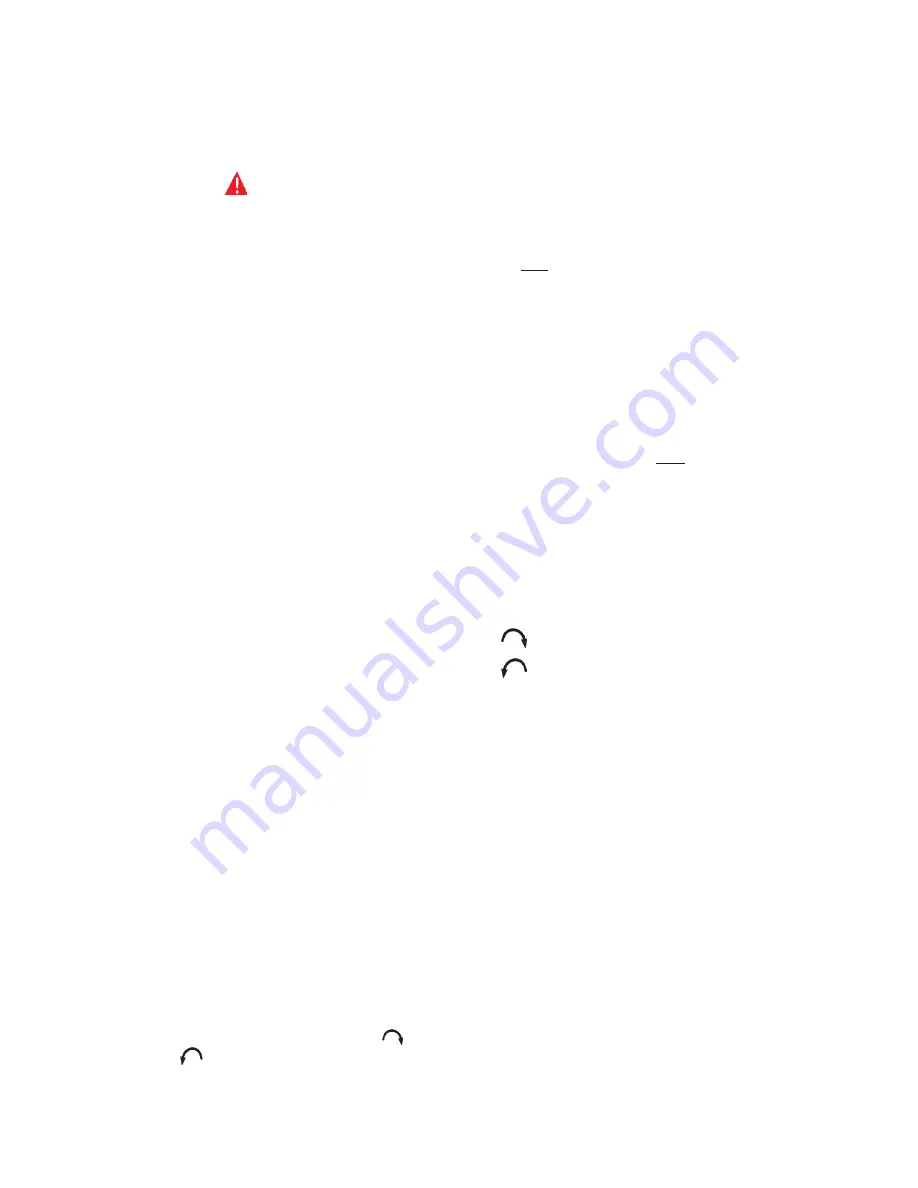
21
5. Check the vent system seams and joints and ensure that there is no
discharge of flue products into the room.
6. Check the input rate.
For appliance installation locations with elevations above 6500 feet
(1982 meters) refer to HIGH ALTITUDE INSTALLATIONS section of this
manual.
a. Attach a pressure gauge (manometer) to the manifold pressure tap
(Figure 16) and refer to Table 4, page 20 for correct pressure.
b. Use this formula to “clock” the meter. Be sure other gas consuming
appliances are not operating during this interval.
3600
X H = Btuh
T
Should it be necessary to adjust the gas pressure to the burner, to obtain
the full input rate, the steps below should be followed:
T = Time in seconds to burn 1 cubic foot of gas. (With a stopwatch read
the gas meter and measure the amount of time required for the
heater to consume 1 cubic foot of gas.)
H = Heating value of gas (in Btu’s per cubic foot of gas).
Btuh = Actual heater input rate, in Btuh.
EXAMPLE: (Using BTH-150 heater)
T = 25.25 seconds
H = 1050 Btu/ft.
3
BTUH = ?
For high altitude installations, compare result to the derated input required
for the elevation at the installation location.
c. Remove the pressure regulator cover screw (Figure 16) and adjust
the pressure by turning the adjusting screw with a small
screwdriver. Do not exceed 4.0" (1 kPa) natural gas models and
10.0" W.C. (2.5Kpa) on the propane models.
Clockwise to increase gas pressure and input rate.
Counterclockwise to decrease gas pressure and input rate.
d. “Clock” the meter as in step (b) above.
e. Repeat steps (c) and (d) until the specified input rate is achieved.
f . Turn the manual gas valve to “OFF”. Replace the pressure regulator
cover screw. Remove the pressure gauge or manometer from the
manifold pressure tap. Replace the set screw in the manifold pressure
tap. If the gas pressure regulator cannot be adjusted to give the full
input rating with sufficient gas pressure at the valve, check to ensure
the unit is equipped with the correct orifice.
