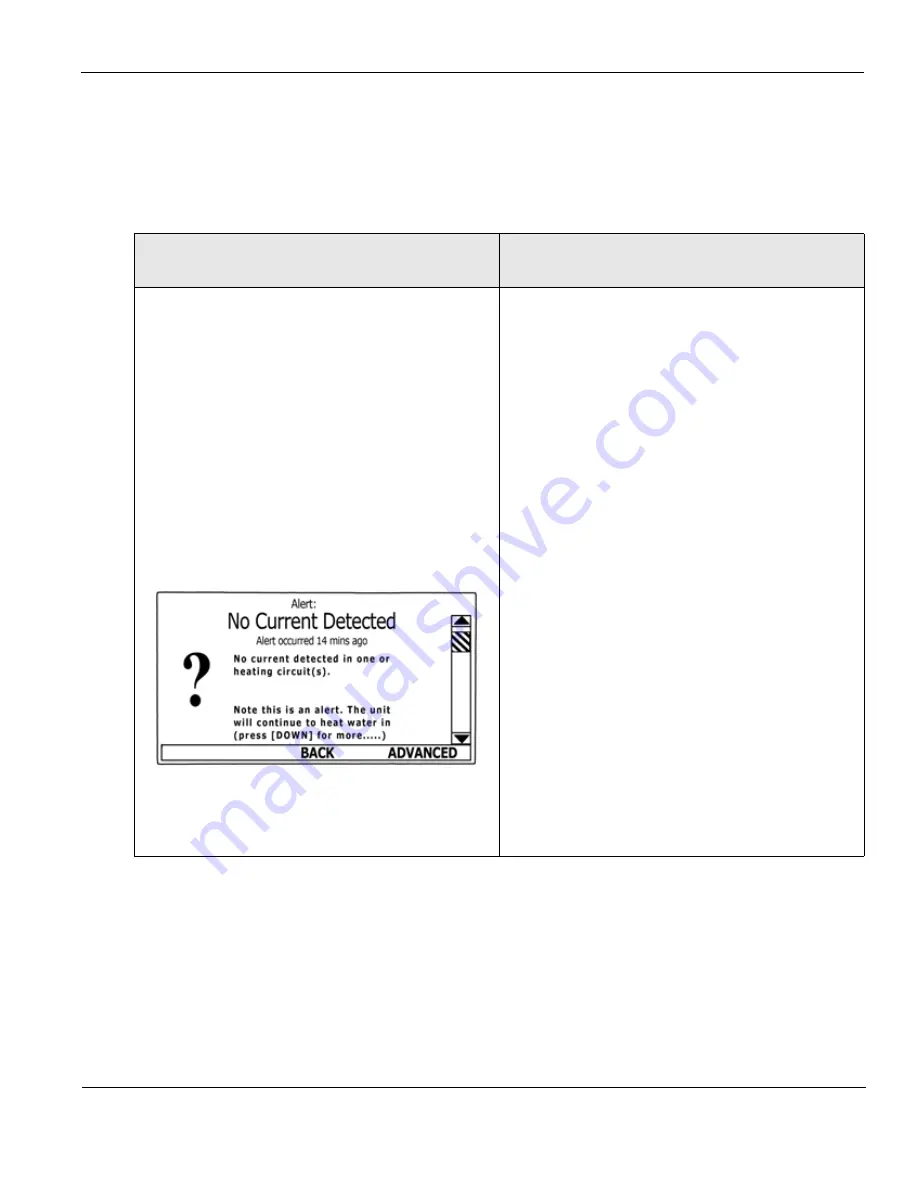
Servicing should only be performed by a Qualified Service Agent
67
TROUBLESHOOTING
FAULT AND ALERT MESSAGES
Troubleshooting procedures for the most common Fault and Alert messages are covered in
this section. In the tables that follow the first column shows the Fault or Alert message as
displayed by the UIM along with an explanation. The second column details things to check
or repair and references test procedures detailed in the Operation and Service section
(pages 10 - 47) of this manual.
DISPLAYED MESSAGE
CONDITION/INDICATES
CHECK/REPAIR
“No Current Detected”
(Alert Condition)
The control system has not detected current in one
or more heating element circuits when expected.
Possible Causes:
Power supply problem (dead leg on 3 phase supply)
Blown power circuit fuses
Defective heating element(s)
Defective contactor(s)
Plug/socket connection problems
Defective Element Sensor
Wiring connection problems
•
Ensure the power supply to the water heater
matches the listed voltage on the water heater
rating plate. Ensure there is not a dead leg of
power on 3Ø models - see pages 12 - 14.
•
Check power circuit fuses - see page 17.
•
Check heating elements see pages 20 - 26.
•
Check contactors - see pages 29 - 33.
•
Check power circuit wiring to heating elements
from Power Distribution Block, to fuse blocks, to
contactors, to heating elements - see wiring dia-
gram on water heater and Contactor Configura-
tion illustration on page 30. Correct any mis
wiring. Repair or replace damaged wiring as
necessary.
•
Check the Element Sensor J12, J13, J14 plug/
socket connections at the CCB for wear or dam-
age - see page 28. Ensure they are mating
properly and providing good contact. See CCB
illustration and socket identification on pages 42
- 44 for location.
•
Check Element Sensors - see pages 27 & 28.
Replace any Element Sensors determined to be
defective.
•
Call the toll free technical support phone num-
ber on the back cover of this manual for further
assistance if the problem has not been cor-
rected after performing the procedures outlined
here.