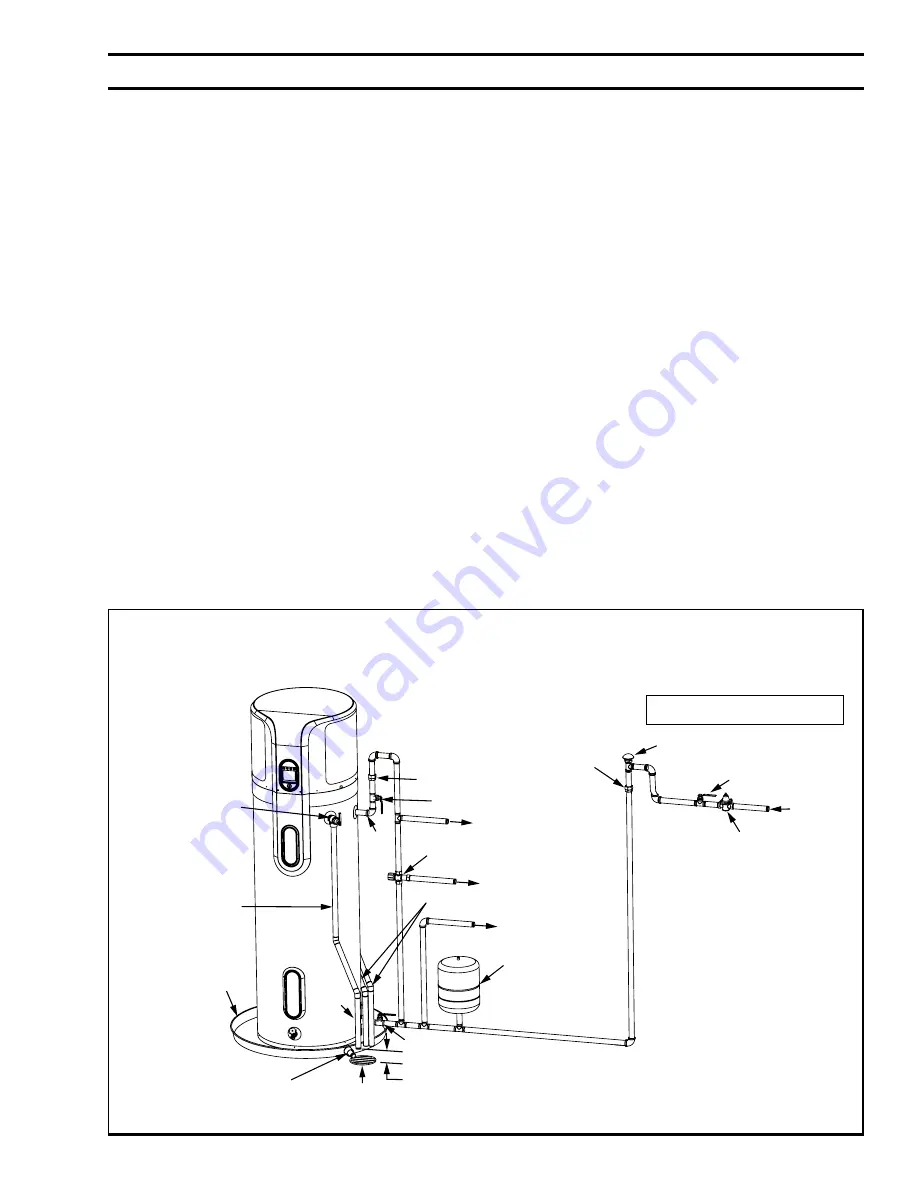
9
Water Piping System
Cold Water
Inlet Valve
Cold Water
Inlet
Pressure Reducing Valve (PRV)
should be installed where the water
supply enters the residence.
In a closed system, use a
thermal expansion tank.
See “Closed System/
Thermal Expansion”
section.
Cold Water Outlet
Shut-off Valve
(Cold)
Tempered Water to Fixtures
Untempered Water Outlet
Vacuum Relief Valve
Mixing Valve - Follow the Mixing Valve’s
Manufacturer’s Installation Instructions.
(Set to 120° F)
6” Maximum
Air Gap
Metal Drain Pan 2 1/2”
Depth Maximum and
2 Inches wider than
the water heater.
Discharge Pipe
(Do Not Cap or Plug)
Temperature and
Pressure Relief Valve
Union
Shut-off Valve (Hot)
Drain Line 3/4”
ID Minimum
Drain
Condensate Drain Lines*
Massachusetts: Install a vacuum relief in
cold water line per section 19 MGL 142.
* If an adequate drain is not available for the condensate drain lines then a condensate pump should be used. DO NOT discharge the condensate drain
lines into the metal drain pan.
Union
Hot
(Outlet)
Cold
(Inlet)
Figure 2
Piping,
fi
ttings, and valves should be installed according to
the installation drawing (Figure 2). If the indoor installation
area is subject to freezing temperatures, the water piping
must be properly insulated.
Water supply pressure should be 50-60 PSIG (.35 MPa)
and not exceed the maximum 80 PSIG (.55 MPa). If
the supply line pressure exceeds 80 PSIG (.55 MPa),
a pressure reducing valve (PRV) with a bypass should
be installed in the cold water supply line. This should
be placed on the supply to the entire house in order to
maintain equal hot and cold water pressures.
IMPORTANT:
•
Heat must not be applied to the water fittings on
the heater as they may contain nonmetallic parts. If
solder connections are used, solder the pipe to the
adapter before attaching the adapter to the hot and
cold water fittings.
•
Always use a good grade of joint compound and be
certain that all fittings are tight.
IMPORTANT:
DO NOT over apply joint compound.
Piping Installation
1. Install the water piping and fittings as shown (Figure 2).
Connect the cold water supply (3/4” NPT) to the fitting
marked “Cold”. Connect the hot water supply (3/4”
NPT) to the fitting marked “Hot”.
2. The installation of unions in both the hot and cold
water supply lines are recommended for ease of
removing the water heater for service or replacement.
3. Some local codes may require, and the manufacturer of
this water heater recommends, installing a mixing valve
or an anti-scald device in the domestic hot water line as
shown (Figure 2), or at the point of use. These valves
reduce the point-of-use temperature of the hot water
by mixing cold and hot water and are readily available.
Contact a licensed plumber or the local plumbing
authority for more information.
4. Some local codes may require, and the manufacturer
of this water heater recommends, installing a pressure
reducing valve (PRV) in the cold water inlet line where
it enters the residence as shown (Figure 2).
5. If installing the water heater in a closed water system,
install an expansion tank in the cold water line as
specified under “Closed System/Thermal Expansion”
(p.10).
6. Install a shut off valve in the cold water inlet line. It
should be located close to the water heater and be
easily accessible. Know the location of this valve and
how to shut off the water to the heater.
7. Install a discharge line from the temperature and
pressure relief valve in the opening marked “T & P
RELIEF VALVE”. See Figure 3 and the “Temperature
and Pressure Relief Valve” (p.10)
8. After piping has been properly connected to the water
heater, open the nearest hot water faucet. Then open
the cold water shut off valve and allow the tank to
completely fill with water. To purge the lines of any
excess air and sediment, keep the hot water faucet
open for three (3) minutes after a constant flow of water
is obtained. Close the faucet and check all connections
for leaks.