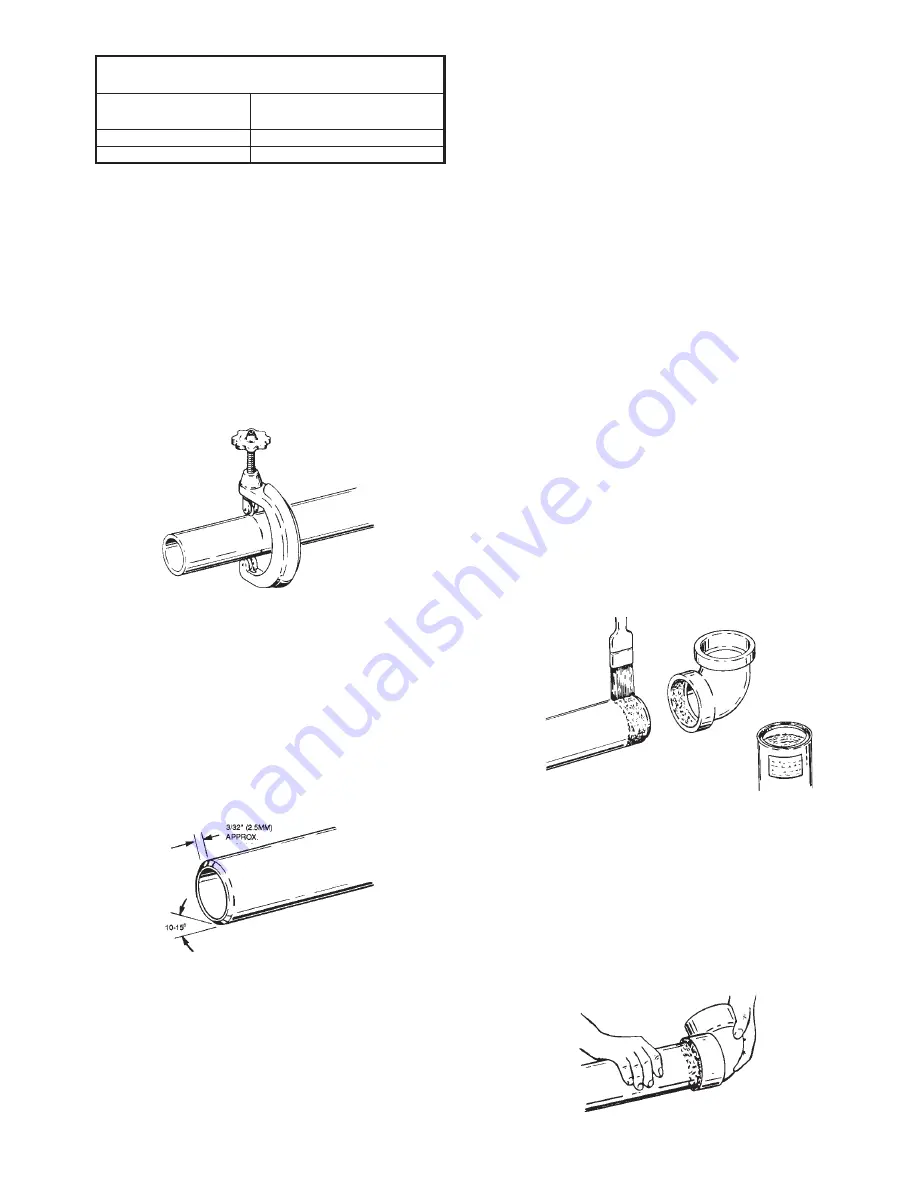
11
RECOMMENDED BRUSH* SIZE FOR PRIMER
AND CEMENT APPLICATIONS
Nominal Pipe
Size Brush Width
(IPS)
(INS.)
2
1-1/2
3
1-1/2 - 2-1/2
*USE ONLY NATURAL BRISTLE
3.
MAKING THE JOINT
A. Cutting
Pipe must be squarely cut to allow for the proper interfacing
of the pipe end and the fitting socket bottom. This can be
accomplished with a miter box saw or wheel type cutter. Wheel
type cutters are not generally recommended for larger
diameters since they tend to flare the corner of the pipe end.
If this type of cutter is used, the flare on the end must be
completely removed.
NOTE: Power saws should be specifically designed to cut plastic
pipe.
STEP A
B. Deburring
Use a knife, plastic pipe deburring tool, or file to remove burrs
from the end of small diameter pipe. Be sure to remove all
burrs from around the inside as well as the outside of the
pipe. A slight chamfer (bevel) of about 10°-15° should be
added to the end to permit easier insertion of the pipe into the
end of the fitting. Failure to chamfer the edge of the pipe may
remove cement from the fitting socket, causing the joint to
leak.
STEP B
C. Test dry fit of the joint
Tapered fitting sockets are designed so that an interfaced fit
should occur when the pipe is inserted about 1/3 to 2/3 of the
way into the socket. Occasionally, when pipe fitting
dimensions are at the tolerance extremes, it will be possible
to fully insert dry pipe to the bottom of the fitting socket. When
this happens, a sufficient quantity of cement must be applied
to the joint to fill the gap between the pipe and fitting. The gap
must be filled to obtain a strong, leak-free joint.
D. Inspection, cleaning, priming
Visually inspect the inside of the pipe and fitting sockets and
remove all dirt, grease or moisture with a clean dry rag. If
wiping fails to clean the surfaces, a chemical cleaner must
be used. Check for possible damage such as splits or cracks
and replace if necessary.
Depth-of-entry
Marking the depth of entry is a way to check if the pipe has
reached the bottom of the fitting socket in Step F. Measure
the fitting depth and mark this distance on the pipe O.D. You
may want to add several inches to the distance and make a
second mark as the primer and cement will most likely destroy
your first one.
Apply primer to the surface of the pipe and fitting socket with
a natural bristle brush (see chart on page 11). This process
softens and prepares the PVC or CPVC for the solvent
cementing step. Move quickly and without hesitation to the
cementing procedure while the surfaces are still wet with
primer.
E. Application of solvent cement
• Apply the solvent cement evenly and quickly around the
outside of the pipe at a width a little greater than the depth
of the fitting socket.
• Apply a light coat of cement evenly around the inside of the
fitting socket. Avoid puddling.
• Apply a second coat of cement to the pipe end.
NOTE: Cans of cement and primer should be closed at all times
when not in use to prevent evaporation of chemicals and
hardening of cement. They are also very flammable and should
be kept away from heat or flame.
STEP E
F. Joint assembly
Working quickly, insert the pipe into the fitting socket bottom
and give the pipe or fitting a 1/4" turn to evenly distribute the
cement. Do not continue to rotate the pipe after it has hit the
bottom of the fitting socket. A good joint will have sufficient
cement to make a bead all the way around the outside of the
fitting hub. The fitting will have a tendency to slide back while
the cement is still wet so hold the joint together for about 15
seconds.
STEP F