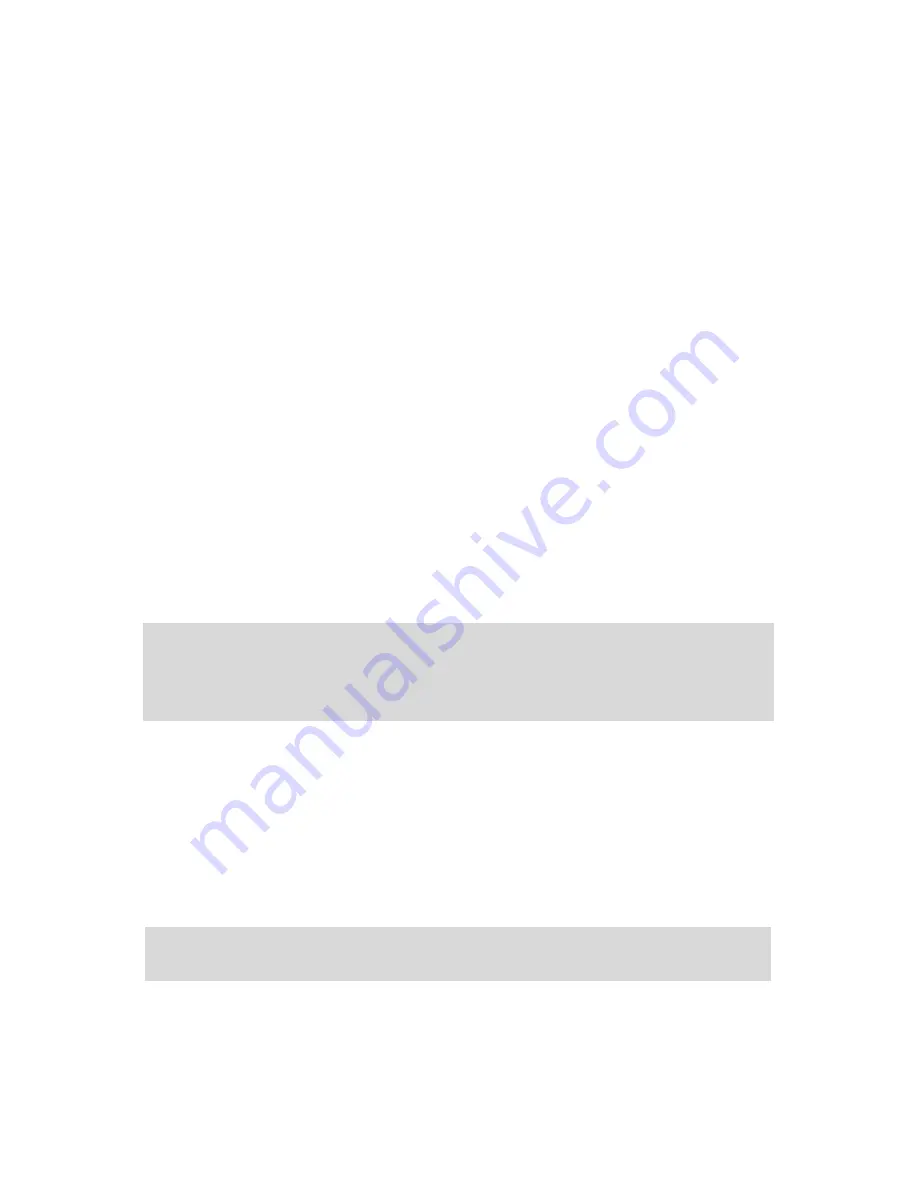
5.3
Swamping Condition
If a flow of more than 10% above the maximum flow rate of the Mass Flow Meter
is taking place, a condition known as “swamping” may occur. Readings of a
“swamped” meter cannot be assumed to be either accurate or linear. Flow must
be restored to below 110% of maximum meter range. Once flow rates are lowered
to within calibrated range, the swamping condition will end. Operation of the meter
above 110% of maximum calibrated flow may increase recovery time.
6.
MAINTENANCE
6.1
Introduction
It is important that the Mass Flow Meter/Controller is used with clean, filtered
gases only. Liquids may not be metered. Since the RTD sensor consists, in part,
of a small capillary stainless steel tube, it is prone to occlusion due to impedi-
ments or gas crystallization. Other flow passages are also easily obstructed.
Therefore, great care must be exercised to avoid the introduction of any potential
flow impediment. To protect the instrument a 50 micron (GFM17) or 60 micron
(GFM37/47) filter is built into the inlet of the flow transducer. The filter screen and
the flow paths may require occasional cleaning as described below. There is no
other recommended maintenance required. It is good practice, however, to keep
the meter away from vibration, hot or corrosive environments and excessive RF
or magnetic interference.
If periodic calibrations are required they should be performed by qualified per-
sonnel and calibrating instruments, as described in section 7. It is recommended
that units are returned to Aalborg
7
for repair service and calibration.
CAUTION: TO PROTECT SERVICING PERSONNEL IT IS MANDATORY THAT ANY
INSTRUMENT BEING SERVICED IS COMPLETELY PURGED AND NEUTRALIZED
OF TOXIC, BACTERIOLOGICALLY INFECTED, CORROSIVE OR RADIOACTIVE
CONTENTS.
6.2
Flow Path Cleaning
Before attempting any disassembly of the unit for cleaning, try inspecting the
flow paths by looking into the inlet and outlet ends of the meter for any debris that
may be clogging the flow through the meter. Remove debris as necessary. If the
flow path is not unclogged, then proceed with steps below.
Do not attempt to disassemble the sensor. If blockage of the sensor tube is not alle-
viated by flushing through with cleaning fluids, please return meter for servicing.
NOTE: DISASSEMBLY MAY COMPROMISE CURRENT CALIBRATION.
6.2.1
Restrictor Flow Element (RFE)
The Restrictor Flow Element (RFE) is a precision flow divider inside the trans-
ducer, which splits the inlet gas flow by a preset amount to the sensor and main
flow paths. The particular RFE used in a given Mass Flow Meter depends on the
gas and flow range of the instrument.
9