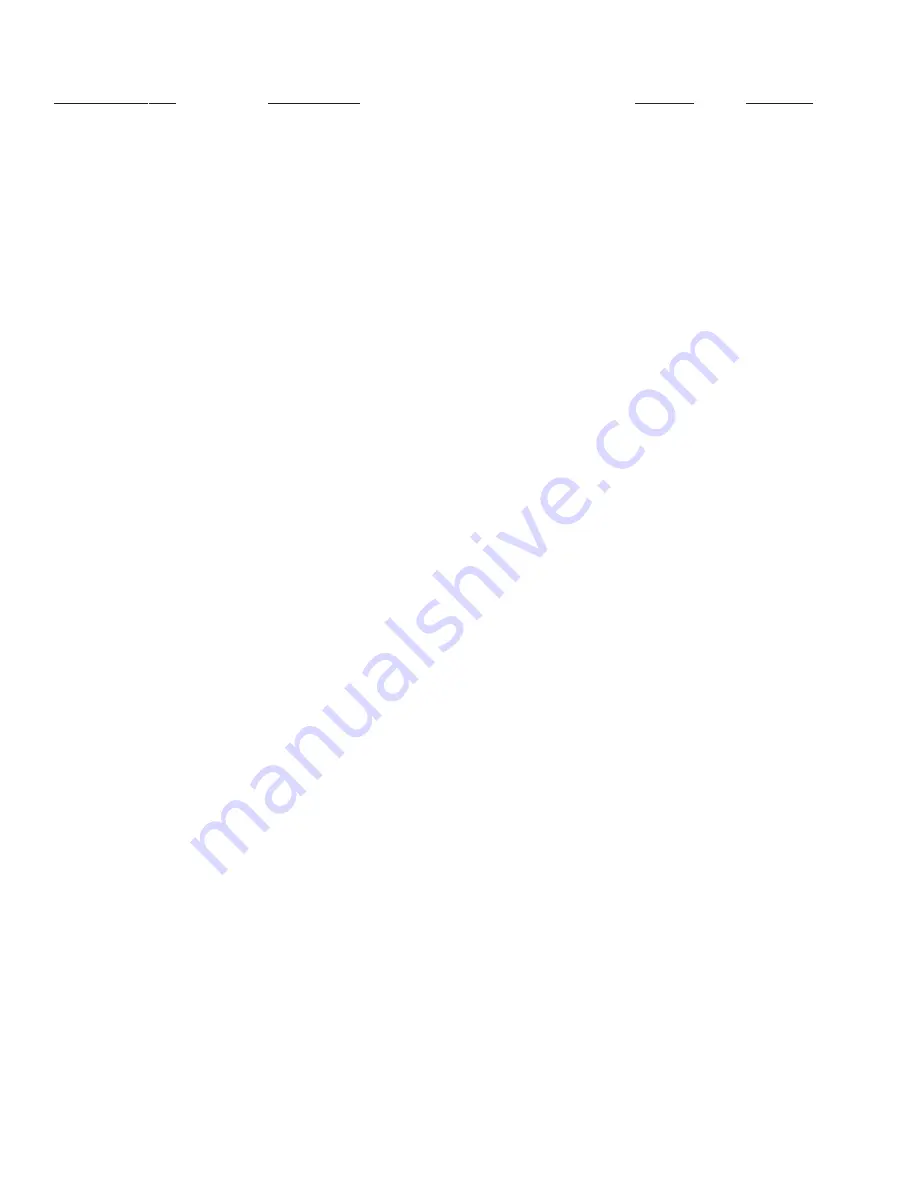
16
TROUBLESHOOTING IGNITION SYSTEM
Fault Messages and Lockout Status (* = stage number: 1, 2, 3, or 4)
FAULT DISPLAYED
DESCRIPTION
RED LED
LOCKOUT
“Display Fail”
Communications with UIM interrupted
Continuous
Auto Reset
Check communication cable to UIM. Try moving to other Internal Communications connector on MCB.
Also check the connectors where the cable is plugged in for best connecting wires.
“Comm. Fail Stg.*”
Communications with FCB interrupted
Continuous
Auto Reset
Same as above. Also try swapping FCB and UIM communications cables.
“Low AC Voltage”
Line voltage less than 90 vac
Continuous
Auto Reset
Check incoming power line for loss of voltage. May also be caused by a power line brown-out (momentary loss of voltage)
“Low 24VAC”
Voltage from transformer less than 18 vac
Continuous
Auto Reset
Check transformer output. Should be over 24vac. May be caused by excessive current drain or a faulty transformer
“Brown Out Reset”
Indicates a brown out reset occurred
- - - -
None
Caused by a momentary dip in voltage on the MCB +5vdc power bus. Contact factory. (Not considered a serious
problem if it only occurs on very rare occasions.)
