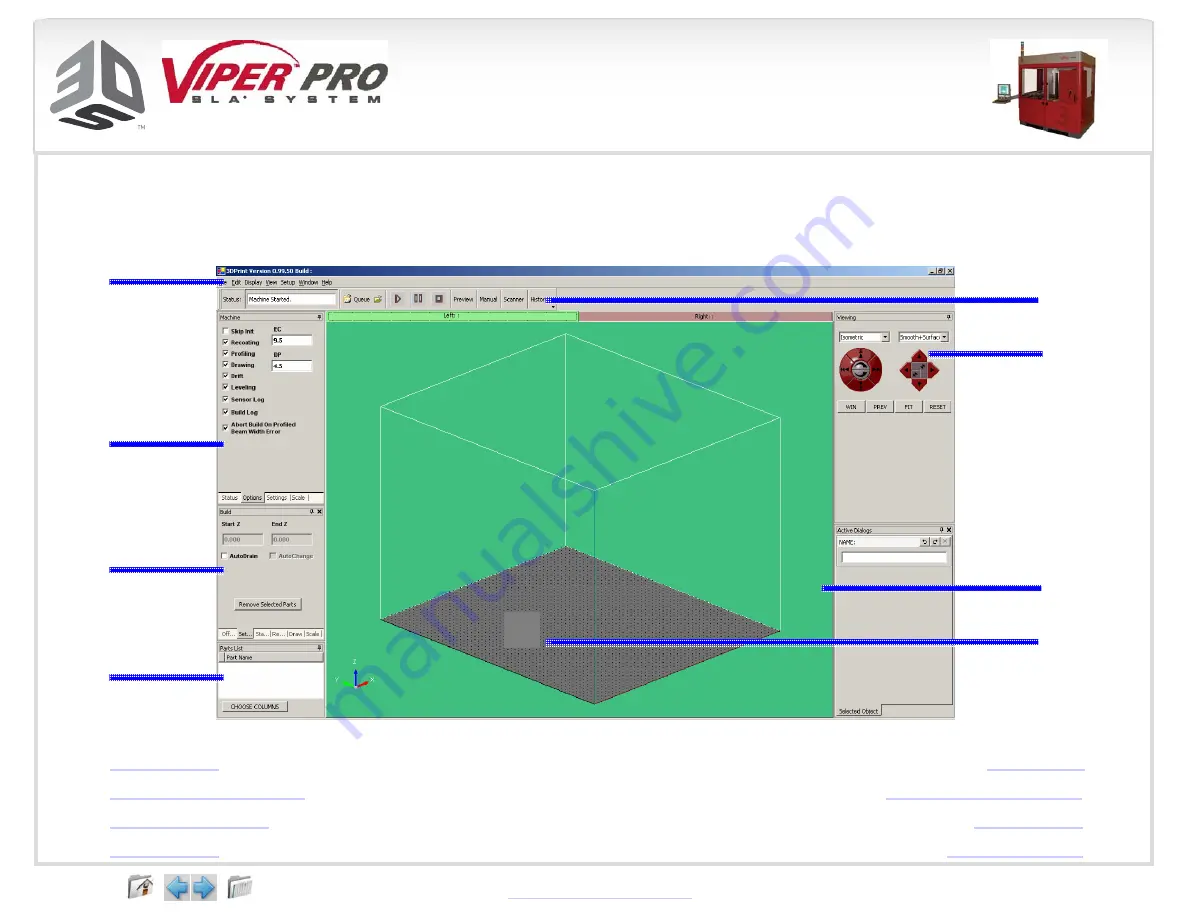
35
s o f t w a r e o v e r v i e w
Software Overview
The next few pages describe the 3DPrint
TM
components, their location in the software, and their
specific tasks.
Menu
Bar
Machine
Window
Build
Window
Parts
List
Main Screen of the 3DPrint
TM
Software
Tool
Bar
Viewing
Controls
View
Port
View
Object
70696 Revision 1C 27-Aug-08