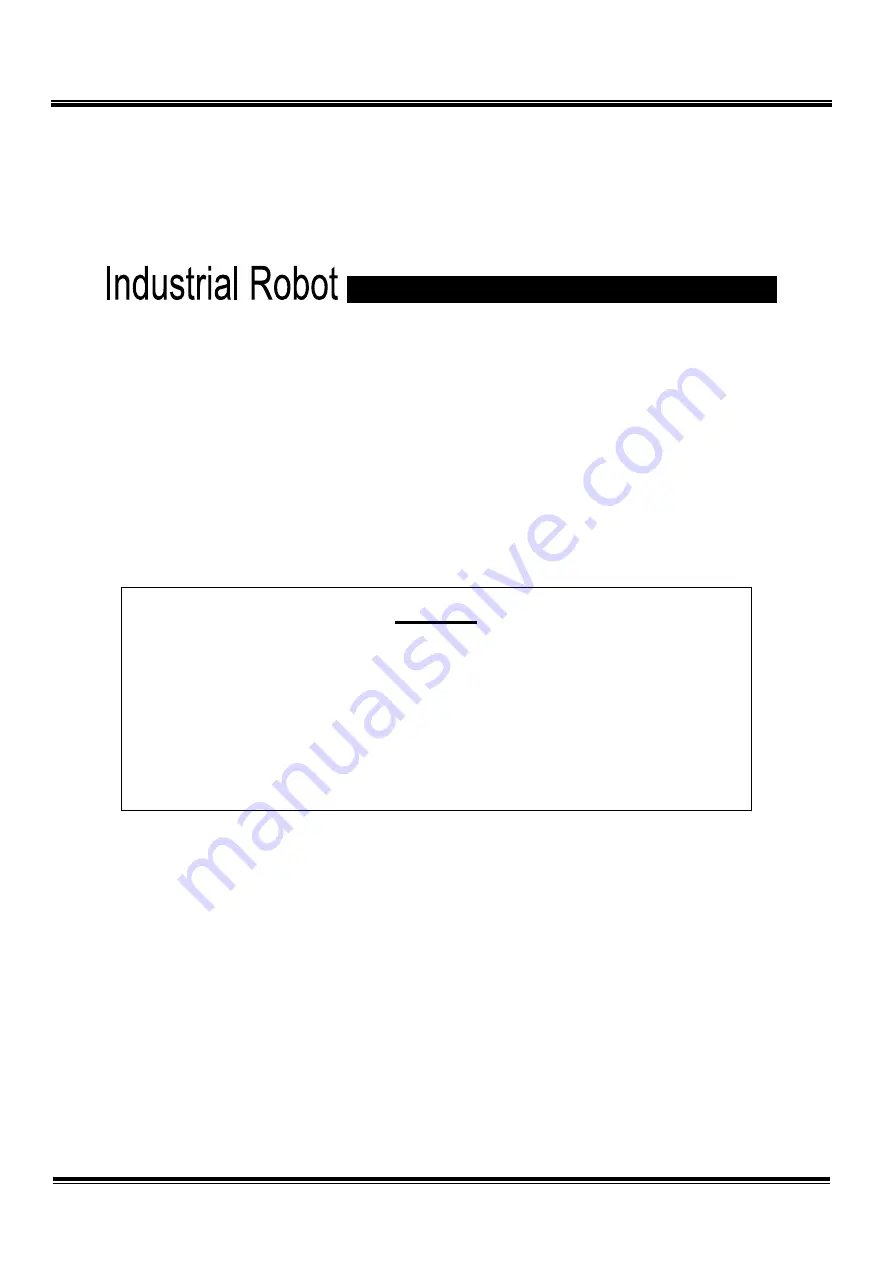
STE 80765–0
TH850A/TH1050A–IP/TS2100
INSTRUCTION MANUAL
DUST- & DRIP-PROOF TYPE
INDUSTRIAL ROBOT SPECIFICATIONS
Notice
1. Make sure that this instruction manual is delivered to the final
user of Toshiba Machine’s industrial robot.
2. Before operating the industrial robot, read through and
completely understand this manual.
3. After reading through this manual, keep it nearby for future
reference.
April, 2009
TOSHIBA MACHINE CO., LTD.
NUMAZU, JAPAN