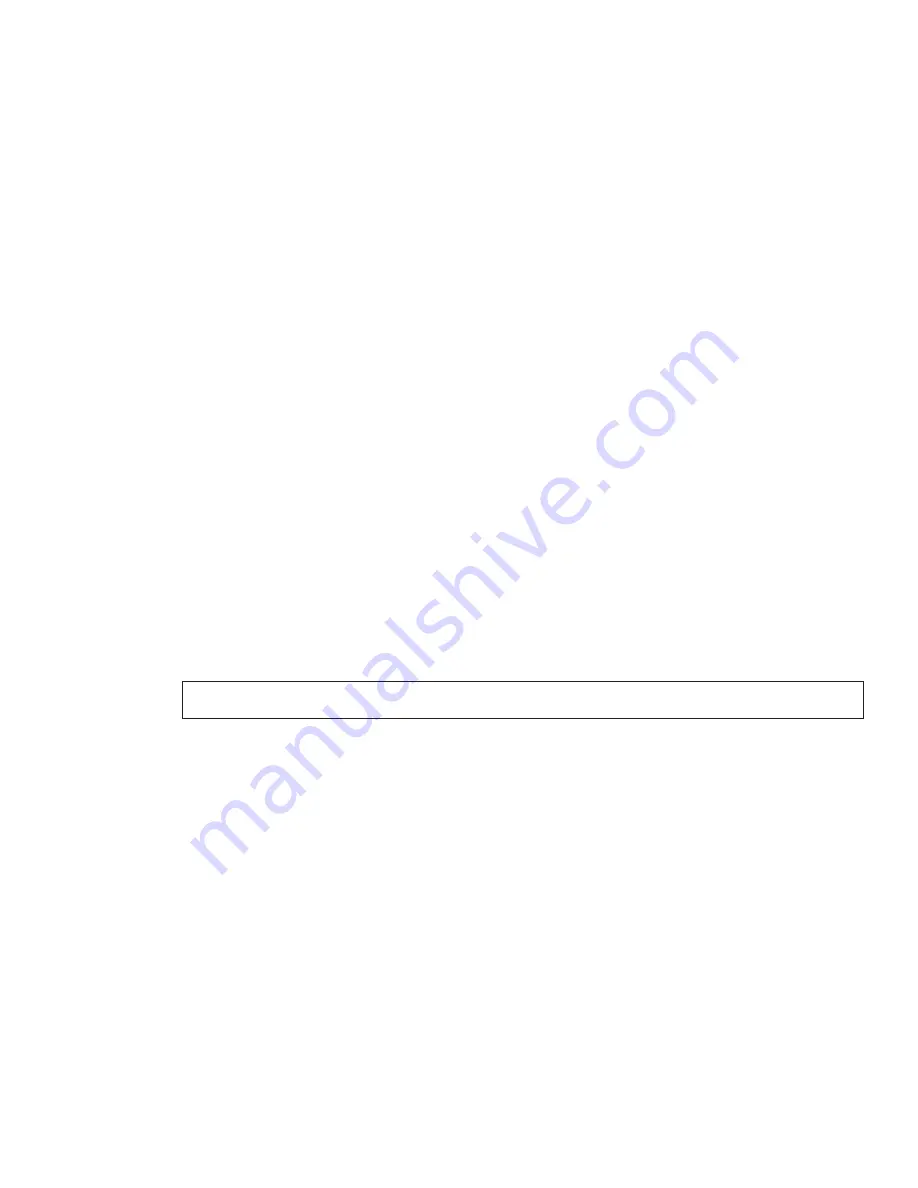
17
3.11 HLL INSTALLATION ON 3M STANCHION POSTS
:
When the 3M™ DBI-SALA® Temporary Cable HLL system is installed on 3M Stanchion systems (I-beam stanchion,
perpendicular I-beam stanchion, pour-in-place stanchion, stud/rebar stanchion) the following accommodations must be
made:
•
The maximum span length of an HLL used between stanchion posts is 60 ft.
•
Ensure each stanchion is properly installed following the manufacturer’s instructions and the structure meets the
anchorage requirements specified in table 1.
•
A common setup involving 3M Stanchion Posts places the HLL at a height 3 ft. (0.9 m) above the walking surface. A
6 ft. (1.8 m) lanyard used in combination with the Stanchion HLL System can result in a Free Fall of 8 ft. (2.4 m). To
account for this increased Free Fall distance, 1 ft. (0.3 m) of additional Fall Clearance must be added to the values in
Figure 7 when a 6 ft. (1.8 m) lanyard is used to connect to a 3 ft. (0.9 m) high Stanchion HLL system.
