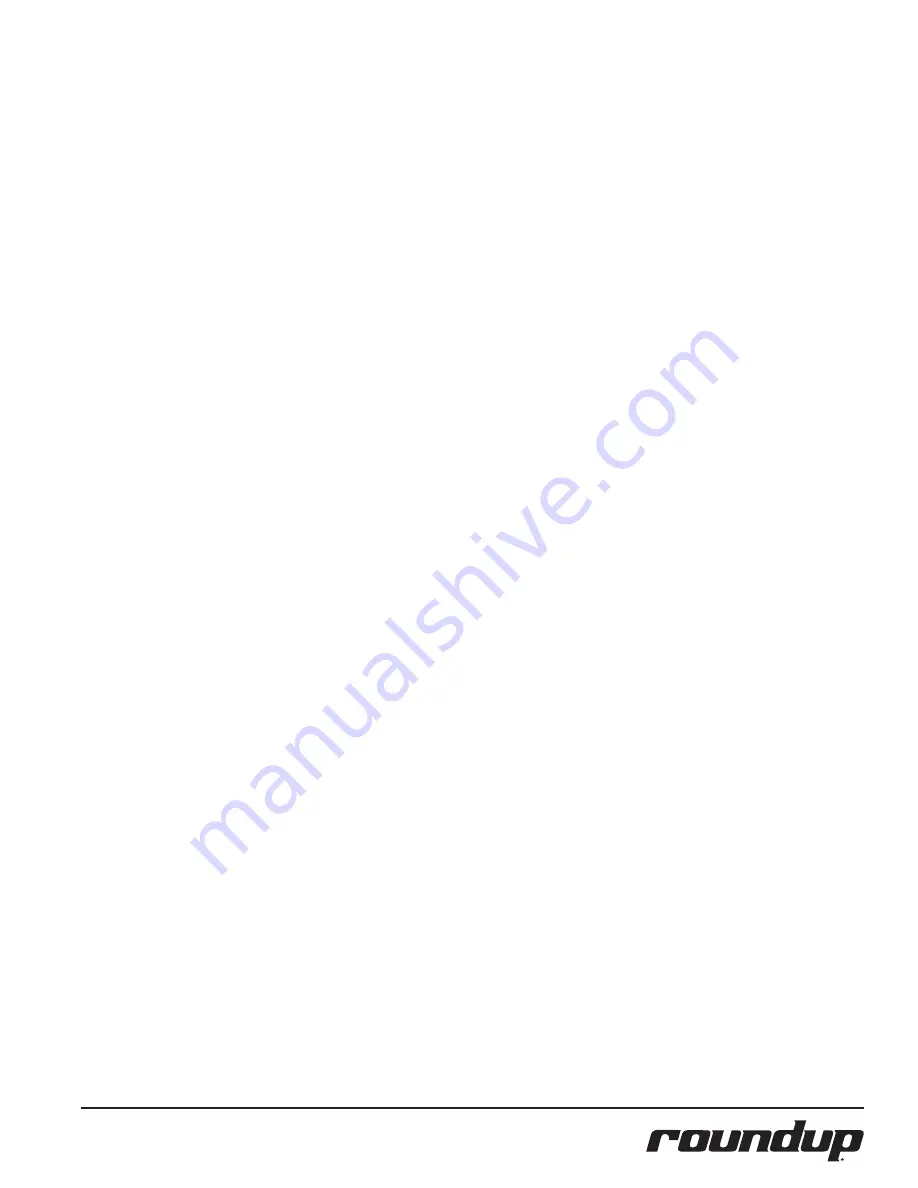
3
P/N 1010698 Rev. I 03/12
imporTanT SafeTy
informaTion
Use the following guidelines for safe opera-
tion of the unit.
•
Read all instructions before using
equipment.
•
For your safety, the equipment is fur-
nished with a properly grounded cord
connector. Do not attempt to defeat
the grounded connector.
