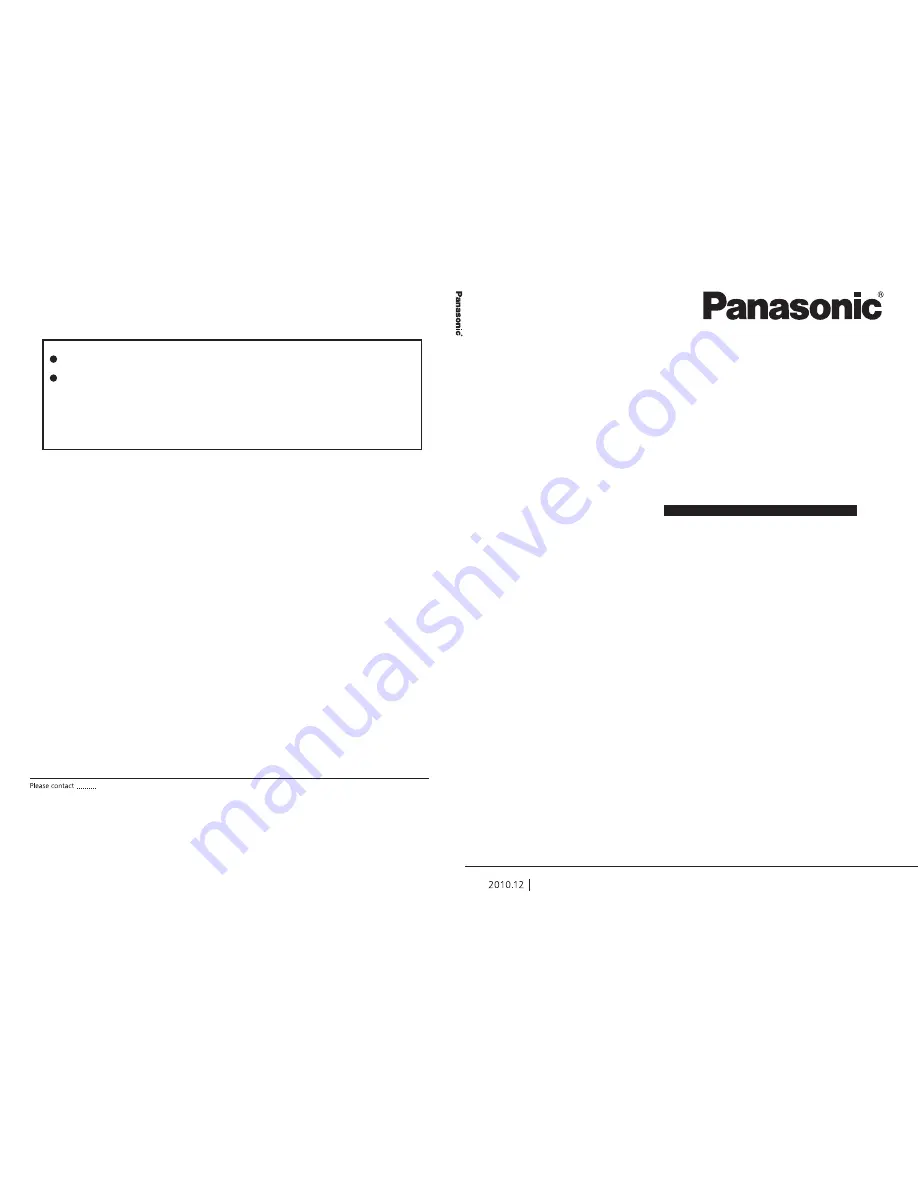
panasonic-electric-works.net/sunx
Elevator Door Controller AAD03011 Instruction Manual
8A3 708 0000 3
Panasonic Electric Works SUNX Shanghai
Panasonic Electric Works SUNX Shanghai
©
Panasonic Electric Works SUNX Co., Ltd. 2010
8A3 708 0000 3
PRINTED IN CHINA
Panasonic Electric Works SUNX Shanghai Co., Ltd.
http://panasonic-electric-works.net/sunx
T52-3, No.1510, Chuanqiao Road, Jinqiao Export Processing Zone,
Pudong New Area, Shanghai, China
Phone: +86-21-5032-3800 FAX: +86-21-5032-3866
Europe Headquarter: Panasonic Electric Works Europe AG
Rudolf-Diesel-Ring 2, D-83607 Holzkirchen, Germany
Phone: +49-8024-648-0
US Headquarter: Panasonic Electric Works Corporation of America
629 Central Avenue New Providence, New Jersey 07974 USA
Phone: +1-908-464-3550
Elevator Door Controller
AAD03011
Instruction Manual
[Support model]
·
AAD03011
Read this manual carefully before
attempting to operate the inverter
and store it for further reference.
ATTENTION
The inverter manufactured in our company is only applied to the elevator.
Use this equipment before ensuring the safety and application of the
elevator.
Always take safety precautions such as dual safety mechanism and
malfunction protection.
Failure to do so could lead to serious accident.