•
If the system setback from the fall edge is greater than the height of the HLL above the working surface, use fall
clearance criteria specified in section 3.3 plus an additional 5 ft. (1.5 m) fall clearance to account for potential
deflection of the post due to side-loading.
3.12 USER CAPACITY GREATER THAN 310 LB. (140 KG) GUIDELINES:
If a user’s total weight, including tools and clothing, exceeds the 310 lb. (140 kg) capacity limit, adaptations can be made
to accommodate a single user weighing up to 420 lb. (190 kg), including tools and clothing.
For users weighing between 310 lb. and 420 lb. (140 kg and 190 kg), including tools and clothing, the following guidelines
must be followed:
1. Capacity is reduced to one user per span.
2. Ensure the connecting subsystem is rated for total weight of the user.
3. Use the two-user Fall Clearance values from the 310 lb. (140 kg) capacity Fall Clearance charts, but apply to a single
user that weighs up to 420 lb. (190 kg).
3.13 HLL INSTALLATION:
Step 1.
Determine the locations of the anchorages and evaluate their strengths in accordance with the anchorage
requirements listed in Table 1. Determine the span length and evaluate the required clearance using Figure 7 or
8. Figures 7 and 8 apply to one or two users connected to the system.
Step 2.
Press on the button (A) on top of the housing and hold it down to pay out the required amount of lifeline by
pulling out the line. Ensure the crank handle is not connected to any output during this operation. When the
button is released, it will spring back up and the lifeline will lock in place. If the lifeline does not lock, do not
use. The unit must be returned to an authorized dealer for service. See Figure 13.1.
Step 3.
Install the horizontal lifeline to end anchorage connectors using the carabiners provided. See Figure 2. If the EZ-
Line is installed as a multi-span system, a Zorbit energy absorber must be added to the end of the system as
shown in Figure 2. Refer to manufacturer’s instructions provided with the anchorage connectors for installation
requirements. The horizontal lifeline system may be secured directly to the anchorage if the anchorage
incorporates a connecting element that meets the requirements specified in table.
;
Zorbit Energy Absorber: Mount so Zorbit can pivot and move freely as shown in Figure 2. Do not rigidly
mount Zorbit HLL Energy absorber to structure or stanchion because this may cause failure due to bending.
Step 4:
Connect the crank handle to the top output and remove excess slack by rotating clockwise. The lifeline must be
tensioned until a “click” and a slight rotation of the crank arm relative to the crank body occur. When the crank
handle is released, it will return to its original position in line with the crank body. In the special case of the HLL
installed on 3M Roof-Top Anchors, the tensioning procedure must be modified to prevent pre-deployment of the
Roof-Top Anchor. For these applications, the wire rope should only be tensioned enough to raise it above the
roof surface 2-3 inches and allow free passage of the attachment O-rings. See Figure 13.2.
Step 5:
If slack is needed to make an adjustment to the system, or for ease in removing the system, connect the crank
handle to the top output and rotate clockwise for about 20 degrees (20°), press the top button simultaneously
and allow the crank handle to rotate counterclockwise. See Figure 13.3.
Step 6:
After use, retract the lifeline back into the casing by connecting the crank handle to the bottom output and
rotating it counterclockwise.
See Figure 13.4.
4.0 USE
4.1
BEFORE EACH USE:
Verify that your work area and Fall Protection system meet all criteria defined in Section 2 and that
a formal Rescue Plan is in place. Inspect the HLL System per the ‘User’ inspection points defined on the “Inspection &
Maintenance Log” (Table 2). If inspection reveals an unsafe or defective condition, do not use the system. Remove the
system from service, clearly tag it “DO NOT USE”, and either destroy the system or forward to 3M for replacement or
repair. See section 5 for more information.
4.2 CONNECTING TO THE HLL SYSTEM:
Appropriate Fall Protection equipment must be worn when installing or connecting
to the HLL System. Connect your Fall Protection system to one of the attachment O-rings on the HLL System. When using
an Energy Absorbing Lanyard, the length of the connecting subsystem should be kept as short as possible in order to
reduce the potential free fall and required fall clearance.
Summary of Contents for DBI SALA EZ-Line
Page 2: ...2 2 D B C E A G F D 3 1 W 2 FC 4 5 A B C D E F G A B C...
Page 3: ...3 6 X Y...
Page 7: ...7 10 1 2 11 A B B A...
Page 8: ...8 12 A A 13 1 A B 2 3 2 1 3 4...