after
the
combination valve in the water circuit, with a
flow switch installed at its inlet and outlet.
This flow switch closes when the velocity is
above 0.7 feet per second. The closing flow
switch signals the control system to indicate
flow through the heat exchanger and allow
cooling to activate as required to maintain the
setpoint. The water exiting the chiller
evaporator leaves the unit through the water
out connection.
Chiller Primary/Secondary Pumping
Primary/secondary pumping option provides
variable flow to the system. It consists of a
constant flow pump for the chiller heat
exchanger and a variable flow pump for the
building. The controls package senses
differential pressure across the pump with
pressure transducers installed at the suction
and discharge, and varies the speed of the
pump using a VFD in order to maintain a
given differential pressure across the pump.
The primary/secondary pumping package is
essentially composed of two piping loops
coupled together. The primary loop has a
constant flow rate in order to keep the chiller
heat exchanger from freezing, and the
secondary, variable flow loop, provides water
to the building. The two loops are coupled via
a water line that compensates for excess flow
in either loop. As the flow in the secondary
loop decreases below the flow in the primary
loop, excess flow bypasses the building loop
and circulates through the bypass water line.
On the other hand, as the flow in the
secondary loop increases above the flow in
the primary loop, excess flow bypasses the
chiller and circulates through the bypass
water line.
The secondary pump has its own suction
guide, combination valve, and isolation
valve, similar to the primary pump, with the
addition of an air separator to remove any air
that is entrapped in the water.
Condensing Boilers
AAON LZ chillers are available with factory
installed condensing boilers. All boiler
systems will include either fixed or variable
speed building pumps. All boiler building
pumps will be supplied with a suction guide
with a strainer and triple duty valve. The
suction guide contains both an operational
strainer and a startup strainer. The startup
strainer should be removed 24 hours after
startup. The triple duty valve functions as an
isolation valve, check valve, and flow
balancing valve.
The condensing boilers will be a water tube
design or a fire tube design. In a water-tube
boiler, the water flows through tubes with the
combustion products heating from the
outside. These boilers require a constant
water flow and will be provided with a
primary pump for each heat exchanger.
Some boilers have two heat exchangers and
will have two primary pumps. The primary
pump is controlled by the boiler and will only
come on when it has a call for heat. Water-
tube boilers are provided with flow switches,
which must make before the boiler can
operate.
In fire-tube boilers water flows through a
tank, with the combustion products inside
tubes. These boilers are capable of
significant water flow turn-down and do not
require individual primary pumps. A control
valve, operate by the boiler controls, is
provided with each boiler. A water flow
switch is not required with fire-tube boilers.
A low-level cutoff switch is used which will
prevent the boiler from operating when there
is not a sufficient water level present. Upon
Summary of Contents for LZ Series
Page 2: ......
Page 27: ...27 Figure 6 Concrete Pad Mounting with Dimensions Figure 7 LZ Base ...
Page 36: ...36 Figure 17 Typical Flue Vent Piping ...
Page 83: ...83 ...
Page 84: ...84 ...
Page 95: ...95 Flo Trex Cross Section ...