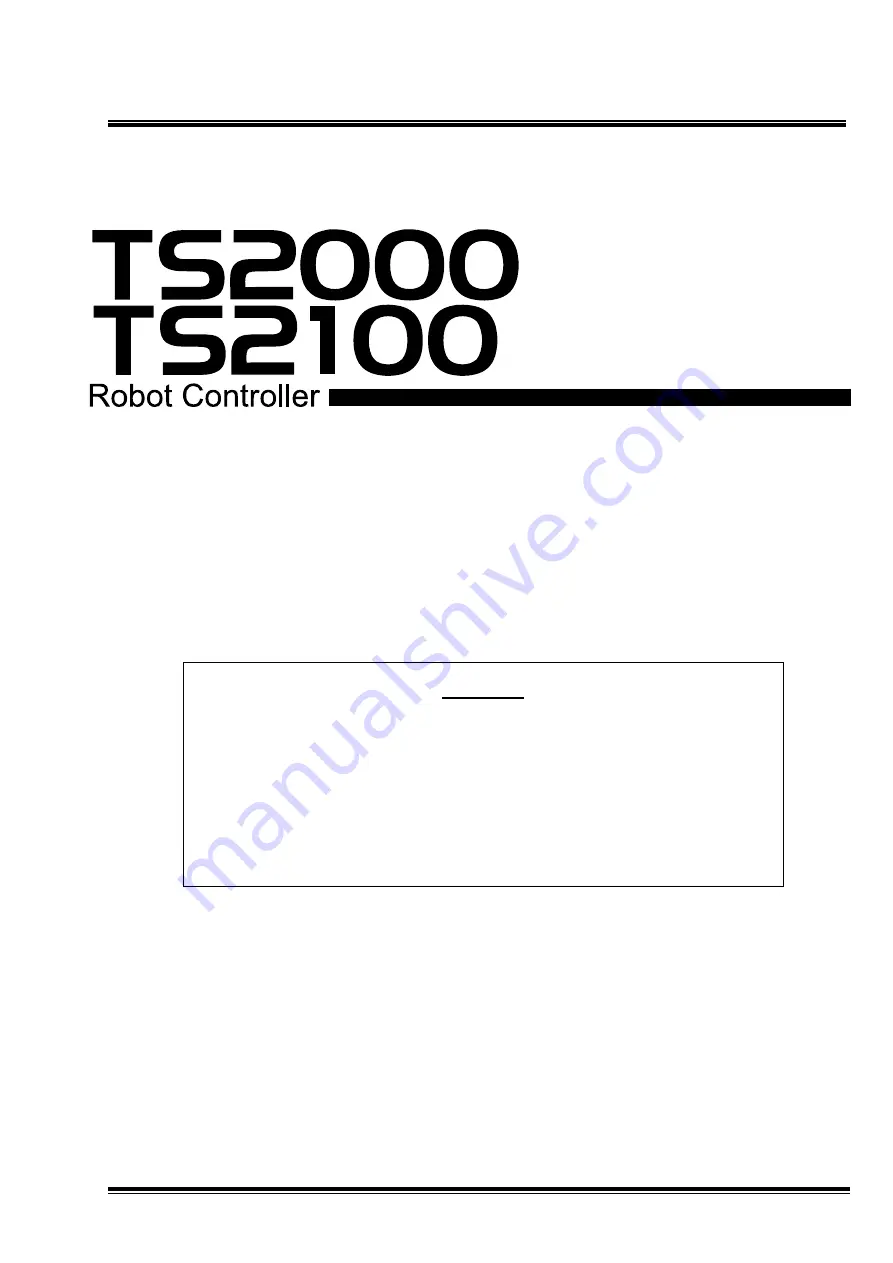
STE 71367–9
INSTRUCTION MANUAL
TS2000/TS2100 ROBOT CONTROLLER
INTERFACE MANUAL
Notice
• Make sure that this instruction manual is delivered to the
final user of Toshiba Machine's industrial robot.
• Before operating the industrial robot, read through and
completely understand this manual.
• After reading through this manual, keep it nearby for future
reference.
TOSHIBA MACHINE CO., LTD.
NUMAZU, JAPAN