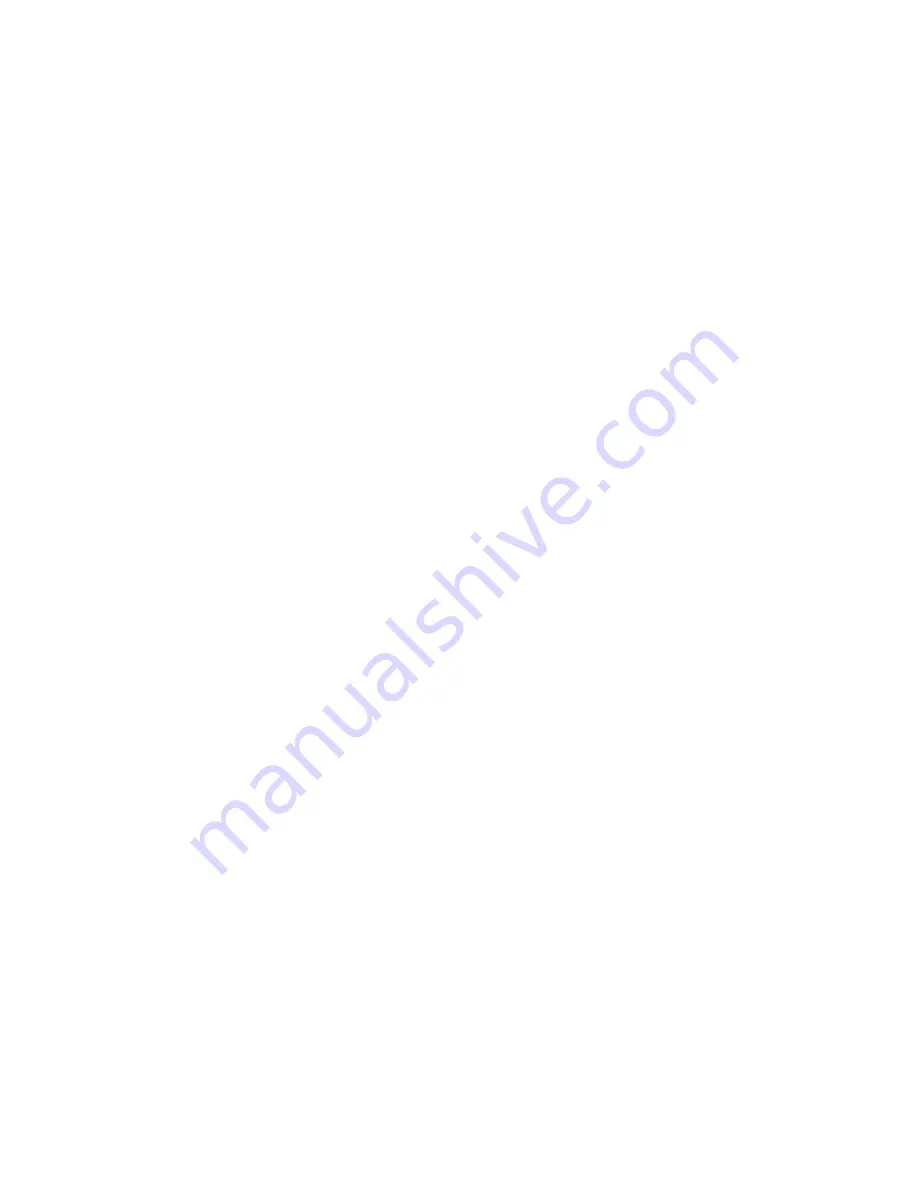
39
Dual Pump Specific Information
Dual Pump Flapper Valve Operating
Instructions
This unit is fitted with internal valves to allow
isolation of one pump for service and to
automatically prevent recirculation of the
flow when only one pump is running.
Procedure for Parallel or Stand-By
Pumping:
Discharge and suction valve stems should be
locked in the center position. This is
indicated by both locking handles in the
vertical position and the center pin of the
locking arms (4) locked by the handles. This
procedure allows the discharge flapper valves
to pivot freely and locks the suction valve
firmly in the center position.
Procedure for Isolation of One Side:
1.
Stop the pump to be serviced.
2.
Close and lock the suction and discharge
valves: as per instructions below.
3.
Ensure seal flush line interconnection
valve is closed and drain the isolated casing.
4.
Service isolated pump as required.
Procedure for Starting the Pump after
Servicing:
1.
Ensure serviced pump is fully re-
assembled including all seal flush lines and
drain plugs.
2.
Fill the dry casing with system fluid by
opening the seal flush line interconnecting
valve and the air vent fitting.
3.
Allow the pressure to equalize in the two
casings, if necessary, by opening seal flush
line interconnected valve.
4.
Unlock the discharge valve as per
instructions below.
5.
Unlock the suction valve as per
instructions below.
NOTE:
Keep hands and tools away from
locked suction valve arm, as the differential
pressure may cause the arm to rotate quickly
with force when unlocked.
6.
Close the seal flush line interconnect valve
and restart pump.
Valve Operation
Refer to the valve illustrations on the
following pages.
Discharge Valve
This valve performs the dual function of
automatically sealing the discharge of the
inactive pump when one pump is running and
can manually be closed and locked to isolate
one pump for service.
Automatic Flapper Operation
In the flapper mode the two halves of the
discharge
valve
are
free
to
pivot
independently under normal
operating
conditions. The locking handle (3) should be
secured with the set screw (11) in the vertical
position with the center pin of the locking
arm (4) trapped by the locking handle (3).
Manual Valve Locking:
The locking feature of this valve is to ensure
a positive seal (leak proof) of the discharge
port on the pump to be serviced.
Note:
Ensure the pump to be isolated is not
operating before attempting to release the
locking mechanism. Failure to do so may
result in injury to the operator and/or damage
to the pump.
Locking
1.
Loosen discharge side set screw (11) to
release the locking handle (3).
2.
Rotate the discharge side locking handle
(3) so that the handle points toward the pump
to be serviced and secure in the horizontal
position, using set screw (11). This releases
the discharge locking arm (4).
Summary of Contents for LF Series
Page 42: ...42 ...
Page 43: ...43 ...
Page 50: ...Pressure Temperature Limits Flo Trex Cross Section ...