“Timeout Reset”
Indicates a watchdog reset occurred
- - - -
None
Caused when the micro executes the software in an improper way. Contact factory. (Not considered a serious
problem if it only occurs on very rare occasions.)
“FCB Comm Timeout” FCB did not receive command from MCB
Continuous
SOFT
Caused when communications between the MCB and the FCB are interrupted. May occur when a surge of power on
a nearby device (i.e. arc welder) creates an EMI burst. Not a serious problem if it occurs rarely.
“No Flow”
Water is not flowing
Continuous
SOFT
Caused by the flow switch being open when it should be closed. Check water lines, pump, flow switch contacts, wiring.
“Blower Prov Stg*
Blower pressure is too low it they should have been closed.
Continuous
SOFT
Check blower, switch contact, wiring, and for air leaks.
“Blocked Flue”
Flue is Blocked
Continuous
SOFT
Caused by the blocked flue switch contacts being open when they should have been closed. Check for flue blockage,
switch contacts, wiring.
“High Limit”
Outlet temp. exceeded high limit setpoint
Continuous
Auto Reset
Caused when the temperature of the outlet probe exceeds the high limit setpoint. This is an internal “software” limit
switch and not an actual device. Check that the over temperature is not being caused by improper setup or
operation of the boiler.
“ECO fault”
Outlet temp is too high
Flashing
HARD
Caused when the ECO (a thermostat) contacts in the Outlet probe are open when they should be closed. Fault may be due to
high outlet temperature, bad switch contacts in the ECO, or disconnected wiring. Note: The ECO can be checked by
disconnecting the outlet probe from the MCB and reading the resistance across the two active pins on the connector at the
end of the probe cable. The value should be approximately 0 ohms when the temperature of the probe is less than 220°F.
“Low Water”
Water level is too low
Flashing
HARD
Caused by the Low Water Cut Out device not closing its feedback switch contacts when it should. Check water line,
switch contacts, wiring, LWCO.
“Low Gas”
Gas pressure is too low
Flashing
HARD
Caused by the Low Gas switch being open when it should be closed. Check gas line, switch contacts, wiring.
“Powered Vent”
Power vent not running
Flashing
HARD
Caused by the Powered Vent device not closing its feedback switch contacts when it should. Could also be caused
by a problem with the relay output on the MCB. Check output to powered vent, switch contacts, wiring.
“High Gas Stg*”
Gas pressure too high
Flashing
HARD
Caused by the High Gas switch being open when it should be closed. Check gas line, switch contacts, wiring.
“Inlet Probe”
Inlet probe shorted or open
Flashing
HARD
Caused when the thermistor in the probe or the wiring to the probe is shorted or disconnected. Check the probe.
Note: The thermistor and wiring can be checked by disconnecting the probe from the MCB and reading the resistance
across the two active pins on the connector at the end of the probe cable. The value should be approximately 10K
ohms (value will change slightly with changes in temperature).
“Outlet Probe:”
Outlet probe shorted or open
Flashing
HARD
Caused when the thermistor in the probe or the wiring is shorted or disconnected. Check the probe. Note: the
thermistor and wiring can be checked by disconnecting the probe from the MCB and reading the resistance across
the two active pins on the connector at the end of the probe cable. The value should be approximately 10K ohms
(value will change slightly with changes in temperature).
“Tank Probe”
Tank (Remote) probe shorted or open
Flashing
HARD
Caused when the thermistor in the probe or the wiring is shorted or disconnected. Check the probe. Note: the
thermistor and wiring can be checked by disconnecting the probe from the MCB and reading the resistance across
the two active pins on the connector at the end of the probe cable. The value should be approximately 10K ohms|
(value will change slightly with changes in temperature).
“Igniter Stg*”
Igniter current is too low
Flashing
HARD
Caused by a low current draw problem with the igniter. This may occur if the igniter is old, damaged, or disconnected
and no longer draws the proper level of current. This condition will affect the ability of the igniterto get hot enough to
fire the gas properly. Check the igniter and its associated wiring.
“Igniter Pwr Stg*”
Improper power applied to the igniter circuit
Flashing
HARD
Caused by improper line power being applied to the igniter circuitry. Check line connections. Paying particular attention to
the earth ground connection. Also check that line voltage does not exceed 132 VAC RMS.
“Igniter Hdwr Stg*”
Hardware problems with igniter circuit
Flashing
HARD
Summary of Contents for 1000 SERIES 100
Page 3: ...3 GENERAL SAFETY...
Page 6: ...6 CONNECTION DIAGRAM...
Page 7: ...7...
Page 8: ...8 SCHEMATIC DIAGRAM VB VW 500 750 1000 SCHEMATIC DIAGRAM...
Page 9: ...9 LIGHTING OPERATION INSTRUCTIONS FOR MODELS VB VW 500 750 AND 1000...
Page 20: ...20 NOTES...
Page 21: ......
Page 22: ...22 NOTES...