ADJUSTMENT PROCEDURE
INITIAL START-UP - 199 AND 250 MODELS
Main line gas pressure to the water heater for natural gas should be
between a maximum of 10.5" (2.59Kpa for natural gas) W.C. (14.0"/3.45Kpa
for propane) and a minimum as shown in Table 4: that is, for Natural Gas 4"
(.98Kpa) W.C. and 9.0" (1.97Kpa) for Propane Gas. The inlet gas pressure
must not exceed the maximum value. A service regulator must be installed
within 10' (305 cm) of the unit.
The BTH 199 and 250 models incorporate a new gas control, which operates
at 0"W.C. (0kPa) for both natural and propane gas. These models are
configured prior to being shipped from the factory and no adjustments are
necessary prior to startup. The controller monitors the air-flow and makes
adjustments to the fan speed which in effect controls the amount of gas
flow. Therefore, the unit will self-adjust to acquire the correct amount of
input.
Once the unit is installed and filled with water and the inlet pressures
confirmed, simply turn the switch "on" and observe operation. Cycle the
unit "off" and "on" several times to ensure proper operation.
OPERATING INSTRUCTIONS
IMPORTANT
IT IS RECOMMENDED THAT A QUALIFIED SERVICE TECHNICIAN PERFORM
THE INITIAL FIRING OF THE HEATER. AT THIS TIME THE USER SHOULD ASK
THE TECHNICIAN ANY QUESTIONS IN REGARD TO THE OPERATION AND
MAINTENANCE OF THE UNIT.
CAUTION
BEFORE PROCEEDING WITH THE OPERATION OF THE UNIT, MAKE SURE
HEATER AND SYSTEM ARE FILLED WITH WATER AND ALL AIR IS EXPELLED
FROM HEATER AND PIPING.
NEVER OPERATE THE HEATER WITHOUT FIRST BEING CERTAIN IT IS FILLED
WITH WATER AND A TEMPERATURE AND A PRESSURE RELIEF VALVE IS
INSTALLED IN THE RELIEF VALVE OPENING OF THE HEATER. DO NOT
ATTEMPT TO OPERATE HEATER WITH COLD WATER INLET VALVE CLOSED.
FILLING:
1. Close the heater drain valve.
2. Open a nearby hot water faucet to permit the air in the system to
escape.
3. Fully open the cold water inlet pipe valve allowing the heater and
piping to be filled.
4. Close the hot water faucet as water starts to flow.
5. The heater is ready to be operated.
THE MAIN MANUAL GAS SHUTOFF VALVE MUST HAVE BEEN CLOSED
FOR AT LEAST FIVE (5) MINUTES. THIS WAITING PERIOD IS AN IMPORTANT
SAFETY STEP. ITS PURPOSE IS TO PERMIT GAS THAT MIGHT HAVE
ACCUMULATED IN THE COMBUSTION CHAMBER TO CLEAR. IF YOU DETECT
GAS AT THE END OF THIS PERIOD, DO NOT PROCEED WITH LIGHTING.
RECOGNIZE THAT GAS ODOR, EVEN IF IT SEEMS WEAK, MAY INDICATE
THE PRESENCE OF ACCUMULATED GAS SOMEPLACE IN THE AREA WITH
A RISK OF FIRE OR EXPLOSION. SEE THE FRONT PAGE FOR STEPS TO BE
TAKEN.
DO NOT USE THIS HEATER IF ANY PART HAS BEEN UNDER WATER.
IMMEDIATELY CALL A QUALIFIED SERVICE TECHNICIAN TO INSPECT THE
HEATER AND TO REPLACE ANY PART OF THE CONTROL SYSTEM AND
ANY GAS CONTROL WHICH HAS BEEN UNDER WATER.
LIGHT THE UNIT IN ACCORDANCE WITH THE OPERATING INSTRUCTIONS
LABEL ATTACHED TO THE HEATER.
THESE INSTRUCTIONS ARE REPEATED IN THE LIGHTING AND OPERATING
LABEL ILLUSTRATION ON PAGE 20 IN THIS MANUAL.
ADJUSTMENT PROCEDURE
INITIAL START-UP - 120 AND 150 MODELS
Main line gas pressure to the water heater for natural gas should be
between a maximum of 10.5" (2.59Kpa for natural gas) W.C. (14.0"/3.45Kpa
for propane) and a minimum as shown in Table 4: that is, for Natural Gas,
4.8 (1.18Kpa) W.C. and 8.5" (2.08Kpa) for Propane Gas. The inlet gas
pressure must not exceed the maximum value. A service regulator must be
installed within 10' (305 cm) of the unit.
1. Check gas line pressure with a manometer.
2. Check manifold pressure (see Table 4, page 20) using a pressure
gauge (manometer) connected to the manifold pressure tap on the
gas control valve, (Figure15).
If full rate adjustment is required, remove cover screw from top of the
gas control valve, (Figure 15).
Using a small screwdriver, turn adjusting screw clockwise
to increase
or counterclockwise
to decrease gas pressure to obtain 4.0" (1 kPa)
for natural gas and 10.0" W.C. (2.5 Kpa) for L.P. Gas.
3. Cycle the burner on and off several times to check its operation.
4. Check the operation of the limit and operating controls.
3600
X 1050 = 150,000 Btuh (44 Kw)
25.25