•
Install or locate the equipment only
for its intended use as described in
this manual. Do not use corrosive
chemicals in this equipment.
•
Do not operate this equipment if it
has a damaged cord or plug, if it is
not working properly, or if it has been
damaged or dropped.
•
This equipment should be serviced by
qualified personnel only. Contact your
nearest Authorized Service Agency for
adjustment or repair.
•
Do not block or cover any openings on
the unit.
•
Do not immerse cord or plug in water.
•
Keep cord away from heated surfaces.
•
Do not allow cord to hang over edge
of table or counter.
•
Turn the power off, unplug the power
cord, and allow unit to cool down
before performing any service or
maintenance on the unit.
•
The procedures in this manual may
include the use of chemical products.
These chemical products will be
highlighted with bold face letters fol-
lowed by the abbreviated HCS (Hazard
Communication Standard). See Hazard
Communication Standard manual for
the appropriated Material Safety Data
Sheets (MSDS).
•
The equipment should be grounded
according to local electrical codes to
prevent the possibility of electrical
shock. It requires a grounded recep-
tacle with separate electrical lines,
protected by fuses or circuit breaker of
the proper rating.
•
All electrical connections must be in
accordance with local electrical codes
and any other applicable codes.
•
Do not clean this appliance with a
water jet.
WarninGS
Be advised of the following warnings when
operating and performing maintenance on
this unit.
•
If the supply cord is damaged, it must
be replaced by the manufacturer or its
service agent or a similarly qualified
person in order to avoid a hazard.
•
Do not modify the power supply cord
plug. if it does not fit the outlet, have
a proper outlet installed by a qualified
electrician.
•
Do not use an extension cord with this
appliance.
•
Electrical ground is required on this
appliance.
•
Check with a qualified electrician if
you are in doubt as to whether the
appliance is properly grounded.
•
If a chemical cleaner is used, be sure
it is safe to use on cast aluminum.
Observe all precautions and warnings
on product label.
•
Inspection, testing, and repair of elec-
trical equipment should only be per-
formed by qualified service personnel.
•
This equipment is to be installed to
comply with the basic plumbing code
of the Building Officials and Code
Administrators, Inc. (BOCA) and the
Food Service Sanitation Manual of the
Food and Drug Administration (FDA).
•
On direct water hook-up units, water
pressure must not exceed 30 psi (2.1
kg/cm2 or 207 kPa). Higher water
pressures will cause poor perfor-
mance, excessive condensation, and
flooding of the Steam Generator. To
reduce water pressure, install a water
pressure regulator and set water pres-
sure to 20–30 psi (1.4–2.1 kg/cm2 or
138–207 kPa). Contact your equip-
ment supplier to purchase a Water
Pressure Regulator.
•
To ensure proper steaming character-
istics, some calcium/mineral deposits
must be present on the generator
surface. If, during cleaning, the surface
does become free of calcium/mineral
deposits, add plain tap water to the
surface and allow it to boil off. This
may have to be repeated several times
to ensure proper steaming characteris-
tics by creating a thin layer of deposits
on the surface.
•
Do not use a sanitizing solution or
abrasive materials. The use of these
may cause damage to the stainless
steel finish.
•
Chlorides or phosphates in clean-
ing agents (e.g. bleach, sanitizers,
degreasers or detergents) could cause
permanent damage to stainless steel
equipment. The damage is usually in
the form of discoloration, dulling of
metal surface finish, pits, voids, holes,
or cracks. This damage is permanent
and not covered by warranty.
•
The following tips are recommended
for maintenance of your stainless steel
equipment:
•
Always use soft, damp cloth for
cleaning, rinse with clear water
and wipe dry. When required,
always rub in direction of metal
polish lines.
•
Routine cleaning should be done
daily with soap, ammonia deter-
gent, and water.
•
Stains and spots should be
sponged using a vinegar solution.
•
Finger marks and smears should be
rubbed off using soap and water.
•
Hard water spots should be
removed using a vinegar solution.